7 Steps To Accelerate Biopharma Manufacturing Processes
By Greg Anthos, Tunnell Consulting
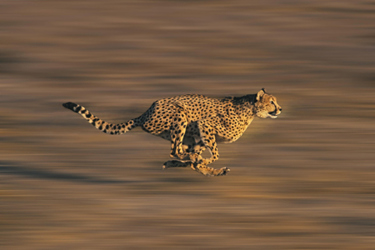
Good manufacturing process capability and control is a critical success factor for emerging biopharma companies facing accelerated timelines and constrained resources. Expedited manufacturing processes, often due to fast clinical timelines, present challenges in achieving optimal performance that is repeatable. This is compounded by limited access to product development expertise compared to larger pharmaceutical counterparts, potentially leading to increased costs and possible supply chain disruptions.
In this article, I delve into strategies for overcoming these challenges, focusing on expedited process characterization and identification of critical material attributes (CMAs), critical process parameters (CPPs), and critical quality attributes (CQAs). Through collaborative problem-solving and optimization, small biopharma firms can enhance manufacturing performance, reduce costs, and improve patient access to innovative therapies.
The Evolution Of Biopharma Manufacturing Challenges
The landscape of biopharma manufacturing has evolved significantly, with advanced therapies and breakthrough approvals reshaping the industry's critical path to drug approval. Traditionally, the clinical program was on the critical path, but now, process development and product manufacturing also can be on the critical path, requiring rapid development.
Moreover, the cost dynamics have shifted dramatically. While solid dosage products once had relatively low manufacturing costs compared to overall product revenue, advanced biologics and gene therapies incur substantial manufacturing expenses. These costs impact patient access and influence payer decisions regarding funding for these therapies. Now more than ever, manufacturing capability can make or break a product's success.
Accelerated approvals further intensify the challenge. The compressed timelines necessitate swift development of complex biological manufacturing processes, a task exacerbated for small biotech firms with limited resources and funding compared to larger pharmaceutical companies.
7 Steps For Addressing Accelerated Manufacturing Challenges
To navigate these challenges effectively, small biopharma companies must adopt strategic approaches to invest time and resources to prioritize process understanding and optimization.
1. Comprehensive Data Collection and Analysis
The foundation of successful manufacturing optimization lies in comprehensive data collection and analysis. Instead of treating each batch as a separate experiment, a systematic approach involves collecting manufacturing process data and corresponding lab test results consistently. This rich data set provides insights into CMAs, CPPs, and CQAs, laying the groundwork for optimizing process control and performance. This data collection and analysis ideally should start early when the product is still being developed in the lab before full-scale manufacturing. Since the batches are so costly and limited in number, all data is valuable to provide insights.
Utilizing a standardized Excel template for data collection and trending can streamline this process, facilitating the identification of trends, process shifts, and critical parameters within the manufacturing process. Visualizing data through graphs and trend analyses aids in identifying patterns and anomalies that impact process performance.
2. Methods
The analytical methods of lab testing will be the eyes of the manufacturing process and need to be in place and qualified to provide reliable lab test results from each batch manufactured before clinical production. These complex lab tests, including bioassay, can be difficult and time-consuming to develop, and focus should be on this task early in the process to ensure success. Once you have a robust set of analytical methods then you can focus on the manufacturing process development with good and reliable information.
3. Collaborative Problem-Solving
Collaboration across multidisciplinary teams is crucial in gaining a deep understanding of the manufacturing process and optimizing performance. By bringing together a team of a product development scientist/process engineer, statistician, data analyst, and project manager, small biopharma firms can leverage diverse expertise to address challenges effectively. It is important to have these different perspectives and expertise to gain manufacturing process understanding and insights.
Direct observation, interviews, and hands-on engagement with manufacturing and lab testing processes provide invaluable insights into process variations, root causes of problems, and conditions for optimal performance. This collaborative approach fosters a culture of continuous improvement and problem-solving, essential for navigating complex manufacturing challenges.
4. Process Characterization
Early in the manufacturing process development, it is a best practice to perform manufacturing process characterization. This process is normally initiated by performing a risk assessment of the process. The risk assessment serves to identify the greatest risks to the manufacturing process not meeting lab release specifications and to develop process mitigation to reduce the risk of out-of-specification results. Next, at small or lab scale, conduct designed experiments to help determine the CMAs and CPPs that control the CQAs. This will be the basis for the manufacturing control strategy and help to develop a robust manufacturing process. When companies skip this step, it can cause significant risk that could impact health authority approval or supply chain disruption. Today’s complex biologics require significant effort and focus on process characterization to be successful.
5. Statistical Analysis and Process Optimization
Statistical analysis plays a pivotal role in optimizing manufacturing processes. Through bivariate and multivariate analyses, significant parameters impacting CQAs are identified, leading to the development of predictive statistical models. These models help determine optimal CPP settings, ranges, and process control strategies, ensuring consistent and robust manufacturing performance. Equally important, these models can define CPP settings that could produce a failing CQA result. As a result, you will know the CPP settings that produce the best results in terms of meeting specifications the highest percentage of time and the best settings for optimal yields.
By validating these models against historical data and executing manufacturing runs at optimal CPP settings, biopharma firms can confirm CQAs and key parameters' performance. Continued process monitoring and trend analysis further enhance process control and identify potential issues before they result in out-of-specification results.
6. Continuous Improvement and Adaptation
The journey of optimizing manufacturing processes is iterative and requires continuous improvement and adaptation. As manufacturing processes mature, the accumulated data, process knowledge, and statistical models serve as valuable assets in addressing potential issues proactively and ensuring ongoing process optimization. Over the life of a product, many things can change that can impact process performance, such as changes in material characteristics or sources, changes in equipment/machinery, changes in personnel, and changes in procedures. It is important and required by the health authority to monitor the manufacturing process for any changes to the validated state or trends. The FDA requires CPV (continuous process validation) to ensure you are maintaining the manufacturing process in a validated state.
7. Leveraging Advanced Technologies
Leveraging advanced technologies such as data analytics, artificial intelligence, and machine learning can enhance process monitoring, predictive modeling, and decision-making in manufacturing optimization. Small biopharma companies can leverage these technologies to drive efficiencies, reduce costs, and improve overall manufacturing performance.
Case Study: Let’s Apply These Steps To A Real-Life Scenario
Consider a small biopharma company with a commercial monoclonal antibody product where fermentation yields for its mammalian cell culture process dropped 18% while demand for the product was rising and additional manufacturing capacity was needed.
The Approach: Using the seven-step approach, the company collected historical data and conducted statistical analysis and used a cross-functional team to observe the process, interviewed those working on the process, and developed a statistical model to explain 70% of the yield variation and key drivers.
The Results: Raw material specifications were established to ensure consistent fermentation yields. The changes implemented returned yields to the normal level and market supply was met. Key outcomes include enhanced process understanding, reduced variability, and increased process capability. These improvements not only ensure compliance with regulatory requirements but also contribute to cost reduction, improved patient access, and sustained innovation in biopharma manufacturing.
Conclusion
Accelerated biopharma manufacturing presents unique challenges that require strategic approaches, collaborative problem-solving, and data-driven decision-making. By prioritizing process optimization, leveraging diverse expertise, adopting statistical analyses, and embracing continuous improvement, small biopharma companies can navigate challenges effectively and achieve their product’s manufacturing goals.
The journey of optimizing manufacturing processes is ongoing, requiring adaptation to evolving industry trends, regulatory requirements, and technological advancements.
About The Author:
Greg Anthos is a principal and operational excellence leader at Tunnell Consulting. He has more than 30 years of experience in the life sciences industry, including over a decade of consulting experience in all business functions, with significant expertise in engineering, organizational transformation, and supply chain. He can be reached at greg.anthos@tunnellconsulting.com.