A Strategic Partnership Delivers Innovation, Efficiency In Biotechnology Manufacturing Training
By Koey Keylon, Cytovance Biologics
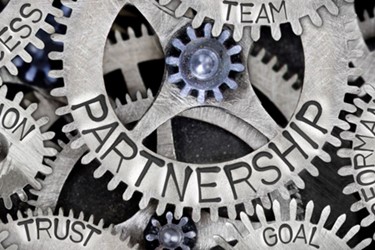
Biotechnology manufacturing training represents a large, often challenging investment. Developing and implementing an effective training curriculum takes months or years, diverting valuable time and resources away from other projects. Talent acquisition is difficult in many United States regions, with local candidates lacking biotechnology or life sciences manufacturing experience. Unfortunately, undertraining can lead to many operational issues, including production errors, record inconsistencies, and in worst cases, product contamination.
As an experienced contract development manufacturing organization (CDMO), Cytovance Biologics (Cytovance) creates innovative solutions that deliver value to our customers. Cytovance has a successful training methodology common in smaller biotech, relying heavily on procedural training combined with side-by-side training with subject matter expertise. As Cytovance experienced exponential growth, we realized we needed to streamline the training process to standardize across departments and to reduce the time to proficiency in our manufacturing areas. A cross-functional team set out to find the next step in evolving our training methodology.
This endeavor drove us to partner with the National Center for Therapeutics Manufacturing (NCTM) at Texas A&M to provide a customized training curriculum based on their workforce development curriculum/certification. Compared to estimates for developing the training program in-house, we achieved results in a fraction of the time (three months vs. an estimated 18 months) at a fraction of the cost (33 percent of the estimate).
Get unlimited access to:
Enter your credentials below to log in. Not yet a member of Bioprocess Online? Subscribe today.