The ADC Market Is Ripening For Disruption

By Matthew Pillar, Editor, Bioprocess Online
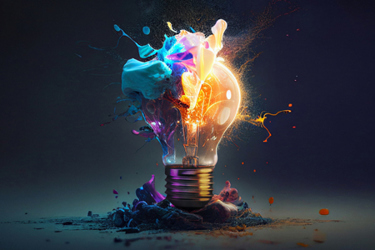
A word of warning to upstart ADC (antibody-drug conjugate) developers who think they’ll be able to handily outsource the manufacturing component of their early-stage ADC therapeutic candidates. The ADC contract manufacturing market is poised for growth, but the shopping is tough right now. As he noted in this column discussing the material handling risks of the HPCs in ADCs, Herman Bozenhardt says multi-use outsourced manufacturing facilities are likely going to be off the table. Dedicated contract facilities are currently few-and-far between, and one-stop mAb, payload, linker, and fill/finish ADC shops are countable on one hand. If you don’t plan to build your own facility, or hand off to big bio before the manufacturing gets hot and heavy, you’d better be making plans.
How can that possibly be, you might ask? ADC development is on fire right now. The technology has come so far, and the therapeutic promise is so great. There are tons of CDMOs in the ADC space! Just look at the list of players Google’s generative AI tool spits out when queried for ADC contract manufacturers:
- AbbVie Contract Manufacturing
- Abzena
- CARBOGEN AMCIS
- Catalent Pharma Solutions
- Cerbios-Pharma
- Creative Biolabs
- Formosa Laboratories
- Goodwin Biotechnology
- Lonza
- MabPlex Minakem
- Recipharm AB
- Sai Life Sciences Limited
- IDT Biologika GmbH
- MilliporeSigma
- Sartorius
- Sterling Pharma Solutions
- WuXi XDC
What’s more, if industry observers like Roots Analysis are right, this list is poised for big growth. The research and consulting firm currently estimates the global ADC contract manufacturing market at $1.79 billion, and their forecast shows it ballooning to nearly $7 billion by 2035.
Take that, Bozenhardt. Pretty tough to refute those numbers.
Eh, not so fast. As is usually the case with market analyses and forecasts, the devil is in the details. And the details reveal that Bozenhardt isn’t wrong.
Outsourced ADC development and manufacturing is a wildly fragmented exercise. In fact, in preparation for a recent Bioprocess Online Live event that touched on the topic, SOTIO head of CMC Meinhard Hasslacher, Ph.D. illustrated those realities when he reflected on heading up CMC for ADCs versus playing the role for mAb development, for instance. With ADCs, there’s LOTS more responsibility for orchestrating the flow of drug candidates from one outsourcing partner to the next. His job, he says, has become as much about managing manufacturing logistics and multiple contract partner relationships as it has about managing chemistry and controls.
The Roots Analysis study backs up Dr. Hasslacher’s reality. It identifies four major segments in outsourced ADC manufacturing:
- Manufacturers of the antibody
- Manufacturers of the high-potency active pharmaceutical ingredient (HPAPI)/cytotoxic payload
- Developers of the linker/conjugation technology
- Fill–finish suppliers of the final drug product
The largest share of the $1.79 billion-and-growing ADC contract manufacturing market identified by Roots Analysis, at 40%, is represented by antibody manufacturers. The second largest segment, at 30%, are the contract conjugation/linker developers.
The folks handling the dangerous HPAPIs/cytotoxic payloads are much fewer and farther between. They represent just 20% of the market, and the fill/finishers receiving these dangerous drugs for commercial preparation are fewer still, representing just 10% of the market. These are most certainly, (or certainly should be) dedicated facilities, as the final filled product remains a risk. It’s cytotoxic, residuals on the exterior of the vial are a real concern, and the equipment used to fill and finish it – lyo condensers, piping, and more—are subject to contamination. Single-use technology suppliers, take note that this opportunity is written on the wall
Specific to cytotoxic payload manufacturers, this skew in numbers can be attributed, at least partially, to the low volume of HPAPIs required in the ADC manufacturing process. But the handling of threatening materials, and the risks those materials pose to both personnel and adjacent drug development and manufacturing operations, have a tendency to quickly thin the crowd of would-be manufacturing partners. What you’re doing in the lab will quite literally take a village to replicate at scale.
Market Impact Of ADC HPAPIs
Bozenhardt and I recently discussed the market implications of a large-and-growing field of pre- and early-clinical ADC developers having access to a shallow pool of manufacturing contractors willing to handle their payloads.
The Roots Analysis forecast answers part of the question we mulled. Where there is therapeutic demand, the industry will build capacity. The glut of drug manufacturing facility construction spurred by COVID and, more recently, the GLP agonist boom demonstrate the simplicity of supply-and-demand in biopharma.
That said, Bozenhardt suggests that as more outsourced ADC capacity comes online, there’s a high probability that much of it will be coming online outside of the U.S. and Europe.
“As the volume of demand for development and manufacturing of HPAPI therapeutics becomes heavier and riskier, outsourcers will likely move those projects to places like China,” Bozenhardt suggests. “There, organizations like FDA, EMA, OSHA, NIOSH and others that would be very interested in what they’re doing with these highly potent compounds don’t exist, or don’t apply the same stringency to safety standards.”
Despite the risks to IP, technology, and market entry control, the prospect of U.S. drug developers and CDMOs staking their manufacturing claims in China isn’t new. But, the additional risks that decision takes on in the context of the U.S. BIOSECURE Act and the sentiment driving it certainly are.
Should You Consider In-Sourcing Your ADCs?
Of course, many of the ADC startups crowding the space don’t have any intention to manufacture anything. They’re playing toward an acquisition by a company that’s heeled enough to manufacture their innovation in its own dedicated ADC facility, or muscle the project into one of the few CDMOs/CMOs willing to take it. But among those upstart companies that do intend to create drug product—and among larger biopharmas that haven’t yet progressed an ADC candidate—Bozenhardt anticipates a spike of in-house manufacturing buildouts. “Some of these folks are going to have to design and build their own facilities, and they will have to manage those facilities themselves, and if they want quality qualification, they’re going to have to do it where they have support that will look out for their interests,” he says.
As we discussed in this previous column, that’s a much taller task than building and qualifying an antibody manufacturing facility.
‘Some of the bigger and later-stage players will go ahead and they'll buy or build a dedicated facility, or they'll take a warehouse, and they'll stick a couple of G-CON pods in there, and that's how they will move forward in the market,” Bozenhardt surmises. “But the smaller ones aren’t likely to do that, They will play a bit of a game with the three or four leaders that eventually come out of this ADC race.” As that game plays out, he projects that the small ADC biotechs struggling to find the right CDMO, or struggling to find the money to progress their clinical programs, will entertain offers from big bio, and we’ll see some significant consolidation activity taking place in the market.
“With a few more candidates getting to phase 3, a couple of products hitting the market, and some big bio money pumping in, we’ll see this ADC market begin to change,” says Bozenhardt. “But because of the unique facilities requirements for handling HPAPIs, it’s not going to happen as easily as you might think.” Read more about those requirements, and where Bozenhardt sees them being ignored, at the link above.