VR/XR In Drug Manufacturing: No Longer Sci-Fi
By Erika L. Roberts, ELR Lab Services LLC
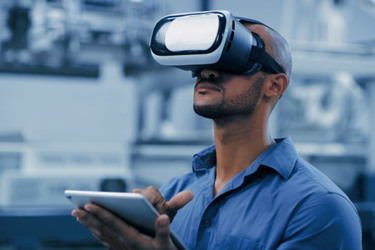
Remember those sci-fi movies where scientists manipulated 3D models of molecules with a wave of their hand? Well, it's not entirely fiction anymore. Virtual reality (VR) and extended reality (XR) are making their way into pharmaceutical manufacturing, promising to revolutionize how we design, train, and operate in this highly regulated sector.
Virtual reality immerses users in a completely simulated environment, while extended reality is an umbrella term encompassing VR, augmented reality (AR), and mixed reality (MR). AR overlays digital information onto the real world, and MR anchors digital objects in the real world, allowing interaction with both. These capabilities open up a world of possibilities for the pharmaceutical manufacturing facilities of the future.
VR/XR In Pharmaceutical Manufacturing: The Current Landscape
Even though this idea of using VR/XR to make drugs may sound like it is a far-away concept, there are already examples of how this technology is being used today:
- Design and Prototyping: VR allows engineers to walk through virtual replicas of manufacturing facilities, identifying design flaws and optimizing layouts before a single brick is laid. XR also can be used to visualize and manipulate 3D models of equipment and processes, streamlining the design and prototyping phases.
- Training and Upskilling: Training new employees in a GMP environment can be time-consuming and costly. VR offers a safe, immersive space for trainees to practice complex procedures and handle hazardous materials without real-world risks. AR can provide real-time guidance and instructions to workers on the shop floor, improving efficiency and reducing errors.
- Remote Collaboration and Support: XR enables real-time, remote collaboration. A technician wearing AR glasses can receive step-by-step guidance from a remote expert who sees the same field of view. This is particularly valuable for troubleshooting complex equipment issues or conducting remote audits.
- Maintenance and Repair: Picture this: an AR headset highlights the faulty component, overlays repair instructions, and even provides a virtual "ghost" of an expert's hands guiding the technician through the repair. Sounds like magic? It's the power of XR in maintenance and repair, reducing downtime and improving productivity.
The current and future applications of VR/XR in manufacturing are indeed remarkable. Below is a closer look at some key trends.
Digital Twins: The Heart Of Virtual Manufacturing
- Real-time Optimization: Digital twins, powered by real-time data from their physical counterparts, will enable manufacturers to continuously monitor, analyze, and optimize their operations. Think of it as having a virtual control room where you can run simulations, predict equipment failures, or adjust production schedules on the fly to respond to changing demands or unforeseen disruptions.
- Remote Collaboration and Training: Digital twins also can facilitate remote collaboration, allowing experts from different locations to interact with and troubleshoot the virtual model together. Imagine an engineer in Germany guiding a technician in the U.S. through a complex repair process using a shared digital twin. This could drastically reduce downtime and travel costs.
- Design and Prototyping: Digital twins also can revolutionize product design and prototyping. Engineers can experiment with different designs and configurations in the virtual world, test their performance under various conditions, and iterate rapidly before committing to physical prototypes. This can significantly accelerate time-to-market and reduce development costs.
AI Integration: The Brain Behind The Virtual World
- Predictive Maintenance: AI can analyze the vast amounts of data generated by XR simulations and digital twins to identify patterns and predict potential equipment failures before they occur. This allows for proactive maintenance, minimizing downtime and optimizing asset utilization.
- Process Optimization: AI algorithms can analyze production data and XR simulations to identify bottlenecks, inefficiencies, and opportunities for improvement. This can lead to significant gains in productivity, quality, and cost savings.
- Intelligent Virtual Assistants: AI-powered virtual assistants can provide real-time guidance and support to workers on the shop floor, offering step-by-step instructions, answering questions, and even troubleshooting issues. This can enhance worker productivity, reduce errors, and accelerate training.
Haptic Feedback: The Touch Of Realism
- Enhanced Training and Skill Development: Haptic feedback can make virtual training experiences more immersive and realistic, allowing workers to feel the resistance of a virtual machine or the texture of a virtual material. This can accelerate learning, improve muscle memory, and boost confidence.
- Remote Collaboration with a Physical Touch: Haptic feedback could also enhance remote collaboration by allowing users in different locations to interact with the same virtual object and feel its physical properties. Imagine two engineers collaborating on the design of a new product, feeling the weight and texture of the virtual prototype as they manipulate it together.
- Accessibility and Inclusion: Haptic feedback could make XR experiences more accessible to people with visual impairments, providing a tactile way to interact with and understand the virtual world.
Wearable XR Devices: The Seamless Integration Of Virtual And Real
- Increased Comfort and Adoption: As XR devices become smaller, lighter, and more comfortable, they will be more widely adopted in manufacturing environments. Imagine smart glasses that seamlessly blend digital information with the real world, providing workers with real-time instructions, data overlays, and even virtual collaboration tools without obstructing their vision.
- Hands-Free Operation: XR devices that can be controlled with voice commands, gestures, or even eye movements will allow workers to interact with the virtual world without taking their hands off their tasks. This can improve productivity and safety, especially in environments where hands-free operation is critical.
- Ubiquitous Access to Information: With wearable XR devices, workers will have instant access to the information they need, whenever and wherever they need it. This can empower them to make better decisions, solve problems more efficiently, and stay connected with their colleagues and supervisors.
Challenges And Considerations
While the transformative potential of VR/XR in pharmaceutical manufacturing is undeniable, a thorough risk assessment is essential to see successful implementation and avoid potential pitfalls.
Cost: The Price of Innovation
- Initial Investment: High-quality VR/XR hardware and software can represent a significant up-front investment, particularly for smaller companies with limited budgets. Additionally, the cost of developing custom VR/XR applications tailored to specific manufacturing processes can be substantial.
- Ongoing Costs: Maintenance, updates, and potential upgrades of VR/XR systems can incur ongoing costs. Companies need to factor in these expenses when evaluating the return on investment (ROI) for VR/XR adoption.
- Mitigating the Cost Risk: The good news is that as technology advances, the cost of VR/XR hardware and software is expected to decrease, making it more accessible to a wider range of companies. Companies also can explore leasing or subscription models to reduce up-front costs and spread expenses over time.
Validation and Compliance: The Regulatory Hurdle
- Stringent GMP Requirements: The pharmaceutical industry operates under strict good manufacturing practice (GMP) guidelines to ensure product quality and patient safety. Any new technology, including VR/XR, must comply with these regulations.
- Data Integrity and Traceability: VR/XR systems used in manufacturing processes must generate and store data that is accurate, complete, and traceable. Validation of these systems is crucial to ensure data integrity and compliance with GMP requirements.
- Mitigating the Compliance Risk: Companies should work closely with regulatory experts and technology vendors to ensure that VR/XR systems are designed and implemented in compliance with GMP guidelines. Thorough validation processes and documentation are essential to demonstrate compliance and ensure patient safety.
User Acceptance: The Human Factor
Some employees may be hesitant to embrace new technologies like VR/XR, particularly if they are unfamiliar with them or perceive them as complex or disruptive.
Companies should involve employees in the VR/XR adoption process from the beginning, gathering their feedback and addressing their concerns. Providing adequate training and support, highlighting the benefits of VR/XR for their work, and celebrating early successes can foster user acceptance and drive adoption. Change management initiatives are also essential to address concerns, build enthusiasm, and ensure a smooth transition.
Embracing The Virtual Frontier In Pharmaceutical Manufacturing
The pharmaceutical industry stands at a pivotal juncture, where the fusion of the physical and virtual realms is poised to redefine the very essence of drug development and production. VR/XR technologies, with their transformative capabilities, are set to revolutionize every facet of pharmaceutical manufacturing, ushering in an era of unprecedented efficiency, innovation, and patient centricity.
Imagine a world where scientists can visualize and manipulate complex molecular structures in three dimensions, accelerating drug discovery and design. Envision engineers collaborating seamlessly across continents, troubleshooting intricate equipment in real time using shared digital twins of manufacturing facilities. Picture technicians receiving immersive, hands-on training in virtual environments, mastering complex procedures without the risk of costly errors or contamination.
Beyond these compelling scenarios, VR/XR has the potential to optimize every stage of the pharmaceutical life cycle. From virtual walkthroughs of manufacturing facilities during regulatory inspections to interactive patient education modules that enhance treatment adherence, these technologies offer a powerful toolkit for improving quality, efficiency, and patient outcomes.
Of course, the path to widespread VR/XR adoption is not without its challenges. The initial investment in hardware and software, the complexities of regulatory compliance, and the need for comprehensive user training all demand careful consideration. However, the potential rewards are immense. As technology advances and costs decrease, the barriers to entry will diminish, making VR/XR accessible to a wider range of organizations.
We should not underestimate the human element in this technological revolution. By embracing VR/XR, we are not merely adopting new tools, we are fostering a culture of continuous learning, collaboration, and innovation within the pharmaceutical industry. We are empowering our workforce with the skills and knowledge to navigate an increasingly complex landscape, ensuring that we remain at the forefront of scientific discovery and patient care.
The virtual frontier beckons, promising a future where the impossible becomes possible. It is a future where drug development is accelerated, manufacturing processes are optimized, and patient experiences are transformed. It is a future where the pharmaceutical industry fulfills its ultimate mission: to deliver safe, effective, and accessible medicines to those in need.
It is important to seize this opportunity to shape this brighter future, where the fusion of technology and human ingenuity paves the way for a healthier, more connected world. The journey may be challenging, but the destination is clear: a pharmaceutical industry that is more innovative, efficient, and patient-centric than ever before.
About The Author
Erika L. Roberts, MFS, is principal consultant and owner of ELR Lab Services LLC. Having more than 15 years of experience working in many different areas of the pharmaceutical/biotech manufacturing quality environments, she has particular expertise in sterility testing, microbial identification training, HPLC analysis, cGMP training, analytical chemistry, and pharmaceutical regulations. Roberts obtained a master’s in forensic science in 2006 with an emphasis in document examination.