Lilly's Calculated Approach To Upgrade Trade-Offs
A conversation with Eamonn Warren, Eli Lilly and Company
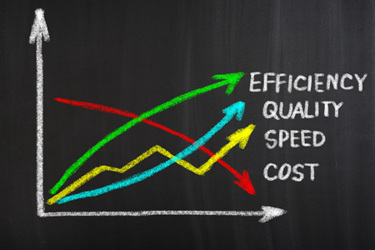
When Eli Lilly and Company changes its process chain to include the industry’s largest single-use bioreactors, the world sees an edgy new technology. Behind the scenes, however, careful calculations about benefit, cost, and testing always come first.
Upgrading biopharmaceutical manufacturing facilities comes with inherent trade-offs. Deciding whether to make them takes focus. At a high level, if the disruption of implementing and adapting costs more than the new technology’s benefits, teams should proceed cautiously.
Eamonn Warren, Lilly’s group vice president of API and dry products manufacturing, has led many of these upgrades for the company and has experience evaluating technology, designing floor plans, and picking deployment teams. He’s slated to speak about those ventures during the International Society for Pharmaceutical Engineering’s 2025 ISPE Biotechnology Conference in June.
He agreed to answer some questions about it beforehand. Here’s what he told us.
Can you start by describing the specific advanced technology Lilly has rolled out recently? What were the biggest unanticipated hurdles, and how did you overcome them?
My team has integrated several advanced manufacturing technologies into our new and existing facilities. Notably, on the active pharmaceutical ingredient (API) side, we have implemented an award-winning continuous manufacturing platform for peptides. At our next generation bioprocessing facility, we’re implementing process intensification, paired with feed optimization, in the industry’s largest disposable single-use bioreactors.
We’ve also introduced an industry-first large-scale purification platform using hybrid, continuous technologies to complement it. This was achieved through close collaboration with suppliers on process design optimization and ergonomics improvements, along with a comprehensive start-up program — including media challenge studies and shakedown runs.
How did you decide which upgrades were worth investing in and which were perhaps overhyped?
In addition to standard quality and safety evaluations, extensive lab-scale and pilot-scale evaluations are conducted along with modeling on proposed changes. This helps determine whether these changes will ultimately result in an overall improvement in output.
For large monoclonal operations, it is important to assess the overall balance of the facility as each step is optimized. There is also a trade-off between the cost-effectiveness and efficiency of replicating a facility design directly versus incorporating the latest updates and optimizations. We maintain a very high standard for these evaluations.
Adding new technology has big compliance implications. You describe a "proactive" compliance culture. Is that just innovating while keeping regulator expectations in mind? How does it impede or perhaps inspire creativity and bold moves?
I think the effective application of new technology can improve our compliance position while at the same time improving operational efficiency. This can break the typical tension between compliance and efficiency — what I term the “pendulum swing.” We break this pendulum swing by leveraging advanced technologies in automation, data, and material flows to improve overall operational excellence and reduce the opportunities for human error. This requires working proactively with regulators and the industry, especially on novel technologies and processes, but ultimately it enables bold moves and better compliance.
What guidance would you give to an earlier version of yourself just beginning a manufacturing expansion campaign?
Don't underestimate the importance of people. Your people are the foundation of great work. Building the facility is just one part of starting a new site for making medicines. I learned that hiring earlier and sending tenured employees along with new-hire employees to existing sites can help the team learn both medicine-making and company culture efficiently.
About The Expert:
Eamonn Warren is group vice president of API and dry products manufacturing at Eli Lilly and Company. He has worked for the company since 1995. Previously, he has worked in engineering and operations roles at the company’s Kinsale site and facilities in Puerto Rico, Indiana, Georgia, and the Fegersheim site in France. Before his current position, he was global team lead overseeing Lilly’s parenteral manufacturing. He received degrees in chemical engineering and management and marketing from University College Dublin and Cork, respectively.