Strategies To Maximize Batch Yields In Aseptic Manufacturing: High Value Actives
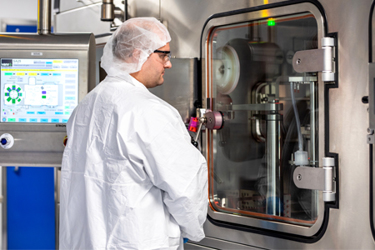
Advances in drug and biologics discovery have allowed the development of increasingly sophisticated and highly targeted therapeutics. The active ingredients, whether small molecules or biologics, have become increasingly complex and costly to manufacture. One source suggests that large molecule therapies cost on average more than twenty times what it costs to produce a typical small molecule1. Because of the physical properties of most biologics, the route of administration is typically parenteral and therefore it is imperative that manufacturers of sterile drug product develop strategies to maximize their yields and minimize losses throughout the finished product production process.
A natural consequence of the trend toward more targeted therapeutics is that patient populations for a given product have generally trended downward as researchers have developed products focused on highly specific disease targets. In some instances, especially in orphan indications, the global patient population may be only a few thousand or even smaller and a clinical trial for a new orphan therapy may require only a few hundred doses for administration to patients. Finished dosage batch production to support a clinical trial in such an instance may involve formulation of only a few grams of active ingredient. This stands in stark contrast to more conventional injectable therapies that might target broad patient populations and where the active ingredient is a relatively simple, plentiful, and inexpensive material.
Handling high-value, complex active ingredients requires an aseptic dosage manufacturer to adopt a mindset that rigorously protects against unnecessary loss of active ingredient. While some losses may be the result of accidents such as breakage, spillage, or errors related to formulating, others are inherent to GMP manufacture. Such inherent losses are the result of the need to sample and test the bulk material prior to initiating finished product manufacture, in-process control testing, finished product release testing, stability studies, and GMP requirements to retain reserve samples of both the active ingredient and finished product. Failure to take into account the often very small batch sizes involved in highly targeted high-value product manufacturing can result in unacceptable loss of precious bulk active materials.
It is imperative, therefore, that aseptic drug product manufacturers adopt appropriate strategies to maximize the final yield of the products they produce. In broad terms, potential losses may occur as the result of planned consumption of the active ingredient related to quality control-related testing, or production-related losses whether inherent to the manufacturing process or unplanned/accident.
Get unlimited access to:
Enter your credentials below to log in. Not yet a member of Bioprocess Online? Subscribe today.