Is Your Supply Chain Ready For the Biopharma Tidal Wave?

By Trisha Gladd, Editor, Life Science Connect
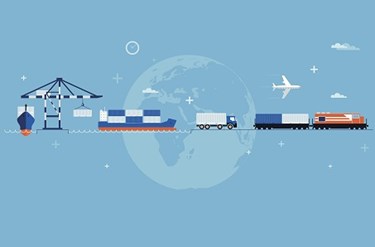
According to recent data from life science market intelligence firm, EvaluatePharma, it is projected that biological products will account for more than 50 percent of total sales within the top prescription products by 2020. Today, biopharmaceuticals make up only about 20 percent of the pharma market. But is the industry ready for this growth?
Andrew Skibo, head of global biologics operations and global engineering at MedImmune/AstraZeneca, was not shy in his keynote at last month’s ISPE Quality Manufacturing Conference about the industry’s readiness, or lack thereof. He warned that this impending biologic “tidal wave” is falling on top of the lowest point of capacity, agility, and resilience that the pharmaceutical industry has ever experienced. Specifically, Skibo addressed the readiness of supply chains and the lack of visibility into them during a product’s life cycle. He referenced a report presented to him last year where 80 percent of companies surveyed recognized their supply chain needed to change. However, only 7 percent of them had actually done anything about it. So what can you do to ensure your supply chain provides a safe and efficient delivery of your product?
Recognize The Importance Of Risk Assessment
In order to manage risk in your supply chain, you have to know where it exists. The same logic is applied when quantifying risks during a process change. Just as a lack of quality affects the patient, so does a lack of supply. Skibo told the audience more than once, “Analyzing quality or product supply risk at a single node is of virtually no value in understanding the risks of overall product supply. Quality metrics are a piece of supply chain metrics, but quality metrics at the site do not do us, including our regulators, any good.”
In an article by the Wall Street Journal, the author listed a failure to build enough production capacity and maintain equipment as well as ward off contamination as reasons for recent drug shortages. It’s possible that these failures could’ve been prevented had a company completed a risk assessment, as urged by Skibo in his keynote. “We routinely codify quality risks for process change,” he says. “We’re not required to do that by regulation, but we do it because it’s good practice.” Completing one for supply chain risks is of utmost importance because it can determine whether or not product gets out the door.
Skibo suggests quantifying risks in dollars. This way you have the dollar amount to show what impact a risk would have should the issue occur. This can help your case should you need to request additional funds or resources to prevent the risk. “We’re judging what we do with inventory based solely on the value of the inventory,” he explains. “A really good supply chain model would give you a dynamic response [to potential risks]. It would be self-correcting. Right now, our first step is to get a model that at least [identifies] the red flags, and then we have to figure out how to correct those red flags.”
Build Risk Into Your Model
It’s one thing to say a risk assessment needs done, and it’s another thing to actually do it. Lance Minor, VP of network strategy and business operations at Medimmune/AstraZeneca, prompted a laugh from the audience when he opened his presentation with this question to Skibo – “You asked why we don’t do supply chain risk assessments. But we do. We have very long risk registers. Isn’t that sufficient?” Clearly, listing risk as opposed to building risk into your model are two very different approaches.
In his presentation, Minor and his team outlined risk at Medimmune/AstraZeneca’s using a Stochastic model. “We took the simple supply chain and mapped out risks from raw materials to shipping,” explains Minor. “At the time, we saw that we had the opportunity to actually capture the risks of every process step and complete a cost-benefit analysis to determine, at any given point in the manufacturing process, the cost to customer service if a risk occurs.” He added that you can also model what the wait time is for a response, such as when you have a site go down or there is a contamination or distribution issue. Applying that modeling throughout your supply chain can help you better plan your production all the way upstream.
Minor discussed a business continuity scenario where they looked at what would happen if their fill site shut down for six months. “We assessed the impact on customer service, inventory, etc., and compared the cost of building up inventory versus having a backup CMO. Very quickly and very intuitively we understood that having the CMO would be a better option.”
In other industry supply chains, a shortage may not be as damaging, but in the pharmaceutical industry, it can mean life or death. Delivering a drug with the highest quality is important, but it only matters if it actually makes it to the patient.