#MeToo & Time's Up — Parallels To Reporting Of GMP Compliance Issues
By Joanna Gallant, owner/president, Joanna Gallant Training Associates, LLC
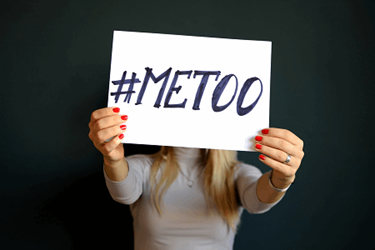
Over the last several months, we’ve heard of far too many incidents of sexual harassment or worse coming to light. In the event you’re not familiar with the terms, #MeToo is a hashtag used in social media to demonstrate the prevalence of sexual assault and harassment. It went viral as victims started to post their own stories, showing how widespread the problem actually is. Founded by Hollywood celebrities in response to several high-profile sexual harassment and assault cases in the entertainment industry, the Time’s Up initiative champions change in these behaviors and works to establish fair treatment for all.
Unfortunately, elements in these stories remind me of situations I’ve personally experienced in the GMP world.
(I don’t intend this article to comment on or discuss harassment allegations; I’m only drawing parallels from what I’ve observed between these two environments.)
Parallel #1: Taking Too Long For One Voice To Be Heard
One element I see in common is that once one person speaks up and is finally heard, several others follow with similar stories. These additional people either weren’t heard at first or broke their silence because someone else did successfully.
This reminds me of when data falsification and poor record-keeping practices were identified in a production/QC process. Once notified of the problem, the production and quality leadership shut down operations. They needed to investigate to determine the breadth of the problem: how many products and lots it had impacted and who was involved in the activities.
During that time, training was tasked with providing data integrity and good documentation practices training to explain why the activities were inappropriate in a GMP environment and to reset management’s quality expectations with personnel.
I wasn’t the trainer, but I observed the session, as I didn’t want the trainer to face a difficult situation alone. What I heard was disturbing, and I’ve never forgotten it.
First, people became very upset with training for telling them what they already knew was wrong. Then, several said they had previously identified these issues and reported them to appropriate personnel (their management chain or site quality) but were either not listened to or told to just ignore it or, worse, go along with what was happening.
I heard anger from the people who talked about how they had tried to get their concerns addressed and had been ignored. Others feared they would be identified as complicit in the problem when they had tried to get it addressed and couldn’t. And yet others expressed fear, anger, confusion, and frustration at having been directed to do the wrong things, leaving them feeling powerless or trapped. Frustrated at not being heard and not being able to change the situation, they eventually stopped raising the issues, believing no one cared.
What made this time different — why the concern was heard this time — was because a new QC analyst reported the problem they found to a new QC manager. That manager recognized it as a problem and raised the concerns to other new leaders in the facility, who finally took appropriate action.
Ultimately, it was determined that not only the lower-level personnel performing the actual falsification were at fault, but the supervisors and management staff who had been told of these situations and did not respond appropriately were also at fault. All were held accountable.
In another situation, which leads into Common Element #2, an individual felt there was a compliance problem in their workgroup and raised it to their line management, but felt line management’s response of, “It’s fine,” indicated the concern wasn't being taken seriously. The person spoke to me after a training session, asking questions about GMP expectations and how things should be done. During our conversation, it became clear that they thought a compliance issue wasn’t being addressed internally. Feeling internal reporting options weren’t working, the person was trying to decide whether to approach the FDA as a whistleblower and report the company and situation.
Parallel #2: Enabling Behavior Through Unclear Expectations Or Failure To Hold Personnel Accountable
Another element I’ve seen in common is the behavior was either: (1) an egregious act which the person should have known was unacceptable, but they did it anyway, with no repercussions at the time, or (2) a lack of understanding of what constitutes unacceptable behavior and/or a lack of common understanding between the involved parties, which doesn’t surface until after the situation occurs and one party has been hurt.
To continue the story of the potential whistleblower, after our conversation, I brought the concern to my management, and we approached quality leadership. After an audit of the area was performed, it was reported back that the area was in compliance.
Ultimately, the situation resulted from a difference in understanding between the person and their management of how the regulatory expectations should be interpreted. Resolving the concern only required cleanup of sloppy housekeeping practices and getting the person and their management on the same page.
In this situation, both sides were trying to do the right thing but went wrong by not taking the time to have an appropriate discussion about the concern, which made the situation more problematic than necessary. Had they taken the time to discuss and maybe consult with the quality group on the practices in question, the situation would have resulted in alignment on the expectation and interpretation, versus nearly becoming a whistleblower situation with much more significant repercussions.
Comparatively, the behaviors in the falsification example were egregious failures. Anyone with an ounce of integrity and GMP experience should be well aware that it isn’t acceptable to falsify compliance information, and yet experienced operators did it anyway. Similarly, the managers and supervisors who didn't react appropriately to the reports of falsification activities failed outright in executing their responsibilities by not investigating a reported compliance problem or by enabling incorrect execution of activities that impact product quality.
Parallel #3: Abuse Of Trust/Power/Position
Finally, many of the incidents have in common a person in a position of power, prominence, or a role in which they were trusted to behave appropriately — which they then abused, thinking they could (or would) get away with it.
From the falsification example, the involved individuals were trusted by the company to perform tasks correctly, and they abused that trust. Further, the personnel who reported concerns had their trust abused when no one acted on the concerns or they were directed to go along with the bad behavior. And those who allowed the situations to occur abused their positions, placing what they wanted ahead of the company’s commitments to the FDA and to the patients they served.
In the case of the potential whistleblower, trust between the worker and their management has eroded due to failing to respond appropriately to a concern. It could also constitute an abuse of power if it was motivated by line management thinking they don’t need to explain themselves or their operation to a subordinate. In reality, when an inconsistency or lack of understanding is identified, it clearly indicates a need to better educate people on operations or to improve a process.
Another situation that falls into abuse of trust/position are those who use intimidation — including pressure — to get what they want. The person being pressured recognizes it’s happening but may not know how to address or defuse the situation, especially if it’s coming from their management or a higher up in the organization.
Several times I’ve seen two people disagree on what should be done or how to do something — and one person explains why they’re right by saying the other person “doesn’t know their GMPs” or “isn’t following the GMPs.” The second person usually doesn’t have a comeback (few people can identify the specific GMP requirement driving the activity they’re performing) and finds themselves bullied into doing whatever the other person wants.
Another “pressure application” situation came from a production operator who approached me after a training session to discuss a concern resulting from a group meeting with their manager. The manager told the group to figure out how to double production without adding personnel or equipment and to only involve him if they couldn’t make it happen. Otherwise, he didn’t want to know what they were doing. As a result, the operator felt their manager was trying to pressure the group to cut corners and take shortcuts, but without actually directing them to do so. By not explicitly directing the group to violate compliance and distancing himself from the activities, the operator believed the manager was setting up people in the group to take the fall when noncompliant activities came to light.
Another example occurred when a QC manager complained to me that the learning management system (LMS) was malfunctioning, because his QC group’s training completion metric should have been at 100 percent. As the LMS owner, I looked into the situation and discovered all of the training requirements for QC had been altered a few days before. The LMS audit trail showed the analyst who was the LMS user for the group had made all the changes. So I went to speak to the analyst. When I asked about what I saw in the LMS and what led to the changes being made, he became very nervous and eventually told me a disturbing story.
According to the analyst, the QC manager instructed him to sign into the LMS and remove the retraining requirement and the due date from any LMS training item assigned to QC. The QC manager demonstrated what he wanted done by changing information under the analyst's username in the LMS, and then had the analyst make the same changes to the remaining items while he watched.
(Making these changes meant no training would ever appear overdue and no procedure would require retraining when it was revised, effectively enabling all QC personnel to always be 100 percent complete on their training. This meant the QC manager's metrics would always be stellar — or so he thought. …)
When the analyst questioned the appropriateness of the changes and asked to check with me about it, the QC manager said that since the changes had already been made, the audit trail led back to the analyst. So, if the activity wasn't aboveboard, the analyst would be the one punished for it, so it was best to just keep it between the two of them.
What’s The Point Of All This?
Obviously, both the harassment and compliance failure situations highlight exceptionally bad behavior for which there is no good excuse and no positive outcome for anyone involved.
The GMP regulations have always encapsulated a behavioral code of ethics — honesty, integrity, transparency, and traceability in the operations, with an education process for what’s expected. So why is it so hard for people to uphold this code?
The quote, “With great power comes great responsibility” (attributed to both Voltaire and Stan Lee), seems exceptionally fitting in this situation. We in the GMP industries wield great power — our actions have the power to positively or negatively impact the lives of the patients who use the products we manufacture. For those of us in management roles, we wield similar power over the quality of our personnel’s daily lives. And, yet, we don’t always live up to our responsibility.
So, what do we need to do to ensure we can and do live up to it?
First, we need to set expectations and be willing to hold all personnel to them — including ourselves.
Then, we need to educate our people on why they’re doing what they’re doing and the impact of not doing it correctly. That includes educating our management staff on what their jobs really include — and it’s much more than simply meeting quotas or metrics.
We need to recognize and encourage people to do the right thing by asking questions and raising issues they think are problems. When they do, we need to take the time to listen and react appropriately — either by explaining and educating the person or acting on the information they’ve provided.
We also need to establish reporting processes for personnel to use to raise compliance concerns. In the event the management chain breaks down, there must be a way for issues to be heard and acted upon.
But mostly, we each need to live the standard ourselves. Model what you want to see, because someone may be watching and taking their behavioral cues from you — no matter who or what level you are in the company. If a new person wants to fit into the company, they watch how the people around them behave. When someone wants to be a valuable employee, they model what the star players do. When a new manager wants to succeed, they watch to see what the management team values and does. Set a good example yourself, and others will follow. Even if they don’t, you’ll still be able to look yourself in the mirror every day.
#MeToo and Time’s Up are spotlighting illegal, unethical, improper, and undesirable behaviors and showing that well-established people and businesses can be toppled by their actions.
Illegal, unethical, improper, and undesirable behavior exists in the GMP world, too (simply read recent warning letters on data integrity if you need evidence), and we’ve been warned as well. Fix what you can, and root out the bad players who won’t clean up their acts — before it’s too late. Because recovering from some situations is almost impossible if it goes too far.
About The Author:
Joanna Gallant is an experienced, solutions-driven quality and training professional who has spent the last 25 years in pharmaceutical, biotechnology, tissue culture, and medical device development and manufacturing environments. Over her career, she has provided regulatory, technical, skill, and management development training support to all operations functions, as well as IT, R&D, customer service, and senior management. Now, as a consultant, she works with clients to design and deliver custom training and build/remediate training systems, including in support of regulatory audit observations and commitments.
Joanna has been a GMP TEA member since 2001, and now serves on the Board of Directors as an advisor. She is one of the founders of the Biomanufacturing Certificate Program at Worcester Polytechnic Institute, and became an Adjunct Professor at the Boston University School of Medicine's Biotechnology degree program in 2011.
You can contact Joanna at Joanna@JGTA.net or connect with her on LinkedIn.