Stopper Functionality – Key Considerations
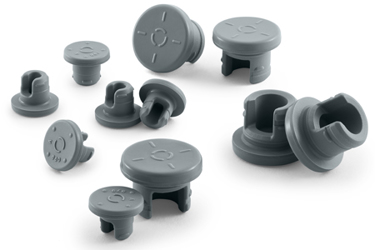
When selecting the appropriate rubber stopper for any respective vial containment system, there are many aspects to consider regarding the properties of the elastomeric closure. For the purposes of this discussion, the focus will be on the functional performance of the stopper and what key aspects should be considered during the assessment and selection process. Coring and fragmentation, container closure integrity, and machinability of the stoppers will be briefly reviewed.
It is also important to consider for all these assessments that they are conducted under pharmaceutically representative conditions, when possible, such as ensuring components are lubricated, washed and sterilized as intended for commercial use.
Coring and Fragmentation
A point to consider in piercing a rubber stopper with a needle is the formation of cores and fragments. Their presence in a drug is a critical concern. Both are considered particulate matter, however they are caused by different mechanisms:
- Cores – characteristically cylindrical in shape, cores formed by the needle cannula cutting the rubber during needle penetration.
- Fragments – characteristically small with irregular shape, fragments are formed via an abrasion of the rubber by the outside of the needle cannula during needle penetration.
If particles are small enough to be drawn into the syringe, and subsequently injected into a patient, there is a potential risk to patient safety. There is also a risk that the cores could be substantial enough that the rubber stopper is unable to seal when the needle is removed, therefore potentially exposing the drug product to environmental conditions and contamination.
These issues can be mitigated through needle and technique selection.
Needle:
- Thinner (i.e., higher gauge), e.g., 27 gauge
- Blunted bevel heel and sharp point
- Use only once
- Consistent lubrication on the needle surface
Technique:
- Puncture within the target circle on the stopper
- Insert at proper angle
- Insert needle slowly
- Do not rotate during insertion
- Note, multiple punctures increase the chance of coring and fragmentation
Container Closure Integrity
Container closure integrity (CCI) is an essential element of a drug product container system. The sterility, stability, and efficacy of a drug product over its target shelf life is directly correlated to the container system’s ability to ensure a leak rate below that of a predefined maximum allowable leak limit (MALL). This topic is detailed in USP guidance: Chapter <1207> Package Integrity Evaluation – Sterile Products. The guidance provides insights into various CCI test methods, while further emphasizing the use of deterministic methods (e.g., trace gas leak detection), where possible, and using probabilistic methods (e.g., trace liquids) only when appropriate for the application.
Selecting the appropriate test method and MALL is a critical first step when challenging a vial containment system. There are many factors to consider when selecting the method, such as the specific application and critical attributes. West has built capabilities to evaluate container systems using numerous different techniques, however Helium Leak Detection and the associated Kirsch limit (6.0 x 10-6 cm3/s) has become one of the most common methods used to assess containers systems given the effectiveness of the method, as well as the versatility for directly testing container systems in cold and cryogenic storage.
No matter the test method chosen for assessing a vial containment system, it is important to keep the following factors in mind, just to name a few:
- Compression forces applied during the crimping process
- Hardness of the rubber stopper
- Cleanliness of the sample preparation environment
- Dimensional compatibility of the vial, stopper, and seal
- Empty or filled vials (e.g., liquid presence and the type of liquid, partial pressure, gas overlay)
Machinability
Machinability is a term used to describe the effectiveness of a component (e.g., container, stopper, plunger, or seal) processed on a drug product filling line. The machinability of components can have a direct impact on the yield and processing time of the drug product, as well as on the required functional aspects of the container system.
To optimize operations and reduce risks attributed to the container system, preliminary machinability assessments are often conducted during packaging development; followed by more extensive machinability assessments during process development and validation. During these machinability assessments there are numerous key factors that should be considered:
- Dimensional compatibility of the various components of the container system
- Dimensional compatibility of the components with the equipment format (change) parts
- Stopper characteristics, such as lubricity, hardness and center of mass
- Stopper processing parameters associated with the feeder bowl, stopper insertion, and capping
- Quality and Operation requirements and specifications (e.g., raised stopper detection specifications, drug product “time-in-solution” limits, product/process deviation rates)
- Pharmaceutically representative condition of the equipment format parts both in terms of maintenance and cleanliness
To learn more about the design for 4040 LyoTec® lyophilization stoppers that facilitate machinability, click here.
LyoTec is a registered trademark of West Pharmaceutical Services, Inc. in the United States and other jurisdictions.
Need More Information? Just Ask.
Click the button below to directly contact the supplier. Use it to:
- Ask a question.
- Request more detailed information or literature.
- Discuss your current project/application.
- Request a quote.
- Locate a distributor in your area.
- Schedule a demo.