mAb Development And Manufacturing: Helpful Biosafety Testing Innovations Where And When You Need Them
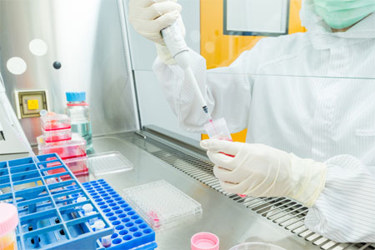
Monoclonal antibodies (mAbs) have long been a cornerstone of biopharmaceutical innovation, supported by mature manufacturing processes and rigorous biosafety protocols. Despite this maturity, the field continues to evolve, with manufacturers striving to enhance efficiency, reduce costs, and improve access to life-saving therapies. Efforts to increase production yields are vital for meeting growing demand and making treatments more affordable for healthcare systems and patients.
Innovations in formulation and delivery methods are broadening the reach of mAbs to more therapeutic areas and patient populations. Simultaneously, advances in antibody engineering—such as improving effector functions, stability, and half-life—are expanding therapeutic potential and durability. In upstream development, engineering of Chinese hamster ovary (CHO) cells focuses on refining product quality through better glycosylation and reduced host cell proteins.
The rise of next-generation antibody formats, including bispecifics and antibody-drug conjugates (ADCs), further drives the need for adaptable, efficient processes. As competition increases with the emergence of biosimilars, manufacturers face pressure to maximize the life cycle value of their products. Streamlining production timelines without compromising quality is essential. Biosafety testing must also keep pace, evolving alongside process innovation to ensure product safety and supply continuity. Together, these efforts support a more agile and resilient mAb manufacturing landscape.
Get unlimited access to:
Enter your credentials below to log in. Not yet a member of Bioprocess Online? Subscribe today.