Virus Exposes Weak Links In The Biopharma Supply Chain

By Matthew Pillar, Editor, Bioprocess Online
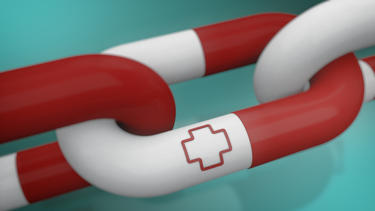
Earlier in March, my colleague Louis Garguilo wrote an eye-opening column that discussed the pharma supply chain’s dependence on commercial airliners to move pharmaceutical material, both raw and finished, around the globe. Much of that material originates in China.
On the heels of that column, the life sciences investment firm SVB Leerink hosted a conference call that exposed just how big a problem that presents to US biopharma innovators. Correcting the problem won’t be a quick fix. And as the epicenter of the virus shifts and jukes its way across the globe, mitigating the consequences to your supply chain might look akin to a high-stakes game of whack-a-mole. You’ll tamp down a potential disruption with one hand while constantly scanning the landscape for the next.
While the SVB Leerink call covered impacts to pharma on the whole, these are the key takeaways for biopharma:
- While exposure to China is small for finished dosage forms (8 percent) and active pharmaceutical ingredients (14 percent), the exposure on key starting materials is significantly greater (90 percent).
These percentages are more skewed towards US, EU, and Australia for biopharma innovators, which is only good news if those countries quickly turn the corner in their own coronavirus containment and mitigation efforts. While biopharma innovators’ proclivity toward “in-sourcing” gives them a bit more visibility and control over their supply chains, that advantage only lasts as long as their suppliers remain stable. It’s difficult, however, to measure the impact on specific innovators given that the FDA has not disclosed any of the information in the Closed portion of individual products’ drug master files.
Another consideration is that biopharmas with late life cycle products are more likely to outsource, putting them at higher risk of losing supply chain visibility and control.
- Companies generally have 6 months inventory of finished goods and 6 months of API on hand, and an impact of COVID-19 beyond the April/ May timeframe would see impact come through 6-9 months down the line.
API companies are exploring alternative sources as part of their mitigation plans, but adding a secondary source depends heavily on the complexity of the API. Bringing a new supplier online is a time- and resource-intensive endeavor, due in no small part to the analytical testing and logistical considerations involved. And, yet again, vetting the stability of a new supplier is difficult as the virus’ spread and trajectory unfolds.
- While manufacturing in China may be starting to come back online, the disruption will likely shift to other geographic regions, resulting in the inevitability of drug shortages on certain products. Stakeholders on the call surmised that the disruption is likely to be seen in 4Q20 or 1Q21 time frame and potentially earlier in some cases.
Exacerbating the situation, integrated delivery networks have started to stockpile hospital injectables, having learned to do so from prior experience with disruptive events (e.g., Hurricane Maria), and some APIs originally allocated for the US are being shipped outside of the US to countries like Dubai and China, which are anticipating a shortage of certain products and willing to pay a higher price. It’s anticipated that this kind of profit “optimization” will continue, further muddling shifts in the geographic markets in which APIs are available.
- While the COVID-19 pandemic may prompt efforts to secure the US pharma supply chain domestically, there remain environmental and cost challenges to any potential implementation.
As recently as March 11, the White House noted it is working on an executive order to require purchasing of pharmaceuticals and medical equipment from American-made companies. That’s a years-long proposition, and as discussed on the call, it raises fundamental questions around the EPA- and OSHA- implications on the manufacturing of key starting materials. It’s also assumed that US-made product and API costs would increase.
While the SVB Leerink call focused on disruption stemming from China, the spread of this particular pandemic makes it clear that there are many facets to the geographic diversification of biopharmaceutical materials strategy. There is no longer a “ground zero.” The world is the virus’ stage.