Optimizing CAPA For FDA Recall Success: A Roadmap For Life Sciences Quality Professionals
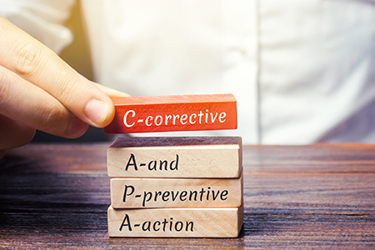
A robust Corrective Action/Preventive Action (CAPA) process is essential for life sciences companies to address quality issues, prevent regulatory citations, and avoid costly product recalls. CAPA provides a systematic framework to identify, investigate, and resolve quality events, meeting regulatory requirements like FDA 21 CFR 820.100 for medical devices and ICH Q10 for pharmaceuticals. However, many organizations struggle with inadequate root cause analysis, poor documentation, ineffective action plans, and insufficient oversight, leading to recurring quality issues and compliance risks.
To optimize CAPA, companies should establish standardized procedures, conduct thorough root cause analyses, and implement risk-based approaches to prioritize critical issues. Verification of corrective actions and effectiveness checks ensure long-term problem resolution. Leveraging technology, such as an electronic quality management system (eQMS), can streamline CAPA workflows, improve visibility, and enhance regulatory compliance.
MasterControl's Quality Excellence solution supports CAPA optimization with configurable workflows, risk assessment tools, and integration with other quality processes. Its advanced analytics, automated task management, and real-time oversight enable life sciences companies to proactively manage quality issues. With a fully integrated and technology-driven CAPA system, organizations can minimize risks, ensure consistent product quality, and maintain a competitive edge.
Get unlimited access to:
Enter your credentials below to log in. Not yet a member of Bioprocess Online? Subscribe today.