Re-Engineering A Complex Process For FDA Compliance
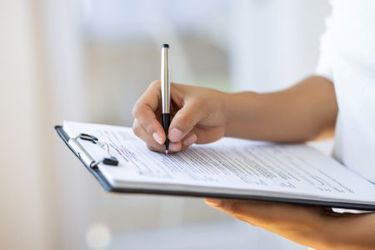
Precision Under Pressure: JHS's Swift Solution for FDA Compliance
In the fast-paced world of pharmaceutical development, where time is of the essence and lives hang in the balance, one company has demonstrated exceptional prowess in navigating complex regulatory landscapes while upholding the highest standards of quality and safety. This case study showcases Jubilant HollisterStier's innovative approach to re-engineering a COVID-19 liquid suspension vaccine production process for FDA compliance, highlighting their ability to overcome challenges and deliver results in record time.
The challenge presented was multifaceted. The company had acquired the tech transfer for a COVID-19 vaccine that was already approved for international use but not yet cleared for distribution in the United States. They faced the daunting task of developing a production process that met stringent FDA requirements without compromising the vaccine's sterility or homogeneity. What makes this case particularly impressive is that they managed to complete the tech transfer in less than half the time typically required for such a complex undertaking.
One of the most striking examples of the innovative approach employed was the development of an aseptic compounding process using only one R&D batch, rather than the several typically required. This strategy not only saved valuable time and resources but also demonstrated the company's confidence in their expertise and methodologies. By successfully maintaining sterility during bulk formulation and recirculation throughout the filling process, they ensured that each vial contained a homogeneous suspension of the vaccine. Another exemplary aspect of this case study is the collaboration between the technical services team and subject matter experts. Together, they created a design of experiment (DOE) in under five months, a feat that showcases the company's ability to work efficiently under pressure. This rapid development was made possible by leveraging prior experience with complex processing formulations and approved products, allowing them to expedite results without compromising quality.
The third notable example of their innovative approach was the validation strategy for engineering batches. By executing a non-sterile compounding-only batch first, followed by a filled, sterile engineering run, they maximized yield from a single compounding run. This approach not only saved the innovator time but also reduced expenses, demonstrating a commitment to efficiency and cost-effectiveness.
While these highlights provide a glimpse into the remarkable achievement, there's much more to discover about the process redesign, sterile handling techniques, and the specific challenges overcome. The full case study offers valuable insights into how sterility was maintained in an ISO 8 environment during compounding of the sterile bulk product and the extensive development work conducted to ensure the sterile handling and delivery of various excipients and active pharmaceutical ingredients.
For pharmaceutical professionals, regulatory affairs specialists, and anyone interested in innovative approaches to drug development and manufacturing, this case study provides a wealth of knowledge and inspiration. It demonstrates how agility and expertise can deliver nimble engineering solutions for a complex manufacturing process, potentially revolutionizing the way we approach vaccine production in the face of global health challenges. To gain a deeper understanding of this groundbreaking work and how FDA compliance was achieved on a compressed timeline, we encourage you to download the full case study. Discover the intricate details of how a robust, sterile transfer of material was accomplished, and learn about the step-by-step collaboration with the client that ensured mutual approval of each change. This case study offers invaluable lessons for those looking to optimize their own processes and stay ahead in the ever-evolving pharmaceutical landscape.
Don't miss this opportunity to learn from a real-world example of innovation in vaccine production. Download the full case study now to discover how Jubilant HollisterStier's expertise can inspire your approach to complex pharmaceutical challenges and potentially transform your production processes.
Get unlimited access to:
Enter your credentials below to log in. Not yet a member of Bioprocess Online? Subscribe today.