Are Bioprocess Equipment Standards A One-Sided Conversation?

By Matthew Pillar, Editor, Bioprocess Online
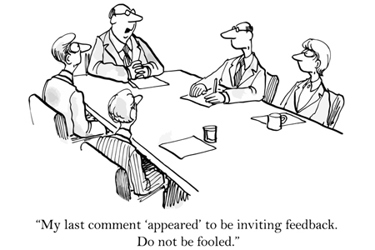
Aspen Surveys asked end-users of single-use supplies in the biopharmaceutical industry, “which of these is the greater challenge in further growing industry acceptance of single-use technology?”
Respondents could choose just one from the following options:
- Concerns about sustainability
- Price
- Lack of standardization
Todd Kapp, CEO at Wautoma Biotech LLC, presented this statistic (and many more) on behalf of Aspen Alert publisher and executive editor Larry West at the BPSA (Bio Process Systems Alliance) International Single-Use Summit this month in Washington, D.C.
The top response, far-and-away, was lack of standardization, chosen by half of industry respondents. Sustainability concerns trailed at 38%. Price registered a nearly negligible 12%.
The Push-Pull Dynamic Of Standards & Interoperability
The supplier storyline at the BPSA Summit isn’t unfamiliar. The major vendors of single-use supplies were there. Sometimes they compete with one another, but often, they find themselves cooperating on biopharmaceutical manufacturing client projects. The buzzword “coopetition” is bandied about often in these circles. The need for that cooperation is rooted in interoperability, not to be confused with standardization:
- Interoperability: The ability of a system to work with or use the parts or equipment of another system.
- Standardization: Bringing into conformity with a standard, especially in order to assure consistency and regularity.
Manufacturing environments are rarely, if ever, single-sourced, the result of unique manufacturing requirements, mergers and acquisitions, hybrid fixed/single-use facilities, legacy development and manufacturing approaches that would require regulatory pushups to change, or any combination of all of the above.
To the supplier community, that reality demands several things—interoperability, customization, and differentiation among them. While those things add complexity to both deals and implementations, they’re welcome. Complexity and interoperability come at a cost to end users, and with that cost comes healthy profits for suppliers. Plug-and-play is, generally speaking, not good for margins. This is not to disparage the supplier community, because importantly, standardization isn’t good for differentiation either. Differentiation benefits both suppliers and end users of bioprocessing equipment. In an industry marked by dozens or more companies chasing the same targets, in many cases with very similar molecules, even nuanced differences in manufacturing processes and equipment (protein design notwithstanding) create the efficiencies that enable differentiation.
Is Single-Use Interoperability A Failure Point?
I shared some of these observations with a colleague of mine recently. She’s in business development and spends much of her time talking to market leaders from the single-use supply scene. I mentioned that another presenter at the BPSA Summit, BioPlan Associates’ Eric Langer, showed data demonstrating an increase in single-use failure rates in recent years. To be fair, more research must be done to accurately determine whether that increase is corollary to the increase in single-use technology adoption, or whether the ratio of implementations-to-failures truly is worsening. Regardless, my business development friend said that when faced with the single-use failure objection, her counterparts from the supplier community sing a common refrain. The stuff breaks because it’s improperly assembled, they say. That’s anecdotal, but I wonder if there’s truth to the notion.
For some insight, I turned to the BioPlan Report and Survey of Biopharmaceutical Manufacturing Capacity and Production, 21st edition. Just last year, the survey began reporting on the frequency of SUS failures by asking respondents simply, When was the last failure of single-use devices and equipment at your facility? Here’s a snapshot of responses:
- Single-use Container Bags: 23.9% indicated failure(s) within the past 6 months. 19.6 % indicated failure(s) more than 2 years ago.
- Single-use Freeze Bags: 14.9% indicated failure(s) within the past 6 months. 28.6% indicated failure(s) more than 2 years ago.
- Single-use Valves: 17.1% indicated failure(s) within the past 6 months. 32.4% indicated failure(s) more than 2 years ago.
- Single-use Tubing: 19.3% indicated failure(s) within the past 6 months. 26.5% indicated failure(s) more than two years ago
- Single-use Connectors: 17.9% indicated failure(s) within the past 6 months. 22.9%indicated failure(s) ore than 32 years ago.
- Single-use Bioreactors: 17.1% indicated failure(s) within the past 6 months. 24.4% indicated failures more than 2 years ago.
The highest rates of failure over the 6 months preceding the survey were in container bags, tubing, connectors, and valves. Valves show the highest level of failure over the 2-year period, unsurprising given their mechanical nature, followed by freeze bags, unsurprising given their exposure to temperature extremes. But tubing and connectors? Those, along with valves, are likely the most susceptible to interoperability issues. The BioPlan report authors concede that “this trend suggests that failure might be dependent on other factors within the facilities such as maintenance or production conditions,” which lends some credence to those anecdotal supplier claims that end-users aren’t assembling (or maintaining) them correctly.
What are the implications of these failures? According to the survey, equipment failure results in the failure of 3.5% of batches, on average, at clinical scale and 2.6% of batches at commercial scale. It’s a small percentage, but each of those decimal points represents a lot of time, materials, money, and risk.
BPSA Works Ardently On Interoperability And Standards
As noted in this recounting of Paul Priebe’s contribution to the Bioprocess Online Live event Single-Use Technologies For Bioprocessing: An Essential Update, BPSA contributes mightily to the interoperability discourse and development of standards – in terms of both the “plumbing” and particulates in the materials said plumbing facilitates. Priebe, an independent consultant with big industry experience, Cytiva’s Jeff Carter, Ph.D., who also chairs the ASTM (American Society for Testing and Materials) E55.07 Single-Use Standardization Working Group, MilliporeSigma’s Monica Cardona, and Sartorius’ Klaus Wormuth, Ph.D. are just a handful of BPSA-associated names leading the charge. The vendor/supplier space is well-represented here. But, sponsor companies, biopharmaceutical and contract manufacturers, and other forms of end users? Not so much, save for a few folks like Dr. Mark Petrich, VP at Krystal Biotech and chairman at BPSA.
End-User Engagement Required
During every session I sat in while at the Summit, I found myself thinking, this content would be quite valuable to a biopharmaceutical manufacturing exec who’s charged with setting their company’s single-use course. I know the BPSA would welcome more industry/sponsor participation. The top brass there has told me as much, and BPSA offers very reasonable end-user membership rates. I think it’s time industry takes the Alliance up on its offer. More end user perspectives would benefit the whole ecosystem, even if it meant exacting a little more “push” on the supplier community’s “pull.”
Finally, as Priebe so succinctly stated during the aforementioned panel discussion (link above), “If you ever find yourself saying, they ought to write a standard, go in the bathroom, look in the mirror, and say, they is you. If you want a standard, then show up and participate, because it doesn't come from somewhere else. It only comes from the participants in the industry.”