2 (Major) Impediments To Faster Biopharmaceutical Product Development
By Mark F. Witcher, Ph.D., biopharma operations subject matter expert
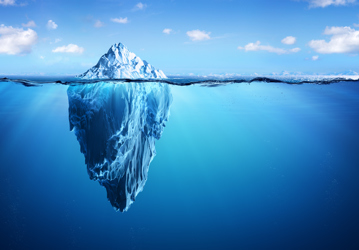
Besides the obvious “need for speed” during a pandemic, the demands of the 21st century require rapid development and commercialization of biopharmaceutical products, including vaccines and directed antibodies. Days count both in terms of cost and lives saved, even during normal times, for important therapeutics. The basic principle of speed to market applies to every biopharmaceutical product, without exception. The world’s tolerance for slow and cumbersome performance in general is decreasing. As pharmaceutical products have become more complex, many companies have become bogged down in accomplishing their primary mission of launching new products by complex regulatory requirements, convoluted management approaches, and inefficient resources and methods that add time and cost to moving new products from research to the patients.
Based on 50 years of experience, this article discusses two issues that significantly hinder biopharmaceutical companies, both large and small, from rapidly developing new products. The first is inefficient management practices that distract and delay an organization from its goals. The second is poor development methods and resources that consume extra time and add organizational overhead. Both also add significant risks to the successful development of new products.1
Effective Planning And Managing
Successful product development starts with a realization that every hour counts. The hours add up to days and even months very quickly. Each hour should be valued as important and can be viewed as an hour of an untreated patient suffering in an ICU, separated from their family, just hoping and praying to get better. What are the methods by which this hour can be saved?
Many of today’s managers seem to be stuck on a path of plan, manage, plan, manage until failure. Project planning can take on an all-consuming life of its own. However, progress is made by “doing,” not planning and managing. Planning and managing are important, but it does not take much of either to support a lot of doing. Doing takes courage. Managing and planning are safe, but doing is risky in the short term. Sometimes it feels like managers continue to plan while hoping the problems will solve themselves. Frequently, it is far better to run the wrong experiment and learn than it is to excessively plan for the right experiment, especially if you never get to it.
The most effective plans are the short ones. A project should have a short strategic plan that describes the sequence of major milestones with short tactical plans covering the paths from one milestone to another. The tactical plan to reach the next milestone should be the point of emphasis. Since no plan survives its execution, focus on doing what needs to be done between the current and the next milestone to achieve short-term success. Start doing the next step in the plan now and adjust the tactical plan as needed by fighting through the problems as they arise. The most important activities are always the ones that everyone is working on right now.
Tactical plans are essential and should reflect a well-qualified doer’s approach to solving the problem. The most effective plans are assembled with strong input from those involved in and responsible for doing the work. A tactical plan’s logical sequence of activities should be assembled using a consensus of those closest to the effort, with assistance and guidance of planners and supervisors developed during a small meeting of stakeholders.
Meetings are a leading cause of organizational rigor mortis and product/project deaths. When you are meeting, you are managing, not doing. A meeting should be viewed as consuming a company’s most important assets: time, money, and especially people. Simple concepts and questions can guide the use of meetings.
Does everyone in the meeting need to be there and are they contributing?
The fewer people in a meeting, the better. The urgent two-person meeting is the most effective. The more people, the harder and longer it takes to schedule. Think in terms of leaving the maximum number of people working on what they need to accomplish for the organization to reach the next milestone. Frequent small, short meetings can be highly effective. Many small meetings can be far more productive than one large meeting.
If you have a problem, how can you get it resolved as quickly as possible?
Management by walking around works. If you have a problem, get up and start the solution now, not later. Replace the large meeting with building trust in the organization by walking around and keeping every stakeholder in the problem informed and involved. Consensus can often best be built through multiple sequential interactions and, when necessary, horse trading within one-on-one conversations. The interpersonal dynamics between very small meetings and larger groups is fundamentally different.
Frequent small meetings can also be extremely useful in finding problems before they find you. Interaction builds trust and effective relationships. Do not hesitate to initiate other small meetings to work on a solution. Once a solution is started, get out of the meeting unless you are part of the solution, and get back to work on your part of the tactical plan. Small meetings also do not need agendas and minutes. For small meetings, agendas are obvious. Write down only what needs to be documented and transmitted. Few things are more worthless than minutes from large meetings that no one will ever read.
The regularly scheduled weekly meeting has been the death of many projects and products. Regularly scheduled meetings delay problem solving and interfere with scheduling important small meetings and interactions, not to mention delaying and fragmenting many other important ongoing activities. If you need to meet, doing it as soon as possible while disrupting the organization as little as possible is critical to saving hours that rapidly turn into days.
Efficient Methods And Resources
Having the right tools and methods is critical to success, especially when things need to be done quickly and efficiently. The first thing a good mechanic will teach an apprentice is to not tighten a bolt with a pair of pliers. Using the wrong tools and methods can lead to a variety of problems and needless risks that could delay the effort.
The first important method is not using risky manufacturing practices. What is a risky manufacturing practice? A bad practice is one that could fail due to a realized risk, leaving you with bad material and causing significant delays from poor data or information. The success of any product or development project depends on making sure that all material, from cell banks to preclinical to commercial product, is what it should be. Achieving that goal requires using a process-based risk mentality to understand the threats to a process that might result in an output failure or risk consequence. Everything from making a cell bank and running an experiment to making commercial product uses a series of processes that include people, equipment, and procedures. How could threats to each process result in that process not achieving its desired goal? A risk-based mentality, based on understanding the flow of threats through structured risk processes that may result in failures, supports moving efficiently and quickly through the product development cycle by minimizing problems and realized failures.2,3
The next method is to view product development in terms of validating while developing, rather than developing, then characterizing, and then validating. Development and validation have the same objective and should be largely accomplished simultaneously using a good engineering approach that generates the necessary validation documentation as part of the development activities. The chance of success is maximized by strongly emphasizing the process design stage to build not only the processes required but also to carefully plan the testing and operational stages of the product’s manufacturing life cycle. Only by using the design stage to anticipate, plan, and manage future problems can the risks and timeline of product development be greatly reduced.4
Both efficiency and speed can be gained by using basic principles to build fundamentally sound processes and systems. The pharmaceutical industry is currently focused on using a secondary objective, compliance to regulatory standards, as a design criterion for manufacturing high-quality products. The industry must switch to using methods based on universal good engineering principles for building all the processes necessary to rapidly, efficiently, and consistently achieve high levels of product quality.4,5
The final method is to think in terms of eliminating tech transfer. Transferring a product between two organizations, regardless of their locations internally or externally, will add time and risks. Seamless continuous product development requires continuity in both the organization and facilities used to support product development, testing, and manufacturing, from cell bank development through launching the product to the patients. Only facilities that have the flexibility to quickly deal with the wide variety of manufacturing challenges, including process formats, scales, and capacities, can quickly and efficiently handle the high product uncertainty inherent in almost all biopharmaceutical products.6
Summary
Biopharmaceutical product development in the 21st century will be very unforgiving, requiring rapid execution of the necessary activities to quickly reach important milestones. Consumers, sponsors, and investors cannot afford and will not tolerate slow product development and commercialization. Only management methods focused on efficiently managing effective human and capital assets that rapidly launch new products will prosper.
References:
- Witcher, M. F., “Phase III Clinical Trials – Ever Wonder Why Some Products Unexpectedly Fail? ISPE iSpeak Blog Pharmaceutical Engineering, Aug. 7, 2019. https://ispe.org/pharmaceutical-engineering/ispeak/phase-iii-clinical-trials-ever-wonder-why-some-products-unexpectedly-fail
- Witcher MF. Analyzing and managing biopharmaceutical risks by building a system risk structure (SRS) for modeling the flow of threats through a network of manufacturing processes. BioProcess J, 2017; 16. https://doi.org/10.12665/J16OA.Witcher J160
- Witcher MF. Estimating the uncertainty of structured pharmaceutical development and manufacturing process execution risks using a prospective causal risk model (PCRM). BioProcess J, 2019; 18. https://doi.org/10.12665/J18OA.Witcher
- Witcher MF. Integrating development tools into the process validation lifecycle to achieve six sigma pharmaceutical quality. BioProcess J, 2018; 17. https://doi.org/10.12665/J17OA.Witcher.0416
- Witcher, M. F., A Straightforward, Risk-Based Approach to Better Quality Management System Design, Pharmaceuticalonline.com, March 18, 2020. https://www.pharmaceuticalonline.com/doc/a-straightforward-risk-based-approach-to-better-quality-management-system-design-0001
- Witcher, M. F. “How FDA’s 21st Century Goals can be realized by using a Multi-purpose Manufacturing Facility,” Pharmaceutical Technology, 2018. http://www.pharmtech.com/how-fda-s-21st-century-goals-can-be-realized-using-multi-purpose-manufacturing-facility-0?pageID=2
About The Author:
Mark F. Witcher, Ph.D., has over 35 years of experience in biopharmaceuticals. He currently consults with a few select companies. Previously, he worked for several engineering companies on feasibility and conceptual design studies for advanced biopharmaceutical manufacturing facilities. Witcher was an independent consultant in the biopharmaceutical industry for 15 years on operational issues related to: product and process development, strategic business development, clinical and commercial manufacturing, tech transfer, and facility design. He also taught courses on process validation for ISPE. He was previously the SVP of manufacturing operations for Covance Biotechnology Services, where he was responsible for the design, construction, start-up, and operation of their $50-million contract manufacturing facility. Prior to joining Covance, Witcher was VP of manufacturing at Amgen. You can reach him at witchermf@aol.com or on LinkedIn.