How To Unlock Efficiency In MES Integrations
By BioPhorum
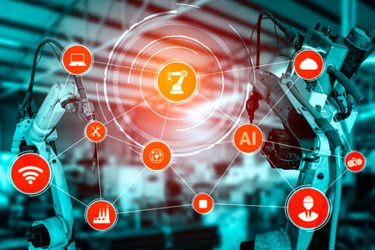
In today’s manufacturing environment, it is essential to have an efficient and effective end-to-end workflow to manage production processes, from the planning stages to the final delivery of goods. Manufacturing execution systems (MES) play a crucial role in achieving this goal. They have evolved significantly over the years, from simple data collection tools to sophisticated systems that can provide a wide range of capabilities. They have also become an integral part of modern manufacturing operations, enabling companies to streamline production processes and optimize performance. However, an MES cannot operate in isolation; it must be integrated with other systems to provide a comprehensive view of the entire manufacturing process.
This article outlines the significance of MES integration with systems such as enterprise resource planning (ERP). A lack of standardized processes in the industry has led to complexity, hindering implementation and scalability. These integration challenges result in manual data entry, increased deviations, longer release times, and higher costs.
Specific integrations highlighted here through use cases can streamline operations, enhance efficiency, reduce costs, and offer real-time visibility across departments and business units. Clear guidelines and recommendations for integrating MES provide a shared understanding of the value proposition and offer insights into the why and what of MES integration for both manufacturers and supply partners.
The Challenges And Misalignments In Integrating MES
Integrating MES with other systems has become increasingly complex and challenging, but it is critical to provide an effective way of executing the entire manufacturing process to improve efficiencies within data transfer. This will reduce the need for manual entry (and minimize human error), therefore reducing time and cost to manufacture.
The current integration process is complex and not user-friendly, leading to difficulties in the setup and configuration for biomanufacturers. The systems detailed in Figure 1 are at different levels of integration maturity, which can result in a misalignment in the capability to connect with different functionalities across the levels. Vendor lock-in is also a common problem, limiting pathways for custom integrations and increasing reliance on vendor support.
Figure 1: Adaptation of the ISA 95 automation functional model/pyramid with example system solutions assigned.
EDMS – electronic document management system, CMMS – computerized maintenance management system, QMS – quality management system, LMS – learning management system, PLM – product life cycle management, LIMS – library information management system, SCADA – supervisory control and data acquisition, DCS – distributed control system, PLC – programmable logic controller, AGVs – automated guided vehicles, AMRs – automated mobile robots
Benefits From Implementing The Information In This Article
The anticipated benefits gained by understanding the content of this article include:
- cost reductions ranging from 10%–30%, depending on the size and complexity of the project,
- the increased likelihood of a successful implementation on the first attempt by 20%–40%, reducing the risk of project delays and failures,
- reduction in project risk by 15%–25%, ensuring projects are delivered on time and within budget, and
- reduction of 20%–40% in the time spent on business case development, enabling faster decision-making and more informed investment choices.
Interface Considerations And Guidance
While the interfaces described here are generally considered mainstream and deliver both data quality and productivity benefits, any interfacing deployments should be undertaken with a thorough understanding of some key points that usually apply across all interfaces:
- impact on quality,
- automated interfaces,
- risk of interfaces being unavailable,
- security,
- data governance, and
- verification signals.
Interface integrations with MES can bring numerous benefits; however, when integrating MES with different interfaces, an organization is unlikely to have the capability to integrate with all available interfaces simultaneously. The time, cost, and resource requirements for interface integration with MES vary depending on several factors, including the complexity of the integration, the existing infrastructure, the number of systems involved, and the expertise of the implementation team. Therefore, it is likely that an organization will complete various integration projects separately over time.
To decide which interface is best to integrate first, it is important to know what the interfaces provide from an MES perspective. Here, we propose a priority for integration with several common interfaces (see Table 1), with number 1 being the highest value. This list is not exhaustive.
Table 1: Interfaces and proposed order of priority
It is important to note that the prioritization of interfaces may differ based on the needs and priorities of each organization. We recommend involving a cross-functional team to assess and prioritize the interfaces for integration with MES, which will help ensure a comprehensive and well-informed decision-making process. The framework for each interface may be used to map your own company-specific interfaces, if not listed in Figure 2.
Figure 2: System integration flow diagram
Here, we look at two of the highest-priority interfaces.
ERP (Material Management)
Use Case
A critical process in a pharmaceutical environment is the application and maintenance of material master data, ensuring consistency of master data across ERP and MES. An important interface enables the material master data to be sent from the ERP system to the MES application upon creation or change of the relevant master data. The interface used to drive this information exchange is the material master message between the ERP and MES.
The role of the ERP system in this interface is to supply the relevant material master data information to the MES. Integration between ERP and MES for the material master is unidirectional (outbound from ERP and inbound to MES) and ensures MES-relevant material known in ERP is also known in MES.
The role of the MES in this data transfer is to receive the relevant material data, to ensure alignment with ERP and enable manufacturing within the MES environment. The material master interface is a crucial integration between ERP and MES and enables the full use of the MES.
Benefits
A material master message integrated between MES and ERP would provide data consistency and accuracy alongside operational efficiency.
Data Quality Benefits:
- Ensures accuracy and integrity of data
- Enables proper use of batches within the manufacturing process and MES
- Provides a complete record of all MES-relevant materials across the full manufacturing process.
Productivity Benefits:
- Enables the ability to implement electronic batch records, therefore removing dependency on paper batch records
- Enhances operational efficiency by reducing manual entry related to materials
- Eliminates manual verification of material data
- Eliminates secondary reviews of material data.
Data Exchange
The following data exchanges are required to create a fully integrated MES/ERP system:
*Note: storage condition details (exposure to various conditions, temperature ranges, etc.) are not currently offered in the marketplace. Products manufactured now are more complex than ever before. These parameters need to be able to be passed automatically from node to node in the supply chain, which could be managed by the ERP systems to help reduce the impact of potential human error.
Challenges And Limitations
Interfacing ERP and MES is a priority to ensure the MES is used to reach its maximum potential. However, there are some challenges in implementing a material master interface. Any material master interface between ERP and MES should consider the following in more detail:
- material master header details,
- material characteristics,
- alternative unit of measurement, and
- mandatory versus optional requirements.
Material master data is critical in the manufacturing process, as it defines the product and material related to each batch. When the data is initially interfaced between ERP and MES, verification/validation is required to ensure the data has been transferred completely and correctly and no disparity has arisen due to application limitations. This verification should be undertaken with the assumption that the ERP is the source system of truth for material master data.
To prevent misalignment, clear and consistent data governance processes are essential. These processes should define the roles and responsibilities of each system, as well as the protocols for data exchange between them. It is important to establish data standards that are consistently applied across both systems. In addition, automated notifications and verification processes can help to identify discrepancies as soon as they occur, allowing for prompt resolution of any issues.
ERP (Batch Management)
Use Case
A critical process in biopharmaceutical manufacturing is the management of the batch master to ensure product quality through traceability of materials during production. Therefore, it is essential to ensure that batches between systems are aligned. The key interface to track and align this information is the batch master message between ERP and MES.
The role of an ERP system in this context is to receive and create batches related to inventory. Integration between ERP and MES for the batch master involves ensuring that the batch data for the inventory is aligned so that the correct batches are identified, used, and recorded. Any additional attributes or characteristics of a batch, such as expiry date or potency that are relevant to manufacturing, must also be identified to support the manufacturing process.
The role of the MES in this context is to receive the batches and use the correct data. However, there are some use cases where the manufacturing process can create batches of products and update the batch data. In those cases, the MES would also need to be able to update existing batch data and create new batches. These data would need to be interfaced with an ERP to ensure alignment.
Integrating batch master data between ERP and MES is crucial for efficient material and batch management. The absence of batch master integration can prevent the full use of MES material and batch management capabilities. This can lead to misalignment between ERP and MES batches, resulting in unnecessary manufacturing and operational disruptions. Without the integration to ERP, the MES would be treated as a paper-on-glass execution system to execute the order, but verification of materials and batches would be manual. Data must be manually entered and updated in the ERP. Manufacturing operators can execute batch steps in the MES, but material inventory and related tracking still need to be manually updated in the ERP, as the ERP is the batch master. The batch master interface is a priority interface for implementation for any ERP and MES deployment.
Benefits
A batch master message integrated between MES and ERP would provide data consistency and accuracy alongside operational efficiency.
Data Quality Benefits:
- Ensures authenticity and integrity of data
- Improves traceability and compliance of batches
- Provides a complete record of the batch across the full manufacturing process.
Productivity Benefits:
- Enhances operational efficiency by reducing manual entry related to batches
- Eliminates manual verification of batch data
- Eliminates secondary reviews of batch data.
Data Exchange
The following data exchanges are required to create a fully integrated MES/ERP system:
Challenges And Limitations
Interfacing ERP and MES is always a priority for integrations and is generally well accepted. However, there are some challenges and limitations with the batch master interface during its implementation. Any batch master interface between ERP and MES should consider the following in more detail.
Batch Master
Batch master data is critical in manufacturing processes, as it defines the characteristics and properties of each batch. When the data are interfaced between ERP and MES, there is a possibility for misalignment and a thorough investigation must be undertaken to determine the root cause of the issue. This investigation should focus on identifying which system is the source of truth for the batch master data. We recommend that ERP should be treated as the master system for batch data, as it typically contains the most comprehensive and up-to-date information.
Batch Status Alignment
While biopharmaceutical companies generally call the names of the batch statuses to be “not reviewed,” “blocked,” and “approved,” the naming of the statuses between two different vendor and supplier systems is usually not aligned or standardized. To address this, a mapping procedure or specification is needed to align the statuses between ERP and MES. This approach is necessary not only from a technical integration perspective but also from a business terminology perspective.
Conclusion
Understanding the synergy between MES and other biopharmaceutical manufacturing systems can empower companies to plan strategically, optimize production processes, and advance toward higher digital plant maturity. During implementation, it is crucial to consider factors such as impact on quality, automated interfaces, business continuity, security, and data governance for successful deployment.
MES integration is critical for enhancing biopharmaceutical manufacturing operations and achieving digital maturity. Following these guidelines and recommendations will facilitate alignment between companies and vendors, enabling them to realize the benefits of a comprehensive and efficient manufacturing ecosystem.
This article summarizes a recent BioPhorum publication on the topic. To read more and see details of further interfaces, check out the full paper in Unlocking efficiency: a deep dive into MES integration for enhanced biopharmaceutical manufacturing.