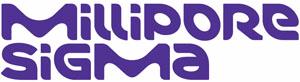
ABOUT MILLIPORESIGMA
The growing demand for new therapies, persistent pressure to reduce costs, and the clinical success of novel modalities are driving the biopharmaceutical industry to adopt new strategies to increase the speed, efficiency, and agility of manufacturing. A variety of approaches are available to address these imperatives.
Monoclonal antibodies (mAbs) and recombinant proteins have templated production workflows. Here, the focus is on exploring and integrating strategies defined by Biopharma 4.0 – the digital transformation to intensified, closed, connected, or continuous processing. For these companies, the key question is: “Where do I begin?”
In contrast, relatively new modalities such as mRNA and cell and gene therapy present different challenges. Cell and gene therapies are highly complex, lack a manufacturing template, and innovators must operate in a regulatory environment that continues to evolve. When developing and manufacturing mRNA-based therapeutics, among the most pressing objectives are to improve process efficiency and mRNA product stability.
For innovators of these novel modalities, access to new technologies and a breadth of expert services are critical success factors as they ask: “How can I improve my process?”
MilliporeSigma, the life science business of Merck KGaA, Darmstadt, Germany, empowers you to optimize and streamline your development and manufacturing processes. Whether you are producing mAbs and recombinant proteins, or highly complex, novel modalities, we will help you meet your goals for speed, efficiency, and agility.
We offer a convergent end-to-end portfolio of advanced, closed processing-ready technologies with extensive documentation for upstream and downstream operations, process analytical technologies (PAT), data analytics, automation and control software, contract testing and analytical development services, non-GMP environment labs, and CTDMO services for mAbs, high potency active pharmaceutical ingredients (HPAPIs), antibody drug conjugates (ADCs), mRNA, and lipid nanoparticle (LNP) formulation.
VIDEOS
HOT PRODUCTS
-
Perfusion at process development scale
The Mobius® Breez Microbioreactor is a 2 mL automated single-use perfusion cell culture platform designed to support gentle, adaptable, and reproducible cell processes.
-
Designed to purify biologics at clinical and process scale, the Mobius® FlexReady Solution with Smart Flexware® Assemblies is flexible, allowing you to have a single system for tangential flow filtration (TFF) at various scales.
-
To ensure optimum equipment uptime and regulatory compliance while mitigating risks, MilliporeSigma has developed System Service Reliance Plans; a complete range of services for your systems and equipment. These comprehensive service and support packages allow you to select a coverage level that best fit your needs
-
MilliporeSigma’s Mobius® single-use mixing solutions deliver advanced technology for mixing pharmaceutical ingredients from intermediate to final drug products and for the preparation of process solutions, such as buffers and media. Unlike traditional stainless-steel mixers, single-use mixers reduce downtime due to CIP, SIP, cleaning validation, and process engineering. Mobius® single-use mixing solutions also offer operational flexibility as they can be up and running in less than five minutes. They are capable of mixing speeds up to 1000 RPMs meeting the broadest range of mixing production requirements. Mobius® flexibility offers you a choice of just the right filter, connector, tubing options for your specific application and environment, including sterile interfaces, from fermentation to final fill. Sizes range from 10 L to 3000 L.
-
You’re developing lifesaving gene-modified cell therapies and need to manufacture lentiviral vector as quickly as possible. But scale-up and regulatory hurdles make the path to the clinic slow and labor intensive.
We're here to help.
-
From your bioreactor to final sterile filtration, the new NovaSeptum® GO sampling system lets you sample processes the way you want. Flexible formats and volumes adapt to your process for robust, reliable monitoring and quality assurance.
-
Cell culture media are important for process efficiency and mAb quality. Production media support initial cell growth and production, while the feeds replenish depleted nutrients required for cellular function and maintain and extend the production phase in fed-batch mode.
-
Cellvento® CHO media are designed to support growth and maintenance of specific CHO cell lines in suspension cell culture for expression of monoclonal antibodies and recombinant proteins. The new Cellvento® 4CHO-X Expansion Medium supports cell expansion including N-1 perfusion for Chinese Hamster Ovary (CHO) cell lines.
-
In recent years, the development of media used to expand and mature adult stem cells has greatly increased the success rate of adult stem cell therapy and the breadth of potential stem cell-based therapies. To obtain enough cells, ex vivo expansion has been utilized to ensure successful engraftment and economize the manufacture of both allogeneic and autologous therapies.
-
Bio4C ProcessPad™ software is a data collection, visualization, and analytics software platform that facilitates 21 CFR Part 11 compliance and enables bioprocess monitoring, lifecycle management, reporting, investigations, and continued process verification (CPV).
BROCHURES
- Viral Clearance Services
- AAV Production: Your AAV CDMO Partner, Every Batch, Every Milestone
- Conical Tube Sampling Unit
- Ensuring Success With Manufacturing Risk Assessment
- API Stability Combined With Rapid Disintegration
- Chemically Defined Cell Culture Feed
- Stabilizer Brochure
- Reducing Risk And Improving Synthesis Outcomes In Drug Discovery
- Digital Data: Your Roadmap To Supply Chain Efficiency
- CDMO Services: Customized mRNA-LNP Solutions
WEBINARS AND PODCASTS
PRODUCT GUIDES, DATA SHEETS & APPLICATION NOTES
- Conical Tube Sampling Unit
- Real-Time Monitoring Of Solvent Clearance By TFF In The ADC Process
- A Novel Approach To Improving AAV Titers
- Implementation Of Multi-Column Chromatography Systems
- Advantages Of Spray-Dried Mannitol In Roll Compaction
- Chemically Defined Cell Culture Feed
- Enhanced Solubility Through API Processing
- Multi-Attribute Method Analysis In Biopharmaceutical Development
- Monitoring Microbial Contamination Of Mammalian Cell Cultures
- Digital Data: Your Roadmap To Supply Chain Efficiency
NEWS
- Simtra BioPharma Solutions And MilliporeSigma Announce Strategic Alliance For Antibody Drug Conjugates Drug Substance And Drug Product Manufacturing Services
- MilliporeSigma Invests $76 Million To Expand ADC Manufacturing For Novel Cancer Therapies
- MilliporeSigma Announces Siren Biotechnology As Winner Of Its North American Advance Biotech Grant
- MilliporeSigma Expands Its Optimized VirusExpress® Platform For Lentiviral Vectors, Further Enhancing Quality And De-Risking Cell And Gene Therapy Manufacturing
- MilliporeSigma Announces Support Of SaudiVax In Becoming First Developer And Manufacturer Of Halal Vaccines And Biotherapeutics In Saudi Arabia
- MilliporeSigma To Manufacture Next-Generation Biotherapeutics For Alteogen
- MilliporeSigma Announces Organizational Transformation To Strengthen CDMO Offering And Accelerate Future Growth
- MilliporeSigma Accelerates Readiness Of Bioprocessing Facility Of The Future
CONTACT INFORMATION
MilliporeSigma
400 Summit Drive
Burlington, MA 01803
UNITED STATES
Phone: 978-762-5100
NAVIGATING THE EMERGING BIOTECH ECOSYSTEM
FEATURED ARTICLES
-
Raman spectroscopy revolutionizes ADC manufacturing by enabling real-time monitoring of solvent clearance. Discover how it enhances process control, ensures regulatory compliance, and supports the production of high-quality therapeutics.
-
Explore the use of Next Generation Sequencing (NGS) to proactively screen raw materials in biopharmaceutical manufacturing, which aims to reduce viral contamination risks from animal-derived reagents.
-
Explore how molecular-based technologies, including PCR and Next Generation Sequencing, are transforming viral safety testing by offering broader, more effective alternatives to traditional animal-based methods like in vivo assays.
-
Explore the growing role of highly potent active pharmaceutical ingredients in oncology and Antibody-Drug Conjugates to highlight manufacturing challenges, safety protocols, and opportunities for CDMOs.
-
The biopharmaceutical industry is transforming by shifting to continuous and intensified upstream bioprocesses, which are driven by evolving demands. Discover the key goals and innovations shaping this transition for modern healthcare.
-
Monoclonal antibody manufacturing is advancing to boost efficiency, cut costs, and expand access, driven by innovation, demand, and the rise of biosimilars.
-
Integrating Process Analytical Technology into validated GMP processes is complex and costly, which requires thorough validation of equipment and cleaning methods. Explore more about PAT's role in ADC production.
-
Navigating clinical trials for viral vector-based cell and gene therapies demands specialized expertise and regulatory insight. Learn how scientific acumen and strategic planning bring innovative therapies from lab to patient.
-
As demand for AAV-based therapies rises, optimizing production processes is essential. By utilizing existing technologies, tailored platforms, and optimized formulations, titers and productivity can be enhanced.
-
Discover how a multi-column chromatography system enhances resin utility and enables continuous bioprocessing with minimal surge tankage for agile multi-product facilities.
-
Compressed tablets are common oral solid dosages that contain the API and various excipients. Learn about the critical steps in selecting manufacturing methods and excipients to achieve the desired therapeutic effects and stability.
-
Pharmaceutical excipients like mannitol enhance formulation stability, flowability, and compressibility, which are crucial for robust tablets. Read how these properties improve patient compliance.
-
The RNA therapeutics and vaccines market has grown rapidly, driven by siRNA and mRNA technologies. Explore how these advancements are now being applied to cancer vaccines and innovative therapeutics.
-
AAV-based gene therapies, while promising, require rigorous quality control through advanced methodologies to ensure safety, efficacy, and regulatory compliance.
-
Ensuring adequate solubility is crucial for small molecule drugs' effectiveness. Find out how poor solubility remains a significant challenge, potentially hindering medications from reaching the market.
-
Explore why technology transfer is a critical component in mammalian biologic drug development and manufacturing with the essential guide to biologics tech transfer that covers key strategies, best practices, and critical considerations.
-
Analytics is a crucial element in biopharmaceutical development and manufacturing. Discover how Multi-Attribute Method (MAM) revolutionizes analytics to enhance quality control and regulatory compliance.
-
Mammalian cells are widely used to produce complex processed molecules. Explore a system that effectively detects microbial contamination in mammalian cell cultures and utilizes a newly formulated lysis buffer.
-
The evolving field of viral vector production, driven by advances in gene and cell therapies, is facing increasing regulatory scrutiny and analytical demands.
-
Explore Cell & Gene therapy (CGT) products now within scope of the ICH Q5A guidance, technologies that can replace traditional testing strategies, viral clearance studies expected for vector products, and more.