Pigeons In The Plant: 10 Real-Life Pharma Facility Blunders (And How To Avoid Them)
By Herman F. Bozenhardt and Erich H. Bozenhardt
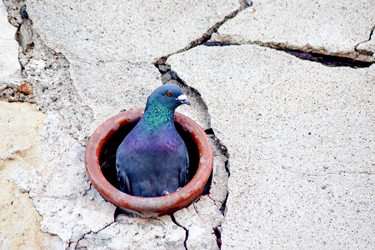
In our many years in the pharmaceutical business we have witnessed the introduction of revolutionary therapeutic products and designed and built plants with the latest process technology and in doing so, saved lives. However, we live in the world of physical plants, manufacturing production, and the humans that run these facilities. As we have discussed in our many articles, there are many ways to tackle design, engineering, building, and production, and each plant has its own methods and culture. However, there are situations we have come across where we really scratch our heads and say, “What did they just do, and what were they thinking?”
This article describes a series of events or activities that we have seen and, while they are amusing or baffling, they reveal the flaws in our industry. As an industry, we need solid technical capability, rational thinking, understanding of GMPs, situational awareness, and, more often, common sense. These mini case studies are all true and have occurred, as bizarre as it may seem, and each has a message for the industry.
The Trained GMP Mice Of Italy
A large filling facility in Italy was undergoing an internal audit from a facility and equipment standpoint. The operations and QA departments were escorting the audit team along the pathway from the CNC area through the locker rooms into the various airlocks and narrating the compliance program of unidirectional flow. At the point where the auditors entered the airlock going from the Grade D corridor into the Grade C airlock/gowning room, a 4-inch pipe was observed penetrating the wall perpendicular to the gowning room door. The pipe went from the Grade D area through the exterior wall of the building to connect to some utility. The problem was that daylight was visible around the penetration of the external wall. Upon closer inspection, the cinderblock around the pipe was broken up, with varying gaps of one-quarter inch to nearly three-quarter inches. No attempt to caulk, seal, or close the gap had been made, and it was obvious vermin could easily travel from the building exterior across the gap into the Grade D space. When asked about the gap and the infiltration of rodents, the plant escort told the auditors, “There is a mouse trap outside by the pipe and another mouse trap here on the floor within a few centimeters from the gap.” To which the auditor said, “I understand; your mice here are trained to enter the traps because of their training.” The escort only smiled.
The lesson here is to really scrutinize your facility and take care if you have any external penetrations and check your pest control at all entrances. The second lesson is to have a plant escort with enough savvy to just note that it is a correctable item and it will be taken care of.
A friend of ours also told us of a black racer snake slithering around an OSD plant in eastern North Carolina. When asked what they did, the response was they eventually caught it, but not to worry, “Snakes are clean animals”!
cGMP Broom Closet
A consumer liquids, tablets, and capsule facility on the U.S. East Coast had received a series of observations on its computer systems and was starting to begin the remediation. As the reviewer and planner, we began looking at the hardware, software, and IO. To say computer validation concepts were foreign to this firm would be an understatement. The one aspect that was frustrating was the lack of documentation on the IO, marshaling panels, cabling, and plant-wide network. We were told it was all contained in the IO racks and we would be surprised when we saw it. The IO rack was something that looked closer in appearance to a high school gym locker that had no lock or restrictive device. When we opened the rack, an industrial-size broom fell out and hit one of us in the head, then the loose, untied signal wires billowed out and over the floor. There was no panel-mounted documentation in the cabinet and the wires and cables had not been documented. Suffice it to say the lines had to be re-run out to ID and document them.
The lesson in this case is that often folks in the business leave “well enough alone.” That is the wrong attitude; maintenance, good housekeeping, and documentation matter seriously. IO racks are no places for brooms.
Why Are My Clean Dry Air Filters Clogged?
One large aseptic filling plant on the U.S. East Coast was in a winter shutdown and was having the carbon filter banks on the air compression systems changed out. This was a busy time for the plant and the local vendor was given the task of making the changeout without any plant supervision or escort. This vendor had an untrained installer who struggled to get the filter in and thought that putting it in backward might be the solution. Somehow, with a few strikes of a hammer, they did it. When the air was turned on, the entire clean dry air system was flooded with carbon dust that blew into all the POU filters in manufacturing. It took the plant two to three weeks to purge the system during an extension of the shutdown.
Never let even the most experienced external vendor work on your plant without observation, and make sure everybody knows what the job is and how it is supposed to get done.
Sorry, I Forgot To Close The Sample Valve
Taking a sample of WFI (water for injection) from a known sample tap with a local floor drain below seems to be simple and common task, right? In another East Coast aseptic facility, an operator was taking the WFI sample from the prescribed drop and was following the procedure to purge the line first. All we really know is that during the purge, the individual was distracted with a phone call. They left the line wide open, never took the sample, and the WFI continued to flow until it overwhelmed the drain. The WFI flowed all over the utility area, found a pathway to the filling suites below, and flooded the ceiling, eventually hitting all the HEPA filters.
We talk about distractions and their consequences; this distraction cost that fill room a month of production, not to mention the cost of a lot of HEPA filters.
Pigeons In The Plant
A large-scale Midwestern API plant was concerned with the changeover of the staffing of the local FDA office and asked for a plant compliance assessment. The auditors traveled through the plant and came up with a number of observations that were clearly compliance concerns. When they viewed the “sterile subdivision and sample area” they were shocked to see a stainless-steel table area with a laminar flow hood above it, but completely open to a multi-bay reactor train. Next to this table was an old, rusted closed jalousie (crank out) window. When asked how they controlled the environment around this area, the operators responded, “We don’t do anything unless it is too hot, then we open the window for some fresh air.” After that statement sunk in, they were asked why there were splatters of white API over certain vessel domes and piping sections. They were then informed that the splatters were not API; they were pigeon droppings! How did the pigeons get in the API plant? It was through the jalousie windows, which had no screens.
That plant was shut down shortly thereafter with a change of ownership.
Gowning Up To Go To The cGMP Lawn
There is something magical about WFI that makes folks do strange things. One aseptic plant in the U.S. had grown up and expanded many times over a 30-year history and failed to provide an adequate sample drop for one end of their WFI loop. To our auditing amazement, we saw the WFI loop routed outside the building and then back in for use. That is not the best way to route pipe, but the owner argued that space was tight. We then observed a sample port and valve outside connected to this pipe and immediately told the owner they needed to dismantle this in case somebody mistakenly opened it. We assumed that the port was a mistake until we saw an operator gown up (bunny suit, head piece, mask, gloves, boots, etc.) completely inside, walk outside onto the exterior building lawn, and draw a WFI sample into the sample bottle. When asked what he was doing and why, he referred us to the sterile gowning SOP and the WFI sampling procedure.
SOPs are great, but common sense is better. The operator is not to blame; some manager told him to do this and, as long as he follows the SOPs, it is all good. We often blame operators for problems and call deviations human error. The vast majority of times, the manager actually tells the operators to do something ridiculous or impossible.
More Brooms And Dust Pans
In this instance, another East Coast aseptic fill plant’s operators were compounding a new parenteral batch and had drawn the WFI and put the excipients and preservatives in the compounding tank. The heavy container of API was next, as the API was to be slowly added manually into the open port on the vessel. The vessel was not being held securely, and the entire container (several kgs) spilled out onto the walking platform. A key point in GMP training is that incidents such as this require notification, API disposal, and issuing new product, assuming the operators can execute the compounding within the time frame. Not these folks! They acquired a broom and plastic dustpan and made the cleanup and compounding one single operation as they swept up the API and put it into the vessel. When interviewed after the incident, the operators’ and their manager’s justification was that it would have been sterility filtered at the next step anyway.
Clearly, the concept of patient safety, quality, and risk assessment never occurred to them. The batch was discarded and GMP training was reinstituted.
Sure, We Have Lightning Protection
A large API plant in the Northeastern U.S. had been in operation for about 30 years and was going through a major control system upgrade. One of the key parts of the upgrade was to review and assure the plant’s grounding systems and lightning protection were in sound condition. One of our electrical engineers audited the grounding and went to the roof to inspect the lightning protection. Surprisingly, he found a well laid out series of spike lighting rods circling the building’s perimeter roof, all connected by heavy steel cabling. But he was baffled as he tried to find the grounding connection to an earthen source. Finally, he discovered the steel cable had a thin bell wire wrapped around it and he saw the bell wire was strung along the roof and into a cabinet — the PLC controller for the HVAC. Lo and behold, the bell wire was connected to the grounding terminal of the PLC.
That will assure that if lighting were to hit the rods, it would carry the current to the PLC and most likely fry the PLC and possibly the AHU’s drive. Lightning rods need to be connected to a large earthen ground.
Is The Cleaning Crew Really Cleaning?
When traveling to a Western European plant recently we audited its biological production facility, which was struggling with bioburden during the start-up. We spent a considerable amount of time searching and analyzing potential contamination paths, practices, and procedures. While we found several minor areas, we could not identify the “smoking gun.” But we did see the situation progressively getting worse over time and were perplexed. Then, at lunch, as we were sitting in the cafeteria discussing the problem, I noticed a large group of folks in plant uniforms directly behind us speaking in a Slavic language and using very foul language. Since English was the dominant language in the plant, they were safe speaking about how they hated their jobs, intended not perform their duties, and were looking to find places to hide from their bosses. I grew up in a household that spoke that language and studied it in school. I was astounded, and I revealed my translation to the operations management and asked who those folks were. The answer was they were the “outsourced cleaning crew” that worked at night.
In the end, they in fact did very little cleaning and were able to get away with it since the plant operations folks did nothing to audit or observe their work. They were released and the cleaning was “insourced” quickly. Within a biotech and pharmaceutical plant, cleaning and sanitization are critical to maintaining the product quality. It is too important not to supervise, audit, manage, and EM check.
Does The Night Shift Read The Same SOPs As The Day Shift?
The final story in this installment comes from a Southeastern U.S. aseptic fill facility. During a project to upgrade its filling capability, we were asked to observe the line operation and the line changeover. Early during the day shift we were escorted to the observation window to watch while a meticulous team changed a filling line over from one product presentation to another. They performed a symphony of careful cleaning, sanitization, line clearance, painstaking setup, and documentation. We were impressed.
The next day, we changed into greens and worked later into the evening to gather our data and travel freely inside some of the classified areas. By the time we completed our tasks, we decided to observe the same line (as the previous day) to gather a benchmark on changeover time from the evening shift, since they had finished and were changing over to a new batch and product presentation. We went to the same observation window (in greens) to watch the night crew change the line. To our horror, we saw sanitizing solution being splattered all over the room, only partial cleaning, and poor behavior topped off with one operator sweeping the broken glass near the capper under the filling machine, rather than picking it up.
Clearly, either the night crew had not read the same SOPs as the day crew, or there was a keen awareness that behavior is variable based on the audience. This emphasizes that the presence of management supervision and QA are necessary on all operating shifts.
As a summary of the above, we need to make sure operators, engineers, and suppliers are trained, tested, and retrained to work in a GMP environment. We cannot become complacent and let our tasks become so routine that we are oblivious or tolerant of poor behavior. Self-audit, QA, and reinforcement of the GMPs is an evergreen activity.
Do you have any good real-life GMP horror (or comedy) stories to add to the list? Please share them in the Comments section below. (Please do not include names of companies or individuals — the goal is to amuse and inform, not to defame.)
About The Authors:
Herman Bozenhardt has 43 years of experience in pharmaceutical, biotechnology, and medical device manufacturing, engineering, and compliance. He is a recognized expert in the area of aseptic filling facilities and systems and has extensive experience in the manufacture of therapeutic biologicals and vaccines. His current consulting work focuses on the areas of aseptic systems, biological manufacturing, and automation/computer systems. He has a B.S. in chemical engineering and an M.S. in system engineering, both from the Polytechnic Institute of Brooklyn. He can be reached via email at hermanbozenhardt@gmail.com and on LinkedIn.
Erich Bozenhardt, PE, is the process manager for IPS-Integrated Project Services’ process group in Raleigh, NC. He has 13 years of experience in the biotechnology and aseptic processing business and has led several biological manufacturing projects, including cell therapies, mammalian cell culture, and novel delivery systems. He has a B.S. in chemical engineering and an MBA, both from the University of Delaware. He can be reached at via email at ebozenhardt@ipsdb.com and on LinkedIn.