Takeda's Green Approach To IG Purification And Filling
A conversation with Geoffrey Pot, general manager of operations, Takeda Lessines
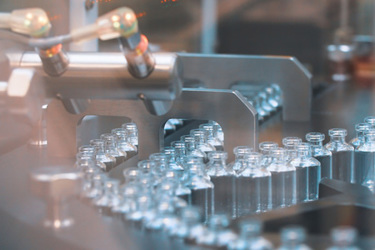
Bioprocess Online and ISPE are collaborating to showcase the 2023 ISPE Facility of the Year sponsor company winners. In a limited series, we hear from industry leaders at three companies, Genentech, Serum Institute, and Takeda, which all earned awards.
Takeda won an ISPE Facility of the Year Award (FOYA) in the social impact category for the design of a new manufacturing building for plasma-derived products at its Lessines, Belgium, campus.
The company boasts a self-reliant energy infrastructure, paperless processes, and a waste management program, which includes a wastewater treatment plant that produces potable water. Takeda aims to reduce freshwater consumption by 90% by 2025 and achieve carbon net zero in its operations by 2030.
Beyond the gentler environmental effects of green construction, building sustainably has long been shown to have financial advantages with lower utility and maintenance costs. The greater initial investment, however, often scares builders off.
We hear from Geoffrey Pot, general manager of operations at Takeda’s site in the southern French-speaking part of Belgium, about the decisions that went into the company’s award-winning build and what they learned that can help any biotech company, large or small, start thinking about sustainable operations.
Bioprocess Online: Takeda's plasma-derived therapies program wraps the world. Why Lessines, Belgium, for this facility?
The combination of this long-time expertise in the field of purification, as well as a highly skilled workforce that has demonstrated its commitment and ability to deliver these life-transforming treatments, was instrumental in choosing Lessines. Moreover, Takeda Lessines is evolving in a very developed biotech ecosystem, with Belgium being a center for highly educated international researchers and employees, thanks to the presence of renowned universities with world-class research institutions and major industry players.
Bioprocess Online: Does anything about manufacturing plasma-derived therapies lend itself to sustainable manufacturing, or can these systems be used for any biopharmaceutical product?
Pot: A lot of what we do at Takeda Lessines can be transferred to other biotech companies.
The manufacturing process of plasma-derived therapies is particularly energy-intensive and water-intensive. We are approaching sustainability holistically from the supply of raw materials to the site to the production of therapies and the shipment of vials of finished products to over 80 countries. Our entire value chain is constantly being analyzed to reduce its environmental footprint wherever possible.
In order to recycle its wastewater for example, Takeda Lessines built a wastewater treatment facility on-site in partnership with Ekopak in 2021. This system helps the site to reduce up to 60% of its freshwater withdrawal. Aside from that, the site is sourcing 100% renewable electricity. By 2026, Takeda Lessines aims to produce 80% of its electricity consumed on-site through photovoltaic panels, wind energy, and geothermal energy. The site also puts a lot of effort into waste management. All the waste is either recycled whenever possible (e.g., used to produce transportation pallets) or incinerated with energy recovery from the burning process.
Moreover, the site has installed containers that compress the plastic waste and other materials before their transportation. Compressing plastic waste reduces volume and lowers the number of truckloads to recycling facilities. The combined effect is a 13.6-ton reduction in site-attributed CO2 emissions.
There is a continuous effort to identify and organize new recycled waste streams (e.g., rigid plastic) and also to reduce the overall waste on site. The treatment of sludge from the wastewater treatment plant is an example of helping reduce our carbon footprint and new recycling opportunities.
Takeda has invested in a centrifuge to dewater the sludge to reduce its weight and volume. This contributed to a carbon footprint reduction of 15 tons of CO2 equivalent per year. Furthermore, the site is currently in the approval process to valorize its sludge through bio methanation. This is a process in which a natural selection of microorganisms decomposes organic matter through anaerobic digestion, in the absence of oxygen, into biogas and a stabilized solid residue.
In 2022, the Lessines site obtained the Logistics in Wallonia organization’s Lean & Green label for having thoroughly reviewed its logistics footprint. Several initiatives were implemented, such as switching the transportation mode for finished products from air to sea (2022 global sea freight ratio versus air: 47.5%,). The construction of a net-zero GHG emissions warehouse will make it possible to centralize all the storage capacity at a single site, reducing the site’s road transport needs.
Bioprocess Online: Beyond the initial investment, how do maintenance costs compare to maintaining legacy infrastructure?
Pot: As all our facilities have their own specifications, it’s hard to put a number on the costs. What we know from experience is that maintaining legacy infrastructure requires more frequent repairs and replacements due to wear and tear, dated technology, and sometimes a lack of available replacement parts.
Moreover, as technology is evolving faster than ever, legacy infrastructure is not as energy efficient as newer facilities, resulting in higher utility costs. This is the reason why at Takeda when designing new buildings and production facilities it is always with energy efficiency in mind. Furthermore, these new facilities are also equipped with smart building management systems that help optimize our energy usage as well as advanced monitoring and control systems, which can help identify and address maintenance issues before they become major problems.
Bioprocess Online: Redundancy or reliability? When designing renewable power infrastructure for biologic products, how do you make decisions to prevent system failure?
Pot: Striking a balance between redundancy and reliability is crucial. Relying solely on a single type of renewable energy source can be risky, as it leaves the system vulnerable to failure if that specific energy source is unavailable. Therefore, it is prudent to incorporate redundancy measures while ensuring a reliable flow of electricity.
This involves deploying a mix of energy generation technologies to diversify the energy supply. By combining different renewable sources, such as wind turbines, photovoltaic panels, and geothermal energy, the system becomes less reliant on a single source and more resilient to fluctuations in energy availability.
Our goal is to ensure both redundancy and reliability in renewable power infrastructure.
Bioprocess Online: Many biotech companies, especially startups, lack the capital to build wastewater treatment plants and dig geothermal wells. What are some small, less obvious steps to reduce process-related consumption?
Pot: It’s all about sustainability by design, the heating, ventilation, and air conditioning (HVAC) system, for example, plays a critical role in this journey as we know that energy demand related to cleanliness parameters for GMP facilities is a big portion of a facility’s energy needs. By optimizing HVAC settings and room design, it is possible to improve the environmental footprint of cleanroom environments.
Also, reducing the water needed in the process, especially for cleaning purposes, is a big energy saver (on top of being key for critical resource preservation) as every liter saved will help preserve a natural resource.
And once you have looked into reducing your consumption, the next area to consider is recovery. For existing facilities, knowledge of your consumption profile is a must to develop a sound energy reduction program.
You need to gather data on energy consumption from equipment and systems, identify areas where lighting, heating, and ventilation are used, analyze the data, and identify energy-saving opportunities. It’s a lengthy process, especially for old facilities, but it will definitively help you to develop and implement a robust plan.
About the Expert: Geoffrey Pot took the lead as site head of Takeda Lessines in 2020. He has worked for the company since 2004, holding several roles of increasing responsibility in quality, operational excellence, project management, manufacturing, and innovation. As general manager, he oversees 1,200 employees at the Lessines site, which focuses on purification with filling and packaging capabilities for plasma-derived therapies. It is also a packaging center for products used to treat blood disorders.