How Modular Facility Design Can Accelerate GMP Facility Construction

By Tyler Menichiello, Chief Editor, Bioprocess Online
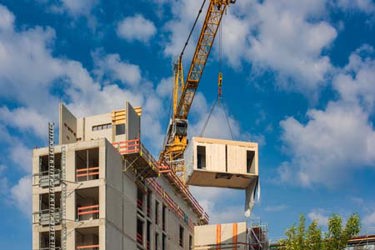
How does that famous Shakespeare quote go? “To build a brick-and-mortar facility or find a manufacturing partner, that is the question.” Okay, Hamlet may not have been fretting over his company’s manufacturing strategy, but it’s a decision that weighs on most biotech executives’ minds at some point. In my time interviewing industry decision-makers, I’ve heard strong arguments for both. Internalizing manufacturing offers more control and autonomy, but outsourcing offers speed, reduced cost, and access to highly specialized experts.
Ultimately, this decision depends on the product, the pipeline, and the company’s long-term manufacturing plan. While there is no right or wrong answer, for Autolus Therapeutics, the choice was clear — the company needed to move out of the U.K.’s CGT Catapult in Stevenage and build its own manufacturing facility.
Editor’s Note: If you want to explore more content about facility design and validation, I suggest you check out our recent Pharmaceutical Online Live event on the topic, which featured bioprocessing facility experts Erich Bozenhardt and Herman Bozenhardt, as well as process architect Fred Grossfeld. You can read the key takeaways from that event here.
Truncated Construction Timeline
The move out of the U.K.’s CGT Catapult was driven by Autolus’s need to scale manufacturing ahead of the commercial approval of AUCATZYL, its lead CAR-T product for adults with relapsed refractory B-cell acute lymphoblastic leukemia. “It’s great to be able to manufacture on a clinical-trial scale, but that won’t sustain global supply for the indication,” Vann says.
The timeline for the facility’s construction was as follows:
- Initial design began in 2021, with the groundbreaking happening on November 8, 2021
- By November 25, 2022, the first cleanroom was operational
- The first piece of manufacturing equipment was installed on December 14, 2022
- By May 2023, Autolus had initiated the facility’s capacity challenge, a stress test that precedes facility validation
- In Q1 of 2024, the facility received its GMP manufacturing certificate from the Medicines and Healthcare products Regulatory Agency (MHRA)
So how was Autolus able to build The Nucleus in nearly half the time of a conventional facility?
“Because we actually built the building from the inside out,” Vann tells me, through a modular, preassembled construction strategy.
Jenga-Style Modular Construction
Around 70% of The Nucleus was built off-site. Vann describes the preassembled modules coming together like Jenga blocks, sliding into a steel frame and being bolted into place. “On the side, there was an open wall, and pieces would come up to the level they needed to be, and they would be slid inside the building,” he says. As you can imagine, the “Jenga blocks” that came together to form the 70,000-square-foot facility were quite big, says Vann. In fact, the U.K.’s biggest and second biggest cranes were used to construct the facility, he tells me.
“Some of these blocks are 25 meters long,” he explains, “and they have to be precision engineered within centimeters.”
Aside from the significantly reduced building timeline, the company’s inside-out construction approach allowed the Autolus team to operate the facility while it was still being built. “We were able to do things like the challenge test while the facility didn’t actually have all of its walls on,” Vann says. “That allowed us to accelerate the operations and learn about the facility while it was being completed.”
Build Where The People Are
The Nucleus is geographically situated near the CGT Catapult facility in Stevenage where Autolus was already doing its clinical trial manufacturing. “We’d built a really strong team, and it didn’t seem sensible to move,” Vann tells me. Well-trained people are critical to run a successful CGT manufacturing facility, and they’re hard to come by. In the interest of retaining the area’s top talent, Autolus opted to build in Stevenage.
Not only did the company avoid having to rebuild its operating staff from scratch, but these seasoned employees were able to train and onboard more than 100 new operators for The Nucleus. By building the new facility in proximity to the existing staff, Autolus was able to develop this training program in a designated training center within The Nucleus. “That probably would not have been possible had we not maintained the expertise of the people we already had,” Vann says.
Whether it’s in choosing a construction strategy, hiring the right team, or building systems and processes, “The devil is in the details,” Vann tells me. “You’re only as good as your weakest link.” The Nucleus stands as a testament to this mindset. Through intentionality and attention to detail, biopharma companies like Autolus can accelerate facility construction and readiness without sacrificing quality.