Product Development For An Oral Solid Dosage Using Continuous Manufacturing
By Kiernan LaMarche and Jessica Settimi, Thermo Fisher
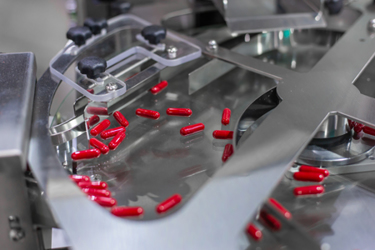
When bringing a new drug to market, product development is typically aligned with the clinical trial schedule; therefore, as the patient pool grows, so does the supply of drugs needed for the study. Phase I calls for a small trial formulation using the easiest and least expensive manufacturing methods for just getting the drug to the patient. Once you move into Phase II, a prototype batch process is often most cost effective, especially since most drug candidates do not make it past this stage.1 However, as clinical trial data begins to come in from Phase II, confidence in the product grows and important decisions about next steps need to be made. This is the best time to consider whether continuous manufacturing is a good fit for your product, as the formulation and process developed for Phase III are the final ones that will be used during commercial manufacturing.
Several small-scale studies should be completed to help determine whether continuous or batch manufacturing is the best fit for your product. These can include characterization work to understand the materials and how they interact with the process as well as proof of concept or range-finding studies on the manufacturing equipment. When continuous is a fit, the workflow can be reduced by as much as six months. This is due to the ability to compress the scale and timeline of the studies, making the process not only continuous but also more flexible.
By considering continuous manufacturing in development, manufacturers ensure they are creating the most optimal path over the life cycle of their program that includes quality, flexibility, and economic benefits.
Get unlimited access to:
Enter your credentials below to log in. Not yet a member of Bioprocess Online? Subscribe today.