Using Virtual Reality To Enhance Aseptic Contamination Control
By Subrata Chakraborty, Ph.D., INOPHAR Consulting & Training and Ajay Pazhayattil, Ph.D., cGMPWorld
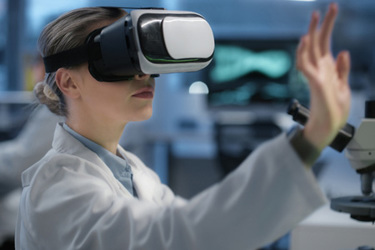
Aseptic processing remains one of the most critical and most scrutinized areas in pharmaceutical manufacturing. This is more so with the advent of new critical therapies involving high-value products relying on aseptic processing. Despite a host of regulatory guidance, technological advancements, and facility investments, concerns around contamination control persist. Regulatory bodies, including the U.S. FDA and the EU’s EMA, continue to report frequent findings linked to poor process design, inadequate operator practices, and a lack of robust contamination prevention strategies.
At the heart of many of these failures lies a common thread: human interaction with the process. Sterility breach and particulate contamination have been topping the list of reasons for drug product recalls from the U.S. market for decades. Such contaminations are often introduced inadvertently through flawed gowning, aseptic manipulations, or insufficient environmental controls, leading to compromised product quality and directly impacting patient safety. Often, regulators are concerned when a large number of failure investigations conclude human error as the root cause and training/retraining as the CAPA. Placing accountability on individuals without a rigorous root cause analysis is preventing the industry from implementing meaningful, sustainable corrective actions. In a practical sense, these issues typically stem from multiple layers of organizational weaknesses. In this article, we go into some of these issues and discuss how technologies such as virtual reality (VR), augmented reality (AR) or mixed reality (MR) can help alleviate some of the long-standing issues in this area.
How Does VR Address Facility Design Issues?
Even the most disciplined aseptic practices cannot fully compensate for a poorly designed facility. Inefficient layouts, inadequate segregation of clean and dirty workflows, poor airflow management, and equipment surfaces in critical zones that are difficult to access or clean all create inherent vulnerabilities. When the physical environment itself works against contamination control, it forces personnel into a constant battle with systemic weaknesses – a battle that is often lost over time.
Even today, we observe facilities where operators are required to fully enter Grade A environments to perform routine operations, significantly increasing the risk of contamination. In some cases, personnel must physically pass through flexible curtains, the only barrier separating Grade B from Grade A areas, thereby brushing and shedding contaminants. It is crucial to recognize that no operator, even after following the best hygiene and gowning practices, can be rendered sterile. Every intrusion into the Grade A environment elevates the risk of product contamination and threatens patient safety. Unfortunately, in many cases, facilities are designed without sufficient attention to these critical details, resulting in environments that are fundamentally unsuitable for robust aseptic manufacturing. The consequences of such oversights can be severe, yet they are often overlooked during the design and construction phases, only to manifest later in operational challenges and regulatory findings.
Contamination control starts at the design phase. VR offers a powerful solution to preempt and address facility design flaws and operational risks in aseptic manufacturing. By enabling full-scale virtual walkthroughs during the design phase, VR allows stakeholders to experience layouts, workflows, and interventions firsthand, identifying and correcting risks before design and construction. Operators can simulate aseptic operations and visualize how their actions can impact contamination control. Design flaws can be identified and corrected early, reducing costly changes later and ensuring a facility that supports contamination control.
How Does VR Address Aseptic Process Design Deficiencies?
Processes that require frequent human intervention inside classified areas or involve unnecessary complexity inherently increase the risk of contamination. Systems that lack sufficient integration of closed technologies, have poor material and personnel flows, or rely on poorly designed aseptic interventions create repeated opportunities for aseptic breaches. When processes are not designed to minimize touchpoints and manual activities or first-air breaches, even the most skilled operators are placed in situations where human error becomes inevitable over time. In some cases, procedures are not defined to the minute details, leading each operator to perform them in their own preferred way. Variability in performing interventions also can arise due to individuals’ physical structure, such as height, arm length, agility, or ability to hold heavy objects. Process designs that depend heavily on operators' physical strength, stamina, or extraordinary mindfulness are inherently risky and are prone to failure.
Imagine being able to test aseptic processes hands-on before they are finalized. By immersing operators and SMEs in a virtual model of the facility and workflow, VR can help uncover challenges such as first-air breaches, awkward movements, hard-to-reach areas, and excessive manual handling before the processes are finalized for qualification. Teams can test interventions, refine material and personnel flows, and identify steps that are overly dependent on operator strength, precision, or agility. Early visibility into these risks ensures that processes are simplified, the potential for human error is minimized, and contamination risks are greatly reduced, leading to a more robust and operator-friendly process design.
How Does VR Address Deficient Training Programs?
In some organizations, training programs tend to focus primarily on meeting compliance documentation requirements, rather than being leveraged as a powerful tool for preventing human errors, strengthening contamination control, and building operational excellence. Often, training is heavily skewed toward theoretical knowledge, with limited emphasis on practical application and hands-on proficiency. While SOPs and protocols may be clear to those who develop them, they may not always fully resonate with shop floor personnel, who come from diverse backgrounds and learning experiences.
Additionally, identifying and accurately translating real-world performance gaps into learning opportunities remains a challenge. Though feedback mechanisms, such as observations on the shop floor, are commonly used, the quality and consistency of these observations, and how feedback is communicated, can vary depending on the proficiency and experience of the observers. Without a structured, well-calibrated approach that includes regular feedback, practical content, effective coaching, and training skills development, these initiatives may fall short of their full potential.
As a result, while personnel may be deemed "qualified" through observations and assessments on paper, their consistent execution of critical techniques like aseptic practices may not always meet required standards. The disconnect between training outcomes and real-world performance remains a significant factor contributing to contamination risks. Often, evaluators are under pressure to qualify the operators sooner, which can lead to a biased assessment.
VR can transform training programs from mere compliance exercises into immersive performance-driven learning experiences that drive real-world excellence. By offering a safe, controlled environment to practice, make mistakes, and improve, VR supports skill development on critical processes. Unlike conventional training methods that depend heavily on SOP reading or classroom lectures, VR engages multiple senses and strengthens muscle memory through hands-on simulated interactions. This experiential learning approach significantly boosts learning retention with greater confidence on the shop floor. Complex procedures are broken down into clear, intuitive steps, making them easier to grasp, even for individuals with varied educational levels or language proficiencies. Most importantly, qualification is no longer based solely on theoretical understanding but on demonstrated competence, ensuring readiness and reducing the risk of critical errors in high-stakes environments. Aseptic training maintains its integrity because operators must show their aseptic skills to pass the VR assessment, which is a plus during regulatory audits.
How Does VR Address A Lack Of Reinforcement Of Knowledge And Skills?
Training on the shop floor is not a onetime activity. Initial training alone does not ensure lasting proficiency in aseptic practices. Knowledge and skills naturally become irrelevant or erode over time without structured reinforcement mechanisms such as periodic refreshers, hands-on practices, and real-time performance assessments. Organizations that fail to integrate continuous learning into daily operations and mistakenly assume that completing initial training guarantees ongoing competency are taking a dangerous risk in contamination control.
VR enables the creation of continuous, scalable, and engaging reinforcement training without pulling operators off critical production duties for extended periods. Through brief immersive refresher modules, trainees can revisit key aseptic techniques, respond to realistic scenarios, and stay aligned with best practices on a regular basis. VR allows structured requalification cycles where performance is objectively assessed, not just based on memory recall but actual execution within simulated environments. This type of reinforcement through an active performance rehearsal helps to maintain high levels of proficiency over time and reduces skill erosion. VR also can log user performance data to identify individual or systemic gaps, enabling targeted follow-up and coaching.
Metrics captured by VR such as task completion time, procedural accuracy, frequency of errors, and number of repetitions provide deep insights into both individual capabilities and the overall effectiveness of the training program. This data-driven approach opens the door to adaptive learning. For example, a trainee may demonstrate strong proficiency in most parts of a procedure but struggle with just one or two specific steps. In a conventional training model, they would still need to repeat the entire module, resulting in wasted time and reduced engagement. With adaptive VR training, however, the system can guide the trainee to focus only on the areas requiring improvement, making the experience more personalized, efficient, and motivating.
Over time, these insights also help organizations identify common training challenges, fine-tune learning content, and provide targeted coaching. High performers can advance more quickly, while others receive the reinforcement they need, creating a more effective and learner-centric training environment.
While the potential of VR in the pharmaceutical industry is increasingly evident, from enhancing aseptic training to minimizing human error, realizing that potential requires more than just adopting new technology. Successful implementation demands a strategic, well-aligned approach that takes into account the organization's unique operational landscape, quality systems, and cultural maturity. To ensure VR becomes a true enabler of quality and compliance rather than just a novel tool, certain critical success factors must be thoughtfully addressed.
Key Success Criteria For VR Adoption
The pharmaceutical industry operates within a highly regulated and risk-sensitive environment. Introducing innovative technologies like VR or AR requires more than just enthusiasm — it demands thoughtful integration into established systems and processes. To fully harness VR for transforming training, optimizing operations, and strengthening compliance, organizations must address several critical success factors:
- Meticulous Planning and Clear Objectives: A successful VR implementation starts with clearly defined objectives and strategic, stage-wise planning. Transitioning from a non-VR to a VR-enabled organization is not an overnight shift — it’s a progressive journey. Begin by identifying specific pain points and high-impact areas such as aseptic interventions, manual critical processes, or activities requiring specific skills. Target the low-hanging fruit where VR can deliver immediate value; for example, improving process design or reducing human error. Equally important is cross-functional alignment: ensure that key stakeholders from quality, operations, and IT are engaged early and united by a shared vision for change. This collective ownership lays the foundation for a smooth and sustainable transformation.
- Balancing Theoretical Training and Hands-On Practice: Virtual reality is not intended to replace all training methods or convert every SOP into an immersive module, nor should it. This isn’t due to limitations of the technology, but rather because its true value lies in bridging the gap between knowledge and hands-on skill, particularly in areas that require human interaction, spatial awareness, and muscle memory. In the pharmaceutical industry, this is precisely where traditional training often falls short.
VR should be integrated as a complement to foundational theoretical learning, not a replacement. For example, pairing essential SOP or GMP content with immersive scenario-based practice enables operators to experience “learning by doing.” This dual-track approach deepens understanding, improves retention, and allows personnel to grasp not just what to do but why each step is critical for quality and compliance. When used strategically, VR fills the much-needed experiential learning gap in pharma training.
- Standard vs. Workplace-specific Scenarios: An effective VR training program often requires a thoughtful balance between standardized learning modules and customized workplace-specific content. Standard simulations can serve as a practical starting point, helping to build foundational understanding of technical concepts (e.g., first air, personal hygiene) that are broadly applicable across the pharmaceutical industry. These are particularly useful for onboarding and reinforcing core skills in a consistent manner and can be implemented organization-wide.
However, to resonate with operators working on line-specific tools and techniques, customization becomes an important consideration. Custom VR scenarios, reflecting actual facility layouts, equipment, SOPs, and risk points, can make the training more relatable and impactful. This can enhance engagement, comprehension, and application of learning to the real-world tasks. That said, the decision to invest in customization depends on several factors, including the organization’s current level of maturity at the shop floor, available budget, and the training priorities identified. Many organizations find value in adopting a hybrid approach, leveraging standard modules for baseline training while selectively introducing custom content for critical procedures or high-risk areas.
- Regulatory Compliance and Validation: In the pharmaceutical industry, the implementation of any new digital technology, including virtual reality, must be aligned with stringent regulatory and quality expectations. A risk-based validation approach should be adopted to ensure that the system consistently performs as intended and meets applicable compliance requirements.
It might be crucial to demonstrate consistent performance such as system reliability, data integrity, audit trails, user access control, etc. The job becomes easy when the VR solutions provider has a sound understanding of pharmaceutical quality systems, current regulatory expectations, and validation principles, in addition to a fair understanding of the technical subject matter. This builds trust, ensuring that the technology can be effectively integrated into cGMP-compliant operations.
To summarize, there are truly unique and persistent challenges in aseptic processes, such as, flawed facilities, weak process designs, less efficient training curricula, and gradual erosion of critical skills. These aren’t just technical gaps — they are cultural and operational challenges, too. While there is no overnight solution, VR technology brings a practical, future-ready way to close these gaps. When thoughtfully implemented, it doesn’t just deliver training, it builds confidence, sharpens execution, and embeds continuous improvement into the fabric of daily operations.
About The Authors:
Subrata Chakraborty, Ph.D., is a pharmaceutical consultant and trainer at INOPHAR Consulting & Training. With over 30 years of experience in pharmaceutical manufacturing and quality operations, he specializes in quality risk management, aseptic processing, and contamination control, ensuring alignment with global regulatory expectations. Apart from his role as a subject matter expert, Chakraborty has made a meaningful impact on people and organizational development during his leadership roles at Pfizer, Novartis, Fresenius Kabi, and Cipla. He is a recognized contributor to global industry platforms such as PDA, ISPE, and SfSAP, frequently volunteering as an author, speaker, and technical reviewer.
Ajay Pazhayattil, Ph.D., is an accomplished management consultant and industrial pharmacist with extensive experience spanning solid oral, sterile, and API sectors. He is the founder of cGMP World. Pazhayattil has held key leadership positions with prominent North American brands, generic manufacturers, and CDMOs. His roles include vice president of scientific and regulatory affairs at Capcium, quality director at Eurofins, and associate director at Apotex. He plays a pivotal role in guiding organizations through remediation efforts related to U.S. FDA 483 observations and warning letters. He has been a lead author and contributor to guidance documents published by industry organizations such as AAPS, PDA, ISPE, and RAPS.