More Case Studies: Managing Change In Vaccine Production
By Eric Doerr, Manufacturing Sciences and Analytical Technology, Sanofi, Toronto
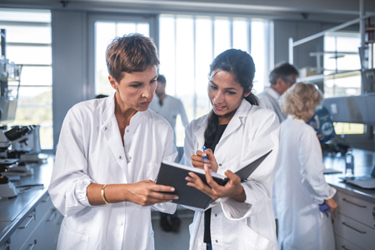
Managing process and equipment changes for vaccine production processes requires, above all, transparent and meaningful communication between all stakeholders.
As described in the first part of the series, a small but important process change can quickly become unwieldy and complicated when it involves many departments and regulatory agencies, especially when the validation stage overlooks key process bottlenecks.
In this second part of the series, four more case studies covering several scenarios will be discussed:
- unplanned supplier-required equipment upgrades,
- data alignment between vendors and their customers,
- scaling ancillary processes to support continuous manufacturing, and
- retrofitting legacy facilities to execute improved processes.
Replacing Unsupported Equipment
In this case study, a manufacturing skid related to the depth filtration of a mixture of several midstream intermediate products required new equipment validation after the manufacturer informed production management that the current equipment in use was obsolete.
The depth filtration step is responsible for early-stage purification of several products of interest against a host of in-process biological and/or chemical impurities; therefore, the company was unable to change it without significant regulatory filing updates. Further, while the replacement of the skid was originally assessed to be minor in scope, it was clearly observed during the performance qualification that the operational conditions differed, resulting in unexpected performance differences that needed alignment/validation support.
Two important tools that put the equipment performance qualification back on track included creating a development/validation library and securing internal/external laboratory testing sources.
The first tool indexed the product and process knowledge surrounding the depth filtration itself, thereby providing insight as to how the step was developed, what parameters most influenced operation, and the correlations of the development/parameters to refine the new way of working with a new depth filtration skid. The second tool secured time-sensitive testing through redundant lab groups. This allowed the validation team to act quickly and meet the study objectives without putting the submission to the appropriate stakeholders/health authorities at risk.
By the end of the new equipment qualification, the depth filtration skid was fully qualified and validated following the establishment of a new process baseline for the affected products. Procedures related to the preparation of the depth filters, along with flow/pressure management during operation, were updated to yield the same quality metrics without impact on product recovery.
Dealing With Insufficient Vendor Data
Another case study involved one media support group responsible for several buffers, media, and solutions that pass through a terminal filtration step. The group did not have sufficient validation data to support product-specific bubble point testing following an extensive investigation related to manufacturing practices within the area. The risks identified included an insufficient data set from an external vendor that challenged the accuracy of the on-site bubble point testing values, the challenge of adhering to said limits and how these limits were used/interpreted within the manufacturing area, and an on-site knowledge gap regarding interpretation of filter validation requirements across different departments.
As a result, filter validation testing was performed internally for simple buffers and solutions using resources from the manufacturing area. It was also performed externally, with the support of industry experts, for complex media and solutions to secure accurate and consistent results.
Given the convolution of managing internal and external stakeholders throughout the filter validation activities, the team held standard meetings with set agendas to discuss study status, results, risks, and mitigating actions. This allowed the team to speak with a single voice and ensure all other members were progressing with the ancillary tasks to support the core team. Another tool that secured the success of the validation was the selection of the appropriate statistical analysis/acceptance criteria that provide an accurate picture of the manufacturing process and, most importantly, that meet regulatory requirements.
By the end of the exercise, most of the on-site filter validation work had been executed and troubleshooted, with the remainder finalized by the external validation team. It was concluded by identifying key internal stakeholders familiar with the regulatory requirements related to filter validation practices. A close working partnership and oversight with external filter validation groups required complete visibility of the logistics/supply chain prior to execution. This was made possible by the use of a shared vocabulary, understood by all stakeholders, for the purposes of the study.
Updating Process To Meet Increased Demand
The next case study involved a different on-site media support group in charge of manufacturing a widely used industrial cleaning solution that had a short in-use expiration date. This narrow useful life of the solution was seen as a risk to other processes and procedures using said solution. Challenges included duplication of work with the repeated manufacturing of the same cleaning solution within a work week and an increased workload for a media group responsible for providing media to more than four manufacturing areas. Moreover, the original validation supporting the cleaning solution manufacturing was misaligned with other media manufacturing areas on-site and across industry.
Based on the nature of the process change to address, a technical assessment was generated to unify the validated state of this cleaning solution across all manufacturing areas. This initial step was required to delineate the quality metrics, process definitions, and limits toward which all manufacturing areas would converge. Tools that were used to make this technical assessment effective included leveraging the internal network available to support the study design and to establish firm study boundaries on scope control. The first tool leveraged expertise across the company and industrial network to assure the validation status, consider previous studies and established baselines, and ensure the assessment purposes would be met. The second tool consisted of using project management features such as Gantt charts and RACI tables to clearly define what needed to be done and by whom, thus streamlining and securing the assessment.
Anecdotally, simple problems do not always positively correlate with simple solutions when working within a routine manufacturing environment. Using available manufacturing data and sound technical knowledge and expertise and, most importantly, drawing reasonable connections within a validated design space are critical for any improvement to GMP activities. This alignment exercise significantly reduced overprocessing of a common cleaning agent while increasing sustainability initiatives across the site.
Retrofitting Facilities For Improved Processes
The final case study for securing stakeholder acceptance was an investigation into upstream manufacturing. The introduction of a new upstream process in a legacy facility faced challenges with retrofitting updated equipment, procedures, and data analytics compared to the obsolete one. More precisely, after its implementation into routine manufacturing, a newly developed process was unable to grow a microbial culture to meet specific harvest criteria (i.e., culture was too slow to grow and/or unable to produce product of interest). This inability to produce harvestable product introduced an unknown end-to-end process risk with batches not achieving the appropriate titer that could not proceed to the associated downstream purification step. This represented a potential stock-out in the market.
An extensive investigation was launched to re-secure production, with two tools to ensure all stakeholders were united across the investigation timeline/deliverables. First, using effective “shakedown” stratification to assist in the root cause analysis aspect of the manufacturing investigation enabled the team to significantly parse through each functional component, identify its relevance as part of the investigation scope, and provide further risk/mitigation actions with investigation closure. Second, using effective control plans to flag the critical and/or key parameters and/or attributes of the process was instrumental in both the corrective actions taken after root cause identification and the preventive actions with routine manufacturing monitoring to prevent recurrence in its entirety.
Ultimately, the root cause related to the slow/low growth was identified, and the process was revalidated with consideration of the equipment design’s influence on the fermentation process. The revalidation secured the current market and removed the risk of a stock-out in the global vaccine market.
Conclusions
The toolkit outlined here can be used at any stage of the product/process life cycle. End-to-end integration of effective techniques safeguards stakeholders’ commitment to the product. Pursuing continuous process improvement and implementation ensures security and success across any product pipeline.
About The Author:
Eric Doerr is a senior project lead for upstream and downstream processing areas at Sanofi where his work supports and improves global vaccine supply chains. He earned his bachelor’s and master’s degrees in biochemical engineering science from the University of Western Ontario.