How Can You Mitigate The Risks Of Single-Use Bags?

By Trisha Gladd, Editor, Life Science Connect
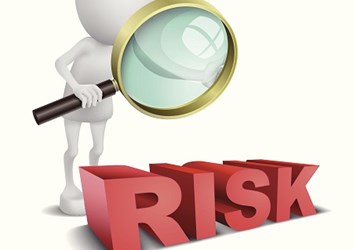
In my last article with Chuck Hart, director of manufacturing at Prolong Pharmaceuticals, he discussed several considerations to keep in mind when switching to a single-use process in your facility. Specifically, Hart covered an important deciding factor when it comes to determining if you should even use single-use technology (SUT), as well as storage space in your facility and what experts you should involve in the design phase. Additionally, he talked about the vendor relationship and how to determine which vendor is right for you. In this article, Hart offers his insight on a major area of concern when it comes to SUT—bag integrity.
The loss of product as a result of bag failure isn’t just an annoyance; it’s an expense, and a costly one at that. Plastic bags can tear easily, so you have to have a plan in place to make sure bag failure is considered and prevented every step of the way. However, Hart says with proper fitting and handling, these concerns can be mitigated.
Customize For A Perfect Fit
Bag failure control begins with the design. This is another area where Hart says a strong partnership with the vendor and the need for them to understand the cost of bag failure is crucial. While at a previous company, Hart recalls an instance when the company subcontracted the manufacturing of their tanks to one company and their bags to another. The customization of the tank to the bag was not handled well and the bags did not fit the tanks properly. Because of this, the bags shifted within the tank during filling and when in use. “As they were shifting, the bag was rubbing against the sides and the bottom of the plastic tank,” explains Hart. “Just a quick rub of the bag across a small area of the plastic tank caused a burr in the bag, which was confirmed by testing. Multiple movements during filling and use caused small tears in the bag.” When it comes to the failure rate of a bag, Hart says he expects less than a one percent failure rate. In that particular instance though, the customer experienced a 5 to10 percent failure rate. The vendor did work with the customer to resolve the issue, but the resolution was to discard the plastic tanks and purchase new stainless steel totes (at a significant cost to the customer).
Proper fitting is especially important when using square tanks. According to Hart, it is less expensive for suppliers to produce square tanks as opposed to cylindrical tanks. As a result, manufacturers experience savings too. For the new facility, the Prolong team decided to purchase all square buffer and process tanks. However, when it comes to fitting a bag and ensuring it expands properly in a square tank, he notes that manufacturers should pay particular attention to handling procedures. “Most experienced vendors will provide specific training on bag setup, like when to pull the four corners out during filling or how to ensure proper bag manifold height for large tank fills. If the training isn’t specified though, the customer should insist on it,” explains Hart. “If bag setup and filling is not performed properly, the result could be unnecessary strain on the bag or manifold, leading to potential bag failure.”
Handle With Care
Bag integrity must be maintained from distributor to warehouse to process area, which requires careful handling of the bags at every step of the way. One way to safeguard disposable bags is by drafting specific and detailed handling procedures for all departments that come in contact with the bags. These instructions should include proper tools and techniques to use for opening boxes, unfolding and inspecting bags, transferring bags from area to area, and proper bag insertion. While at face value, these procedures would appear easy and obvious, dismissing these instructions as basic and non-critical could lead to unnecessary bag damage. As with most “new” tasks, training and adherence to details are very important.
In an example of an incident where procedures such as this would’ve been a valuable tool in preventing bag failure, Hart recalls an investigation into a contaminated bioreactor, where they discovered a pin-hole sized puncture in the bag as the root cause of the contamination. Upon examination, it was determined that the bag was manufactured correctly but the puncture occurred during its handling. It was also discovered that warehouse employees typically used utility knives to open boxes, including boxes of bags. As a result, procedures were changed to use box cutters only when removing components from boxes. It is proactive planning such as this that Hart urges manufacturers to consider implementing, in order to minimize bag breaches.
Integrity Testing – Can It Be Done?
According to Hart, unlike stainless steel tanks, which have straightforward pressure hold methods to ensure tank integrity, there currently isn’t a full-proof process for pressure testing, which is absolutely crucial. “While quite a few bag pressure integrity testing ideas and techniques are being examined, there has not been a single approach that has been proven effective,” he explains. “The current ideas are either ineffective or come with cumbersome procedures or accessories. For this reason, incorporating a thorough inspection procedure for bag release and at setup is essential.”
Inspecting single-use bags is a difficult task, especially as the bags get larger. It’s up to the manufacturer to create a robust qualification method for the inspection of bags, as well as other disposables (tubing sets, filter assemblies, etc.). Because of the need to unfold the bag, manual inspections of large volume bags is nearly impossible, and even then, it requires additional aids (i.e. lighting source and magnifying tools) to truly inspect the entire bag. When you’re talking about bags designed to hold as much as 3,000 liters, the task becomes insurmountable. So how do you do it?
“With a stainless steel tank, you perform a pressure integrity test. It’s fairly basic,” says Hart. “Put 20 psi of air in the tank, isolate valves at your clean boundary, and make sure the tank holds pressure. You can’t do that with a bag. If you put even one psi of air on a bag, it’ll blow up like a balloon.” For this reason, Hart says manufacturers should be skeptical of any vendors making the claim of a full-proof pressure integrity test. While he says it’s possible a robust and simple test will be available in the near future, there isn’t one that he would confidently use. “Until that vigorous test is established, leveraging vendor expertise, careful bag handling, and thorough bag inspection should be the points of focus.”