Manifolding For Scale-Up, Safety, And Speed
By Chris Hofmann and Ian Burdick, Charter Medical
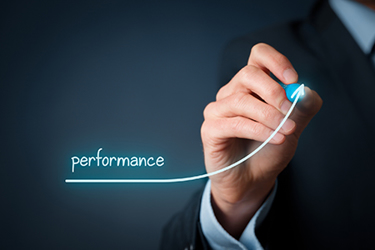
Although simple to execute, filling individual single-use bags one at a time requires a lot of repetition: multiple operators fill one bag at a time, and every few hours work may be interrupted by line clearances, sampling, and other mandated safety measures. In addition to being time-consuming, this process involves multiple connections and touchpoints to these high-value products. Each connection introduces a contamination risk, and any non-uniformity in those junctions can damage cells passing through. Further, the process is not conducive to effective scale-up for commercialization, since highly skilled personnel are needed to complete each connection, and cleanroom space is both limited and expensive to expand.
A manifold — a collection of sterilized, single-use bags and components connected along a central line called a spine — allows different container types and sizes for storage or sampling purposes to be connected, depending on the user’s needs. Thus, the manifold spine allows the users to transfer a large batch of liquids to many bags at once, reducing time, process complexity and product loss from contamination.
As a product scales from benchtop to commercialization, manifolds provide the flexibility to easily transition from small to large production batches. Manifold designs can range from simple to complex and can accommodate any number of final bags based on available space, process parameters, and number of operators.
Get unlimited access to:
Enter your credentials below to log in. Not yet a member of Bioprocess Online? Subscribe today.