Integrating Analytics And Automation In Cell Therapy Manufacturing

By Tyler Menichiello, Chief Editor, Bioprocess Online
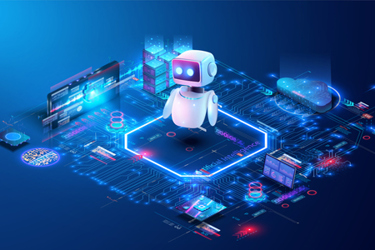
Most people in the industry will agree that we’re still very much in the early days of cell and gene therapies. While every successfully manufactured lot is a testament to human ingenuity and medical progress, the manufacturing process for cell therapies is far from optimized. It is a costly and manually intensive process that’s prone to error — but luckily, one that’s seeing a wave of innovation and investment.
These innovations were the subject of last month’s Cell & Gene Live event, which was focused on the myriad of ways cell therapy manufacturing can stand to be improved. From facility design to new equipment and technologies like artificial intelligence (AI) and improved analytical testing, Chief Editor Erin Harris discussed it all with Vittoria Biotherapeutics' co-founder and CEO, Dr. Nicholas Siciliano, Ph.D. and established executive in cell and gene therapy quality, Will Junker.
An Impending Shift In Skills Requirements
As technology advances and becomes more and more integrated into cell therapy manufacturing, it raises an important question: How will these automation technologies impact the skills requirements and job roles in the workforce?
On the bright side, both Junker and Siciliano believe that humans will remain integral to advanced therapies manufacturing. However, they also think that in coming years, as technology advances and manufacturing becomes more automated, job training and requirements will shift away from backgrounds in biology to those more focused in programming and computer science. “I think you’ll start to see that shift from a skills standpoint at CDMOs and therapeutic companies that are doing in-house manufacturing,” Siciliano says.
Regardless of workers’ backgrounds or how automated biomanufacturing processes become, Junker says, the biggest challenge is the newness of cellular manufacturing and the inherent variability that comes with it. This variability — the unforeseen events common in cellular therapy manufacturing — is the real “beast to be tamed,” according to Junker. “Going towards automation doesn’t take the leaky bags away, and it doesn’t take the problems of particulates away,” he says. “What we need to do is make sure that the staff that’s on site, the operators in the suites, are capable of dealing with these problems in a way that salvages the lot of product.”
Integrating Analytics Into The Process
“What we have seen, I think, is that specific unit operations are relatively automated, but linking those unit operations together to create a full process is still a bit of a challenge,” Siciliano says early on in the conversation. “And that’s where we’re starting to see technologies that are working to do that.”
A critical aspect of stringing these pockets of automation — the unit operations — together, according to both Siciliano and Junker, is the need for real-time analytics built into the system. As it stands, there’s a great deal of traffic between the manufacturing floor and the QC laboratories on a day-to-day basis, says Junker. Being able to integrate real-time analytics into the manufacturing process will help improve turnaround time for production.
“If you’re unable to link manufacturing with analytical results, then at the end of the day, it doesn’t matter how fast you can manufacture it. You’ll still have the bottleneck of waiting for analytics to come back,” Siciliano says.
Automating And Closing The Process
A fully automated, closed manufacturing system — one with built-in analytics — is the “holy grail,” says Siciliano. It also seems to be the eventual expectation of the field, says Junker. “Every health authority I talk to — and I’ve talked to probably most of them by now — has the clear expectation that we go automated,” he says.
There are a host of benefits in shifting towards a closed system manufacturing for cell therapies, according to Junker. “From an economical perspective, you can go away from an ISO 7 suite type of construct when you close a process, meaning you can go into a ballroom concept where you don’t have individual suites anymore, but super suites with many workbenches,” he says. Not only does this allow for greater site flexibility, but this lowering of environmental control requirements from ISO 7 to a ballroom setup can equate to massive savings in the manufacturing process. “Your building becomes easier to maintain, and your equipment that you use for that maintenance is a good deal cheaper to operate,” Junker continues.
However, closing the process entirely doesn’t come without challenges. Perhaps the most significant, according to Siciliano, is that it may inhibit human intervention should something go wrong. “If you don’t have that human element to be able to intervene and potentially correct the process, you’ve also put the patient at pretty significant risk,” he says.
Both panelists agree — before successful automation, the industry needs to focus on “right first time,” i.e., addressing the present challenges and unforeseen events (e.g., leaky bags) that occur in today’s manufacturing before worrying about how technology can make things more efficient.
Invest In A Mature Process
As much promise as emerging technologies have, it’s important not to rush into automating your process. “The process needs to be at a certain level of maturity to be fully automated,” Junker says. Automation isn’t simply having the equipment, “You also need to generate code that integrates that equipment into your process.” In the early stages, when a process is still being refined, there are too many changes being made — “pretty much on a constant basis,” says Junker. For this reason, an immature process doesn’t lend itself to automation.
There’s a “sweet spot” in the course of commercialization where it makes sense to double-down and lean fully into automation — once the variability is foreseeable and the majority of the process is controlled. “The sweet spot is usually, I would say, late stage three, or if you are pivotal on Phase 2,” Junker says. “Maybe in the first year of manufacturing, you can do that.”
Point Of Care Manufacturing
Next month’s Cell & Gene Live event, “Modernizing CAR-T Manufacturing: Is Point Of Care The Future?” will continue this conversation on cell therapy manufacturing with expert panelists Jason Bock, Ph.D., founder and CEO of CTMC, Emily English, Ph.D., SVP and head of manufacturing operations at Cartesian Therapeutics, and Tal Salz, Ph.D., former FDA CMC expert-turned consultant at Dark Horse Consulting Group Inc. We will discuss how technology is improving CAR-T manufacturing, as well as debate whether decentralized, point-of-care (POC) manufacturing can ever truly phase out traditional, centralized manufacturing. The event is scheduled for 11 AM ET on Tuesday, August 27. You can register here for FREE thanks to the event sponsor, CPC. We hope to see you there!