Going From DNA To IND In 11 Months*
By Dominik Wegmann, Senior Director, Head of Mammalian Development Services programs, Lonza Visp and Matthew Minakowski, Director of Commercial Development for Mammalian Clinical Development, Lonza
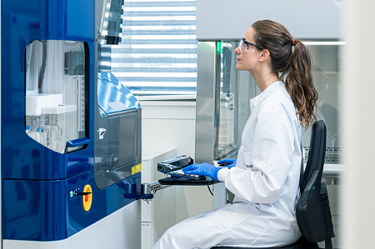
Biopharmaceutical companies are under increasing pressure to advance their molecules to first-in-human trials faster than ever before. For drug developers, this is a time-consuming, risky paradigm – on average, just one in every 1,000 of these molecules makes it out of Phase 1 trials.
Surmounting the various challenges that define the biopharmaceutical manufacturing space means stacking the odds in a project’s favor. One of the biggest ways a company can work to maximize their chances of success is in partnering with a contract development and manufacturing organization (CDMO) that possesses the expertise and resources to balance risk with speed-to-market while managing project costs.
In a recent webinar, “Ibex® Design - DNA to IND in 11 Months Guaranteed*,” experts from Lonza, a global partner to the pharmaceutical, biotechnology, and nutrition markets, convened to explore how it is able to guarantee customers five months from DNA to tox drug substance, and 11 months to Investigational New Drug Designation (IND) filling for antibodies, using its Ibex® Design 2.0 Program. Speakers for the webinar included:
- Matthieu Stettler, Senior Director, Head of Mammalian Development Services programs, Lonza Visp
- Matthew Minakowski, Director of Commercial Development for Mammalian Clinical Development, Lonza
The Ibex® Design 2.0 Program uses state-of-the-art cloning and expression technologies, coupled with Lonza’s approach of conducting parallel workflows that integrate its drug substance and drug product services, to achieve reduced timelines, mitigate development risks, and ensure companies have submission-ready CMC package in-hand when they’re ready to apply for an IND.
Improving Timelines, Ensuring Quality, Controlling Cost with Lonza’s Ibex® Design program:
Lonza Biologics possesses a broad range of capabilities to support various therapeutic modalities, including mammalian, microbial, mRNAs, and antibody drug conjugates (ADCs). Its biologics development capabilities span from early development services supporting lead candidate selection such as humanization, non-GMP protein production, and developability testing, to cell line, process, analytical and formulation development, as well as GMP drug substance and drug product manufacturing for clinical and commercial molecules.
Within its global network of facilities, Lonza has supported the development of more than 565 large molecules in 2021; more than 515 of those molecules are in the preclinical and clinical phases of development, while 50 are commercial molecules. This expansive portfolio is supported by Lonza’s 35 years of experience in developing cell lines and supporting DNA-to-IND programs, with more than 800 cell lines moving from development to GMP manufacturing. Lonza’s GS system also has a robust history, with more than 60 commercial products on the market. Lonza has also supported more than 145 INDs and Investigational Medicinal Product Dossiers (IMPDs).
This track record has enabled Lonza to create and optimize a workflow with platform, processes, and analytics using a solid risk-based approach to track activities in parallel during the DNA-to-IND process, enabling it to reduce timelines while also minimizing risk. This approach, combined with single-use technology, enables flexible options for resupply, tech transfer, and scale-up within Lonza's network. In addition to drug substance, Lonza also possesses wide-ranging experience in drug product services, with drug product development and manufacturing capabilities spanning various modalities. Roughly two-thirds of the products Lonza has supported in the past have been antibodies, but it also possesses extensive experience with non-antibodies, such as bispecific antibodies, antibody fragments, recombinant proteins, and fusion proteins. Lonza’s Drug Product Services has liquid and lyophilization capabilities and experience with different concentration ranges, from low concentration to greater than hundred milligrams per milliliter.
Ibex® Design 2.0 guarantees customers tox drug substance delivery in 5 months and drug product in 11 months*. The Ibex® Design offering includes a holistic package to support an IND, including stability studies, materials storage, and end-to-end supply chain management. Because it is fixed price, Lonza’s Ibex® Design program affords customers greater control over their budgets, minimizing the need for potential rework by integrating drug substance and drug product at one site under one quality system.
The overarching timelines that Ibex® Design adheres to are well codified – a research cell bank or cell development is completed within two and a half months of the project’s launch, with formulation and process development ongoing in parallel to this activity. Clinical toxicology non-GMP drug substance is also provided at the 200-liter scale at five months, and GMP drug product released at 11 months. Ibex® Design also provides customers a minimum 1.5 kilograms of drug substance, with drug substance produced at the 1,000-liter scale.
Integrative, Innovative Technologies for Accelerated Biologics Development
A core element of the Ibex® Design workflow is new technologies geared toward reducing the time necessary for certain unit operations and improving the overall quality and robustness of processes. Lonza works to balance its existing platform technologies with advanced, state-of-the-art elements to optimize performance. The expression system used in its cell line development workflow has been recently upgraded to include GS piggyBac®, a platform that facilitates more controlled DNA insertion for a product of interest within the host’s genome. This capability is optimal for monoclonal antibodies, and is also well-suited to more complex proteins.
The major advantages of this upgrade are twofold. The first is a much faster recovery rate following transfection: on average, a previous version of GS Exceed® alone required 10 days or more for a cell to recover sufficiently to proceed to the next step. With GS piggyBac®, this recovery has been reduced to a few days. The second advantage has been higher product concentrations at the pool stage for fed-batch cultures, resulting in a higher probability of generating more productive cell lines.
The next step in the Ibex® Design process is single cell cloning, as well as screening and selecting the best clone to advance toward manufacturing. This is performed using the Berkeley Lights Beacon technology, a fully integrated, automated platform that utilizes opto-fluidic positioning to move individual cells. Thousands of cells are isolated and subsequently monitored for growth and productivity; this is typically performed in a miniature bioreactor system, wherein operators test performance and productivity using the manufacturing fed-batch protocol.
Lonza has also launched the latest version of its direct-to-platform process, GSv9™, designed to support speed-to-clinic with chemically designed and animal component-free media and feeds. This process, which scales seamlessly and conforms to GMP standards, results in high product quality, with low levels of aggregates or fragments, and appropriate glycosylation patterns.
Increasing Speed While Decreasing Risk
Ibex® Design 2.0 new, accelerated workflow innovates to improve speed without increasing risk, ensuring that timelines and quality are maintained throughout. By developing the process and cell line in parallel, Lonza can commence subsequent production steps once the research cell bank is available, saving considerable time. This approach can cause concern for companies that may question whether the early pool material is truly representative of the material generated later; Lonza has generated considerable data to validate this approach, as seen in the below graphs, where the profiles are equivalent regardless of whether the material was generated from the pool or a clone.
Another strength of Ibex® Design’s integrated development approach is in its scalability. The toxicology material is produced in a 200-liter bioreactor system that is a scale-down model of the bioreactor used at GMP manufacturing scale. Once a program progresses beyond early clinical development stages, Lonza is able to offer optimal and flexible manufacturing capacity through its extended manufacturing network.
Ultimately, pursuing parallel cell line and drug substance process development is one of the key strategies biopharmaceutical companies can employ to save time without increased development risks. Lonza’s Ibex® Design workflow relies on state-of-the-art process platforms, which ensure straightforward scale-up to cGMP manufacturing, as well as new, innovative technologies and workflows that further reduce the development time and improve the overall productivity. This secure, validated approach helps companies achieve faster timelines with the expected level of quality assurance.
*For antibodies. From DNA transfection. Subject to terms and conditions.