Single-Use For Fill-Finish: Is It Worth The Risk?

By Christopher J. Smalley, compounding pharmacist advisor, ValSource
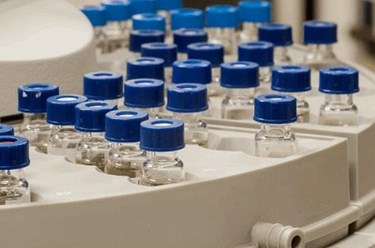
Single-use technology is a potential solution to some of the problems that have long plagued the fill-finish portion of the pharmaceutical manufacturing process. Aging facilities can contribute to some of those problems, as can capacity issues, where changeover times limit the pace of manufacture.
However, it is important to remember that single-use is not a hammer, and every problem you encounter is not a nail. There will always be circumstances where stainless steel, and even glass lined tanks, will be part of the optimal solution.
The question that needs to be asked is: When is it appropriate to consider single-use for fill-finish processes? After all, single-use is frequently used in upstream processes, such as media and buffer preparation.
So why are upstream applications of single-use technology so popular? Because upstream carries less risk than downstream when evaluated against the two largest concerns associated with single-use: leaks and leachables. Media and buffers have less value than the final product, so an upstream leak that results in media or buffer throwaway is not a large risk. Plus, subsequent processing steps will remove the majority of any leachables that might migrate into the media or buffers.
For fill-finish applications of single-use systems, you need to make sure you are looking at the right risks. What are the risks to your fill-finish process? What causes batch deviations — or worse, batch rejections? Have you compared the risks between your current process and a single-use solution?
Risk Assessment For Aging Facilities
For many manufacturers, the starting point for performing a risk evaluation incorporates the risks of an aging or inadequate facility. Keep in mind that the term “aging facility” doesn’t only relate to the age of the facility or equipment. Deterioration of systems often depends on how adequate the preventive maintenance (PM) program is or whether a predictive maintenance (PdM) program has been instituted. Additionally, a facility may have become inadequate due to regulatory expectations that have changed (frequently due to some other manufacturer’s crisis). Or, processes may not have been robust to begin with, owing to the rushed launch of a product without taking the time for product optimization.
Another good example of a risk periodically encountered is a facility design that is incompatible with current process and/or personnel flows. This can result from changes to the process flow in the building, or from well-intentioned changes to the existing building — perhaps a new equipment entryway in one wall, or a personnel airlock with requisite pressure differential changes added to another wall.
When performing the risk assessment, the factors that created the circumstances don’t matter; what matters are the results. Regardless of whether you have a new fill-finish assembly or a legacy fill-finish assembly, the questions become:
- Does it ‘fill’ your needs?
- Is it prone to problems?
- Does it have the filling speed and reliability that you expect and need?
Benefits Of Single-Use Technology
How, then, can single--use technology help address the risks associated with aging or inadequate facilities?
One key is flexibility. We have all experienced marketing forecasts that predict great sales for a new product, but do we want to build permanent capacity based on unproven forecasts? A single-use solution could meet the actual requirements for launch and then ramp up to sales stabilization without large capital outlays or disruption to an operating facility.
But is scaling to a sales forecast the right risk to mitigate for your facility? Again, you need to ask the right questions. What are the risks to your fill-finish process? What causes batch deviations or batch rejections?
Another situation that may pose a risk is the approaching end of a product life cycle. Perhaps a competitor is about to launch a new therapeutic entity, accelerating the end of your product. How do you ramp down capacity for that product and quickly free it up for others? Would you be confronted with the need to update validation, such as cleaning validation or sterilization-in-place (SIP) validation for a process that is going away? Neither cleaning nor SIP validation would be needed for a single-use solution.
Other advantages of single-use include:
- Reduced water usage
- Reduced demand on autoclaves if the single-use assemblies have been gamma irradiated
- Quicker changeovers, because you aren’t waiting on cleaning and drying of parts
- Ability to autoclave or incinerate biohazard or high-potency contaminated parts
Downstream Risks — And How To Mitigate Them
Now, let’s talk about the risks that single-use can introduce to the process. First, there is the issue of extractables and leachables. Perhaps the greatest risk is the fear that a regulatory inspector will ask questions about extractables and leachables and that “enough might not have been done.” Second is the issue of leaks, which might be a fear not because the organization has had leaks, but because there have been rumors of leaks. We will explore each of these two risks in further detail in the following sections.
Extractables And Leachables
Extractables studies can produce results that may appear alarming — for example, extractables studies performed on Type I borosilicate glass can demonstrate lead and arsenic as part of the results. When we see such results, are we going to stop using ampoules and vials? No, because leachables studies, even when performed over the shelf life of the finished product, will not yield those results. And remember, the final product is in contact with the glass for years, while the product is in only contact with fill-finish components for hours.
How can you mitigate the risk of the extractables and leachables issue? One option is to create a design space for your fill-finish operations. In doing so, answer the following questions:
- What is your longest fill-finish operation time?
- What is the pH range of your final products?
- What is the temperature range of your final products?
- Is there a model solvent that encompasses most, if not all, of your final products? (Hint: Look at your filter validation for model solvents selected.)
Once the design space has been created — and you may choose to build a design space around a family or grouping of products, if including all products will result in an unwieldy design space — perform studies using those parameters. Conduct the studies on components in direct product/process contact for primary suppliers, as well as for secondary suppliers that are in place for business continuity purposes.
Include in your study all components down to connectors and end caps, so long as they contact materials that will be included in the final product (not flush bags or other non-process related components). Ensure that you understand the characteristics of the components. For instance is the component autoclaved, gamma irradiated, fresh (received just in time), or stored for some time? Why would that last issue matter? Some components have semi-volatiles that will dissipate during storage. For example, some silicone tubing will appear oily when fresh, but in storage that silicon oil will volatilize off.
A library of the design space for components in use in a facility will result in significantly less work (and time) for addressing the extractables and leachables issue than would testing to assure that extractables results are in place for all components for each application.
Leaks
What of the risk of leaks? You may have heard rumors about leaks, but have you actually experienced leaks? If you have experienced a leak, do you know what caused it? Would the leak in fill-finish have been any different if a legacy system were used instead of single-use? For example, do both systems use tubing, hose barb connectors, and a clamping system? Is that where the leak occurred? Is single-use to blame?
What are the best ways to mitigate the risk of the leak issue? First, confiscate all box cutters. Second, make sure that all personnel involved are properly trained on handling single-use systems, from the receiving dock through to the aseptic filling suite.
If a leak does occur, document it, save the component, and work with your supplier to determine the root cause.
Conclusion
Single-use systems can be a great advantage in fill-finish operations, since they can:
- Reduce manual manipulations and connections,
- Improve capacity management with quicker changeovers,
- Better manage hazardous contaminated components, and
- Increase facility capacity without adding water for injection (WFI) generation or autoclaves.
All of these advantages present opportunities to improve flexibility, if you can rationally address the risks. Evaluate single-use — it could be the solution your facility needs.
This article is based on a presentation made by the author at BioWeek Boston 2016.
About The Author:
Chris Smalley recently retired from Merck, where he had responsibility for innovative implementation and validation, including single-use systems, globally. Previously, he was director of quality operations for Wyeth Pharmaceuticals for 12 years, with responsibility for setting validation standards and validation activities globally. His research experience includes responsibility for quality in the U.S. operations of the Sanofi Research Division, and earlier he worked for the Johnson & Johnson family of companies, where he was a plant manager. Chris is a graduate of the Philadelphia College of Pharmacy of the University of the Sciences in Philadelphia. His graduate education includes an MBA from Temple University’s Fox School of Business and an MS in pharmaceutical chemistry from Temple University School of Pharmacy.
Chris has been a member of the PDA Board of Directors, as well as a member of the PDA Science Advisory Board. Currently he is a member of the ISPE Disposables Community of Practice (COP). You can reach him at Chris.j.smalley@gmail.com or on LinkedIn at linkedin.com/in/chrisjsmalley.