IT in the Lab: A strategic view of laboratory and process integration

There are many options to consider when integrating LIMS with the rest of your organization
By Michael Gannon
Orbis Information Systems Ltd.
Contents
Integration benefits
Integration architecture
Process-ready LIMS
Integration with LIMS as a business object
Conclusion
Systems integration for business solutions is changing from a desirable option to an essential requirement. There is in process manufacturing an increasing demand to integrate Laboratory Information Management Systems (LIMS) into the enterprise or supply chain, with the result that quality information becomes more widely available, thereby promoting pro-active quality control. The laboratory itself is an integral part of the organization so it makes sense that its information system links with other organizational divisions.
While integration between different systems has always been technically achievable, it has remained an aspiration for many businesses. It is often the case that whenever the limitations of a particular product might be overcome, or indeed whenever an application might be significantly enhanced, through integration with a business division elsewhere in the organization, this option is deferred. Perhaps the reason is that integration is sometimes perceived as an expensive extra without clear business benefits. In practice, this often results in operators having to move between different software applications to retrieve basic information, with the overhead that this entails.
A simple example of this is in process manufacturing, when a plant operator, using a plant system (e.g. SCADA), is responsible for taking a sample for the laboratory from the process. The sample is taken and the operator is required to change over from the plant system and directly access the LIMS for sample login. This is inefficient because of the time spent between applications, double data entry and required familiarity with two products.
Integration benefits
So what are the benefits of systems integration? The following are most often quoted:
- Single operator interface
- Data reliability
- Wider availability of information for decision support
- Enhanced operational efficiency
- Solutions assembly using Best-in-Class Product and Legacy Systems
Consider the case of a LIMS integrated to a stock system. Product for despatch in a warehouse is automatically assigned a quality control status by the LIMS on lot approval. A certificate of analysis, with full analytical results, is generated in the warehouse at the time of despatch from the stock system. This type of integration meets each of the first four criteria above in that analytical data is entered once into the LIMS, and the LIMS automatically updates the stock system with the lot quality control status when its authorized. The certificate of analysis is generated on request using analytic results retrieved from LIMS, thereby providing data reliability and operational efficiency.
Integration architecture
Modern systems integration architecture demands:
- Configured rather than programmed solutions
- Robust and reliable systems interfacing
- Supports N Tier Client Server
Most of the familiar integration solutions are described as point-to-point, in that there are two applications communicating through a single interface. In the example above, the LIMS initiates a data transfer to the stocks system through a pre-configured routine, and there is a corresponding routine in the stocks system to receive, interpret and store the data. While this meets the business requirement, the point-to-point integration methodology requires the stock system to have significant intelligence built into it to interpret and manage the data that the LIMS will send. Also, the initiating system must have intelligence about the receiving system so that it can send the required data in the correct format. If flexibility and cost effectiveness are to be maintained as major objectives, then this intelligence must be effected through standard configuration rather than customization, the latter often being costly to implement and maintain. Configuration leaves the "ownership" and maintenance of the interface in the hands of the users rather than the external consultants.
Integration between applications demands robustness and resilience. If the interface between the two systems fails, or either or both of the systems fails, then any data in transmission must be recovered and resubmitted when the interface is re-established. This is essential for data reliability. The interface should be self-starting, with error logs for system analysis. A middleware approach to integration, using messaging or brokering, is highly recommended to meet these criteria.
Process-ready LIMS
The SMIP21 middleware product for integrating Thermo LabSystems SampleManager LIMS and Aspentech's InfoPlus.21 (IP21) Process Information Management System, developed for Thermo LabSystems by Orbis Information Systems, is an example of integration middleware that meets the requirements of being configuration driven, with built-in reliability and recovery. IP21 consists of a real-time database, gcs screen builder and process explorer. In the plant, multiple PLC or DCS are connected to the database through specific CIM/IO interfaces (see Figure 1). CIM/IO is a TCP/IP based messaging system with its own client-server architecture. Through the CIM/IO interfaces, IP21 interacts bi-directionally with the respective DCS and PLCs at very high frequencies, storing any data transmitted in the pre-configured database. SMIP21 takes this architecture a stage further by building a specific CIM/IO interface into SampleManager so that it communicates with CIM/IO through its own API.

The interface is bi-directional with the client on either side of CIM/IO initiating a data transfer and writing that data to the corresponding server on the other side. Typical integration scenarios (see Figure 2) include:
- IP21 logs a sample into SampleManager and enters results
- IP21 queries SampleManager for laboratory information
- SampleManager writes results to IP21
- SampleManager retrieves results from IP21
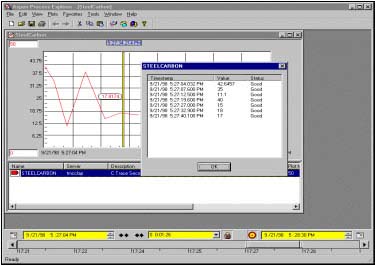
The wide range of standard CIM/IO interfaces available with IP21 result in direct integration between the laboratory and many plant control systems. These include ABB, ACS, AIM, Applicom, Bailey, Fisher-Rosemount, Hitachi, Honeywell, Intellution, Measurex, Mitsubishi, PI, Measurex, Siemens, Toshiba, etc. The LIMS is therefore process oriented, or "process ready."
Integration with LIMS as a business object
Supply chain management solutions require integration of quite different applications, as illustrated in Figure 3 below, even if much of the scope is covered by a single product, e.g. SAP. LIMS becomes a major component of the wider manufacturing supply chain when it is integrated with one or more of these applications, for example with Process and Inventory for quality control, with Finance for job costing, etc. In addition LIMS is accessible from the internet for remote sample login or customer access to specific information.
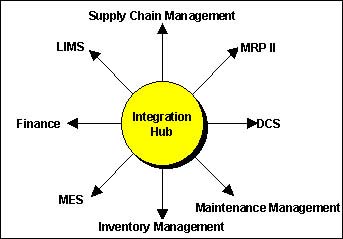
The usual approach to this level of integration is through deployment of a number of point-to-point integration solutions that are either bespoke or proprietary. This is not the most cost effective way of achieving the objective. A centralized integration architecture (Figure 3) recommends itself because the various applications can be integrated through a single integrator ("Hub") using a common integration method for all applications.
The hub itself behaves as a router between applications and establishes connectivity to the various applications through specific product adapters. The adapters can use one or many technologies with the same integrator, e.g. ODBC, COM, DCOM, Corba, XML, BizTalk. Using stored methods, it picks up the data from the initiating system, sends and maps this data to the target system. And it's not limited to raw data. It must also support the transmission of workflows, which consist of data and procedures packaged together and are hence knowledge based. An example of this is transmitting a complete certificate of analysis to the business system, including qc results, lot disposition, certificate format and lot genealogy.
Figure 4 below illustrates a centralized enterprise-wide integration using RealFlow, a product developed by Orbis and its partners. This has process integrated to the laboratory and the warehouse for inventory; the warehouse is in turn integrated to administration. The integration is built through a Graphical User Interface using stored methods and is therefore entirely configurable. Each application, for example LIMS or the financial system, is a business object connected to RealFlow, and each line between the objects in Figure 4 represents an integration method. This approach is often described as "plug and play."
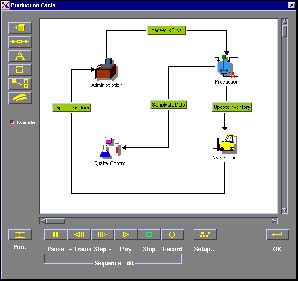
LIMS is included as a business object in Figure 4, hence it becomes part of the strategic supply chain management solution. In fact, this approach to systems integration effectively involves the assembly of different products or applications to provide an enterprise solution.
Conclusion
In deciding to integrate LIMS to other solutions the customer is confronted with a decision about how to obtain the best value for the money. There are two sides to this: the cost of technology and its implementation against the likely business benefits. The cost of integration technology as well as its ease of implementation is relatively less today than it was five years ago. In many cases, the business benefits will speak for themselves, for example LIMS integrated with stocks or to the plant, LIMS integrated with the business financial system for job costing.
Whether LIMS integration is being considered as part of the initial implementation, or because some benefits are expected through integration of an existing LIMS to other live systems, a short business benefit analysis is recommended. The focus of the exercise should be:
- Specify the business' practical integration requirements with matching benefits.
- Review existing systems technologies and corporate standards.
- Specify a common integration technology that will work for all systems likely to be integrated in the short and medium terms.
- Develop and cost an integration plan that meets these requirements and which can be phased, i.e. strategic integration should give the customer options to suit the needs of the business.
The design and implementation of the technologies discussed above are straightforward, but it's good practice to be able to demonstrate measured business benefits and to have a standard approach for future needs.
About the author: Michael Gannon has worked in the international services market for Laboratory Information Management Systems since 1990. He established a LIMS business at Tensor Technologies in 1990 and, with a core group, grew the business to £0.7m by 1997 with an overall return on sales of 20%. In 1998 he established Orbis Information Systems with John Tobin to provide the market with a wider mix of process engineering and integration skills in addition to the already established expertise in LIMS. From start-up Orbis reached a turnover exceeding £2m in 1999 and a workforce of 28 people. The company is geared for further growth in both the European and North American markets.
Michael has worked in partnership with Thermo LabSystems for nine years and is well known to its customer base. He believes that the long term success of Orbis rests in its ablity to form enduring partnerships with its customers. He can be reached by phone at +44-00353-1-2090111, by fax at +44-00353-1-2090130, or email at michael.gannon@orbis-is.com.
About Orbis: Orbis is a systems integrator, specializing in information management for the process and laboratory information markets. The company implements and integrates world-leading software into plant and process manufacturing sites in the petrochemical, food & beverage and pharmaceutical industries.