Top 5 Considerations When Making Decisions For A More Robust Harvest
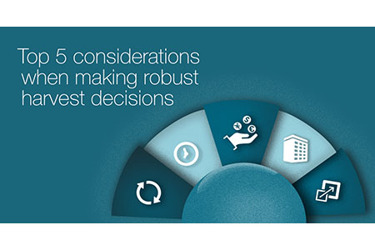
Once a drug developer has identified a viable molecule, one of the more complex decisions that must be made is defining the process used to produce, harvest, and purify said molecule. There is a need for innovative single-use technology to support the monoclonal antibody (mAb), recombinant protein, bioengineered vaccine, gene therapy, and cell therapeutic segments, accommodating the market growth forecast in the coming years. With a growing need for optimization of processes requiring high cell densities and more efficient workflow steps to alleviate bioproduction bottlenecks, customers are seeking robust innovations in the harvest step to address unmet needs they are facing. More specifically, those needs often revolve around finding ways to drive down operational costs while still managing to develop a process that is sustainable.
For secreted biologics produced in a batch process, the harvest process requires the full bioreactor volume until all the drug products have passed through the harvest equipment and are ready for the downstream purification step. Historically, many facilities used stainless steel centrifuges, which require steamin- place (SIP) systems to be run between batches to assure regulatory compliance and sterility. In contrast, depth filtration is a much more flexible technology in relation to scalability and uses a series of filtration steps to remove waste from wet biomass. Many modern harvest steps have become more abbreviated and result in less exposure. This allows for further facility optimization of cleanroom space and other efficiencies. The ratios of consumable to hardware costs vary between these two most common harvesting methods. Selecting one type of technology and process over another requires an assessment of facility operations, cleanroom space, labor expenditure, ongoing cost support, and upfront capital expenditure investment.
Read how considering the perspective of sustainability, time, cost, space, and scale will allow companies to thoroughly evaluate the key harvest considerations that contribute to cost and operational efficiency savings.
Get unlimited access to:
Enter your credentials below to log in. Not yet a member of Bioprocess Online? Subscribe today.