Reduce Product Loss In Biopharma To Save Costs
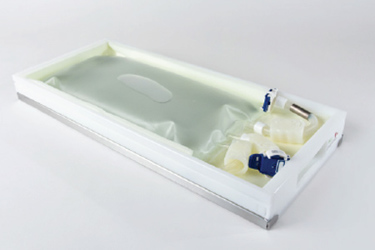
The customer, a global biotechnology company with a total turnover of > 5 billion USD, produces different drug substances (BDS) of highly valuables mABs in batch sizes from 10l to 700l for clinical phases up to commercialized products. The BDS is frozen < -85°C (-121°F) and shipped within Europe or transatlantic for max. 200 hours with dry ice and stored. At the fill & finish site, the BDS is thawed for producing the drug product.
The biotech company planned to rely on single-use bioprocess containers as preferred primary packaging for BDS bulk filling, freezing, storing and shipping. This was due to various advantages of single-use bags like filling in a closed system, higher volumes, scalability and high storage density.
But the biggest challenge of single use bags was the high loss rate of 0,5% to 5% due to their sensitivity at sub-zero temperatures. The product loss rate depends on the bag used, the clam shell of the product, the process and the shipper/shipping route. Therefore, the goal was to reduce the current product loss below 0.5%.
Continue reading to learn how they set up a cold chain process and implemented robust technologies around the brittle single use bag and to consequentially reduce product loss.
Get unlimited access to:
Enter your credentials below to log in. Not yet a member of Bioprocess Online? Subscribe today.