Support Of Scale-Up And Technical Transfer Through Understanding Equipment
By Girleigzoaryt Sioacnha, Ph. D.
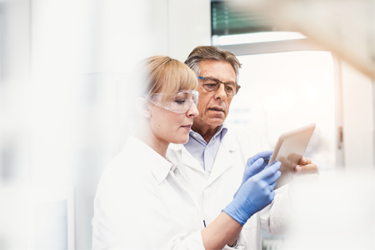
Formulation and process development for injectable products are typically carried out at the laboratory scale. Laboratory-scale equipment plays a crucial role during this phase, particularly when technical information is limited and when the active pharmaceutical ingredient (API) is scarce. While scaling up production for solution formulations generally poses few challenges, the complexities significantly increase when the formulation is intended for lyophilization.
One major issue is that the design of lyophilizers can vary significantly between laboratory-scale and full-scale production, as well as among different manufacturing sites. Laboratory studies often utilize lyophilizers with small product chambers, typically around 0.43 m², whereas full-scale operations require much larger equipment, often exceeding 19.95 m². This substantial increase in chamber size and the corresponding differences in equipment design can impact heat transfer dynamics within the lyophilizer and affect overall equipment capability.
These variations can have profound implications for the success of the scale-up process and technical transfer. As such, it is essential to carefully consider these factors to ensure a smooth transition from laboratory-scale development to full-scale manufacturing, ultimately leading to the successful production of high-quality lyophilized injectable products.
Get unlimited access to:
Enter your credentials below to log in. Not yet a member of Bioprocess Online? Subscribe today.