Next-Generation Monitoring Of Bioprocessing To Enable Smart Data Management And Analysis
By Hemant Garg, Product Manager, Analytics
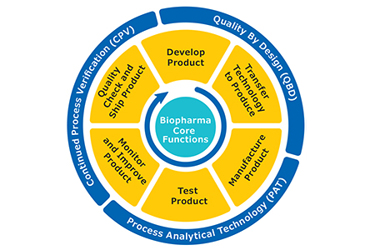
The bioprocess lifecycle for any therapeutic protein includes a complex series of upstream and downstream activities starting with drug development followed by manufacturing, quality release and finally shipping the drug to the market. These activities must adhere to strict regulatory guidelines and are designed, monitored and optimized through the use of several approaches including quality by design (QbD), process analytical technology (PAT) and continued process verification (CPV).
Every step of the process and each unit operation generate a massive amount of data at an incredibly fast rate. There is always uncertainty associated with the manufacturing batches due to the underlying biological processes; as such, it is paramount to understand these datasets to enable better decision-making. Adding to the challenge presented by the volume and velocity of the data is that it is typically stored in multiple, disparate systems. These disparate systems, which may not effectively communicate with each other, contribute to the difficulty in leveraging the data to inform and guide decision-making.
The enormous amount of data being housed in separate locations can present significant obstacles during investigations and quality deviation closures. In these cases, unified data sets must first be created, drawing input from multiple departments to pinpoint the root cause of the problem. In many cases, data are not readily available; some may exist only as paper-based, manual reports while others are housed in separate electronic systems. Data consolidation thus requires an enormous amount of time and labor, invariably slowing the manufacturing process and progress of the drug to the market and, ultimately, to patients in need.
Not surprisingly, regulatory agencies have put forth guidelines on bioprocess monitoring and data collection to ensure high product quality and process consistency. For example, the US FDA clearly states in its Process Validation: General Principles and Practices1 – Stage 3 – Continued Process Verification – ensuring that the process remains in a state of control assures quality and is an integral part of process validation. Regulators also emphasize that drug sponsors must have a system for detecting unplanned deviation in routine processes.
Given the need to collect and fluidly handle massive amounts of data being generated with tremendous velocity, a new approach to data management is essential.
Get unlimited access to:
Enter your credentials below to log in. Not yet a member of Bioprocess Online? Subscribe today.