Forget About Isolators: Switching From Manual Vial To Automated Bag Filling
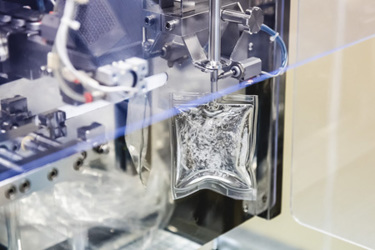
More than half of pharmaceutical manufacturers still rely on manual filling for drug substances — a process that remains highly susceptible to human error, which accounts for approximately 80% of process deviations in pharmaceutical production. Manual filling is typically carried out in isolators, laminar flow hoods, or biosafety cabinets, where vials are individually filled by hand.
One mid-sized European biotechnology company faced these limitations firsthand while manually filling intermediate products for viral vectors as part of its fill-and-finish process. Using an isolator-based filling line, the company encountered multiple challenges: a heightened risk of contamination due to open handling, difficulty achieving the precision needed for small fill volumes (ranging from under 100 mL down to 3 mL), and a labor-intensive process involving the handling of more than 1,000 single-use bags per batch. Additionally, the lack of standardization in the aliquoting process led to inconsistent fill volumes, failing to meet GMP compliance requirements.
As batch sizes continued to grow and these inefficiencies became more pronounced, the company recognized the need to shift from vials to single-use bags as its primary packaging format. FInd out what happened next by accessing the full case study below.
Get unlimited access to:
Enter your credentials below to log in. Not yet a member of Bioprocess Online? Subscribe today.