Shocking! Biotech Facilities Don't Maintain Themselves
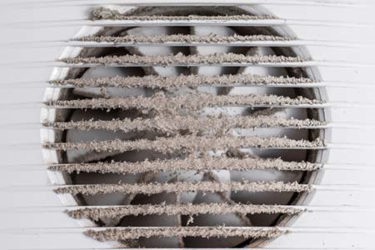
In the first part of our series, which reflected on common errors we’ve seen over and over again in the pharmaceutical and biotech industry, we discussed operational issues that focus on cleanliness and operator commitment. In this installment, we will focus on simple maintenance issues that we see as chronic and decades-old problems across the industry.
Some maintenance managers believe that once you build a facility you only must be concerned with the process equipment inside, and the rest of the facility will take care of itself in perpetuity. Some maintenance groups get trapped in focusing only on the process systems. This happens particularly on new buildings and recent renovations, where managers are challenged to obtain budget to continue to invest immediately after a major capital expenditure.
The idea that those “non-value-adding” systems can skip investing is too pervasive. It is like buying a new car and skipping oil changes until something fails.
We all know the reality of maintaining a plant; however, some organizations compromise their facilities and rationalize a series of high-risk decisions over several years to put their plant in financial strength but place the enterprise in regulatory peril. Maybe they do not understand the risk and simply rationalize their jobs as maintaining the status quo or they simply do not understand the intricacies of a complex plant.
Regardless of the reasons, we have a brief discussion on a few of the most common critical lapses in maintaining an injectable drug-producing facility.
We have repeatedly seen all the following in failing facilities.
Don’t Worry, The HEPA Won’t Bite, So Change It
HEPA filters should hold a special place in the hearts and minds of our facility managers since they ensure the cleanliness of the air in our manufacturing. We have come across facilities with the same HEPA installation intact for up to 30 years without a filter changeout except when they fail. As the installation ages, the number of HEPA failures increases. HEPAs, like all things in this world, do not last forever. Based upon the recommendations of the pharmaceutical filter manufacturers, the material integrity is only guaranteed for between 10 and 12 years. In addition to the HEPA filter material and the adhesive system, there is the installation “can,” fasteners, and the gel seal, all of which are under constant pressure and vibration.
In our travels we have seen these aging HEPA installations fighting particle testing not only on the filter face but at the edges of the unit. This result requires a teardown of the grid, extended outage of the suite, rebuilding, retesting, and “keeping their fingers crossed.”
Another key aspect is the long-term effect of filter loading. As we all know, delta P across any membrane is equal to a K*air density*velocity^2 /2 gc. Therefore, as the filter ages, the delta P increases, and the velocity that we validated for the filter deteriorates. When we then perform the periodic HEPA certification, we may pass the particle count but fail on velocity profile, thus forcing a deviation, investigation, and replacement of the filter.
Let us now look at this from a QA and regulatory standpoint and ask the question of how long the HEPAs were failing (since the last acceptable test) and what products were made, compounded, dispensed, and exposed in that suite since the last successful test. Now we must do a product lookback from a bioburden or sterility standpoint and assess the consequences of the failure, and in many cases, we may have to withdraw the product from the market.
The bottom line is the HEPAs must be changed out on a suite-by-suite systematic approach in which 8% to 10% of all the filters are changed each year. If any filters fail during the annual or bi-annual testing, they must be discarded and not repaired. During the HEPA changeout, the grid installation and gel must be inspected. The handling of the HEPA media must be done by a professional (no hands on the media) and, finally, a successful particle test must be performed.
You Really Should See What’s Growing On Your HVAC Coils
In the realm of HVAC systems, another area that is consistently missed because it is either time-consuming, inconvenient, or considered “these last forever,” is the HVAC coil systems and condensate drains. Over time, the coils build up and become encrusted with microbial and fungal growth, thus becoming a contamination point and reducing the efficiency of the coils (lower Uo).
The drain system under the coils consists of drain pans, fasteners, brackets, conduit, drain screens, and the actual drain. These are built with a variety of metals and corrosion is a fact of life, especially in older pharma facilities. This corrosion contributes a layering effect on the drain screens and drain body and, ultimately, the drain will become clogged, and the condensate water will build up in the receiving pan and overflow into the plenum and ductwork. This typically will not be noticed until a catastrophic event occurs, such as the terminal HEPAs becoming saturated with water and dripping, or pooling is discovered in one of the plenums.
All HVAC systems need to be inspected at each major turnaround, with the coil system cleaned, drains cleared, anti-microbial UV lights replaced at the coils, fasteners/brackets replaced, and the drain pan recoated with antimicrobial paint.
Inspect For Rust At Least Quarterly, And Watch For It Constantly
Operators, as well as maintenance personnel, should constantly watch out for rust and rouge on the inside and outside of process vessels. Interior rust or rouge is a serious GMP issue, and the presence of rouge constitutes a non-GMP environment and must not be tolerated.
The operators, when executing a batch, are generally required to inspect the vessel’s interior before committing the batch. Common day-to-day observation may not be visually effective or even noticed. The key is a minimum of quarterly inspections of all stainless-steel process vessels, with each tank’s interior photographed. The comparison of each inspection’s photograph will provide a basis for determining the vessel’s de-rouging or routine passivation. Depending on the vessel’s frequency of use, CIP cycles, and process materials, some stainless-steel vessels require bi-annual passivation, while others can last up to two years.
The frequency depends on the observations and the risk indicated by the discoloration of the surface. The key is keeping an inspection and photographic history of each process vessel.
The observation, inspection, and data capture should also be done on the vessel exteriors, especially if the vessel is inside a classified space. Rust build-up on any steel surface is problematic from a microbial and cleanliness standpoint. Vessel exteriors can be de-rouged as needed, with a periodic passivation, depending on the environment, ranging from one year to five years. Remember, the lack of ions in WFI, particularly in hot WFI, will erode normally unreactive materials like stainless steel and glass. Check the spray ball impingement points on hot WFI storage tanks.
Replace Those O-rings With Welded Connections
Many purified water (PF) and water for injection (WFI) lines wind their way through most facilities with extensions and drops added on over time. Branch lines need to be borescope inspected on a yearly basis or when the system is taken down for passivation.
Most systems are completely orbitally welded; however, many older systems are flanged and gasketed with Viton O-rings. In the past, we have walked into the water generation mechanical areas and needed raincoats to inspect the lines due to the O-ring failures, vibration, and general deterioration of the system. O-ring flanges need to be removed and migrated to all welded connections. Often because of the age and the poor documentation of these systems, the current maintenance personnel are not aware of the decisions made 30 years ago and blindly accept the installation as is. The Viton O-rings deteriorate over time and shed small black particles into the water, which can show up in the product solution. Sometimes, the CIP spray balls contain these black specks, and that should be the first clue that there is an imminent problem.
The use of O-rings is more prolific in air and nitrogen systems; here again, nothing lasts forever, and these need to be replaced over time or risk shedding particles into the gas stream. The key here is documentation of changeovers and adhering to a replacement schedule.
From The Floors To The Doors
What is something you use every day, constantly (more than the process equipment) and rarely given a serious thought? Floors are in constant use, they wear quickly, and do not last forever.
Floors in classified areas are particularly prone to harboring microorganisms and foreign matter if they are not smooth or have a worn finish. In the classified areas, floors need to be inspected quarterly with a photo and documented assessment and correlation with EM trends. Turnarounds are excellent times to refinish floors and clean up the wear, tear, gouges, and dents from the drum drops and tri-clamp falls.
Another part of our facility inspection are the doors, door-seals, and rollup doors (only allowed in CNC areas). These items are the most notorious for collecting and retaining dirt, microbial matter, and all sorts of foreign matter. These need to be inspected and a yearly replacement program needs to be put in place.
Watch For Leaks With Low-Cost Monitoring
Another frequent and often catastrophic event is derived from the cascading leaks from the mechanical chases, interstitial spaces, and mezzanines.
These leaks are not noticed until they accumulate on the floor and overrun the doors, or they find a crack in the walls and drip a microbial “soup” into the process suite below, contaminating the production operation. Besides the routine inspection, a floor-mounted liquid sensor in all major unmonitored spaces is needed and should be connected to the plant’s building management system (BMS) to alarm if there is a puddle forming from a leak. In addition, installing video cameras in several of these key areas that reside over the production suites is a great risk-remediation practice.
With the facilities today covered by Wi-Fi, the sensors and the cameras do not need to be hard-wired to provide monitoring and observation. A popular Wi-Fi sensor for water costs $32 for three sensors via Amazon, and Wi-Fi cameras of varying quality can be bought at Best Buy.
Inspections Underlie The Whole Strategy
Inspections and the recording of inspections are the key to today’s maintenance issues and prevention of maintenance oversights that will cause disruptions to production. In addition, these observations and trends can prevent a series of EM excursions that force a “deviation” and subsequent investigation.
Sure, Drawings Are Expensive But Necessary
The last sin by maintenance departments that we have seen repeatedly is the lack of drawings. Sometimes, this is not the fault of the current maintenance management; however, as projects and periodic work commences over time, it is incumbent on the responsible parties to update the drawings for that effort. Over a longer period of time, the plant will be better documented.
In one facility, an engineering manager told me drawings are expensive and he keeps the engineering and construction costs down by not getting “as-built” or record drawings. This transgression was a short-lived fantasy, as within a month of that statement, a demo crew removing a wall next to a chase tore open a WFI line and flooded the entire floor of production suites.
In another example in 2020, a sterilizing tunnel was underperforming and the maintenance crew was struggling to find a “base case.” The only drawings we could find were from 1995, yet the tunnel had gone through several upgrades and instrument modifications. We have no idea how periodic “requalification” was performed.
Conclusion
We do not intend this to be a list of all the items on a maintenance work list. Our objective is to discuss the most chronic and recidivistic behaviors that we have seen, expose them, and hope if you have any of these shortcomings, you will remediate your actions and procedures.
Most maintenance managers look at their yearly budget and assume they just add a few percentages and continue doing (or not doing) what they always have. The better way is to start with a zero budget and build in realistic costs, looking at grade C, D, and CNC areas independently. Within each area, a priority is established focused on GMPs, product quality risks, EU/FDA requirements, safety, environment, and operability.
As a benchmark, each aseptic manufacturing facility should be spending 10% of the original capital cost on maintenance plus capital upgrades per year.
In conclusion, nothing lasts forever, and putting off some of these critical items or ignoring them will only cause a serious problem at some point in time. The key starting points are observation, photographing, documenting, and then taking positive corrective action.
About The Authors:
Herman F. Bozenhardt has 47 years of experience in pharmaceutical, biotechnology manufacturing, engineering, and compliance. He is a recognized expert in aseptic filling facilities and systems and has extensive experience in the manufacture of therapeutic biologicals and vaccines. His current consulting work focuses on aseptic systems, liposomes, biological manufacturing (BL-1, BL-2, BL-3), and automation/computer systems. He has a Bachelor of Science in chemical engineering and a Master of Science in system engineering, both from the Polytechnic Institute of Brooklyn (now NYU). He can be reached via email at hermanbozenhardt@gmail.com and on LinkedIn.
Erich H. Bozenhardt is the associate director of process engineering for Untied Therapeutics in Raleigh, NC. He has 18 years of experience in the biotechnology and aseptic processes and has led several biological manufacturing projects, including cell and gene therapies, mammalian cell culture, and novel delivery systems. He has a Bachelor of Science in chemical engineering and an MBA, both from the University of Delaware. He can be reached at via email at ebozenhardt@uthr.com and on LinkedIn.