Low Risk Frozen Distribution Of Single-Use Bags For Bioprocessing
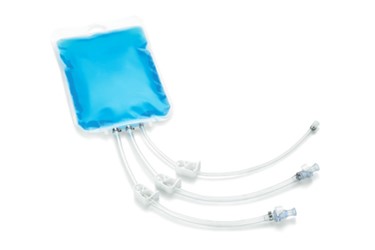
As biopharmaceutical therapy development and manufacture proliferates on scale-up in biosimilars and scale out in emerging cell and gene therapies, the successful distribution between process sites becomes vital for the supply chain. These steps are often decentralized for added manufacturing flexibility since final fill and finish processes are not bound by time-dependent active pharmaceutical ingredient (API) product factors and can therefore be utilized at a higher rate than API production processes. As the global clinical pipeline expands with more complex and temperature-sensitive products, the distribution of high value API’s between development sites, clinical sites, and to drug manufacturers for further processing will become a more relied upon paradigm. This is the case in the ongoing race to develop treatments for COVID-19, which requires a temperature-controlled distribution network that can quickly scale-up to meet huge demands. Cold chain dependent pharmaceuticals are projected to grow twice as fast as the industry overall with the 2022 expectation that 30 of the 50 top global biopharma products will require cold chain handling.1 As cold chain grows, effectively managing and mitigating its associated risks will be critical.
Cold chain consists of the freezing of heat liable APIs to below subzero temperatures for storage and transport followed by thawing for their subsequent manufacturing and production. The current implementation of single-use bag technology is reducing operating costs and mitigating the contamination risk of traditional stainless steel freezing tanks and bottles through batch flexibility, lower storage density, and controlled freezing all in a sterile closed system. However, under frozen temperature these single-use components are brittle and prone to failure that can lead to product loss and contamination, especially during transportation. In addition, transport can be a nebulous step where it is the only part of the production process that is outside of the manufacturer’s process control. Even within the cold chain end-to-end process (Figure 1) the frozen distribution of product is where significant failure can occur from various unknown mechanical and thermal shocks experienced along its route. Mechanical damage typically results in 3 – 5% product loss from bag breakage in frozen bulk drug cold chain handling while most pharma end users see temperature excursions in their shipments. 43% of those end users see excursions that exceed four degrees, which is enough to harm their product.2 To further quantify this impact, the industry sees a $35 billion loss annually from failures in temperature-controlled logistics.2 It is vital then to have a single-use product packaging system that functions under these conditions but often, these systems are not appropriately qualified to avoid failure or maintain temperature because their challenging distribution environments are not fully understood. Fortunately, the risks of single-use bags in frozen shipping can be mitigated by following the approach of:
- employing sensors for monitoring critical shipment parameters
- utilizing more suitable low-temperature materials and packaging
- qualifying and evaluating through simulated standards and testing in real-world transit lanes
Implementing these guidelines increases visibility in your distribution lane, incorporates robust materials, and qualifies them against relevant metrics to ensure consistent product quality in cold chain.
This paper will discuss the results of applying this approach to a frozen shipping study of single-use fluoropolymer bags.
Get unlimited access to:
Enter your credentials below to log in. Not yet a member of Bioprocess Online? Subscribe today.