Harnessing Lab Deviations For Performance Transformation In Vaccine Manufacturing
By Bob Johnson, Tunnell Consulting
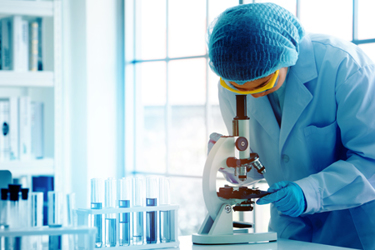
In the pharmaceutical laboratory, deviations occur, sometimes frequently, and with varying degrees of seriousness. Generally speaking, a deviation leads to non-compliance and, as such, requires careful tracking, monitoring, and remediation.
A deviation may take one of two forms: It may occur when instructions regarding a specific activity, such as those laid out in the standard operating procedures (SOP), batch record instructions, or other guidelines, are not carried out, are delayed, or are performed incorrectly; or a deviation may also be defined as a difference between normal and expected value in the pharmaceutical laboratory process. In some cases of course, the two types of deviations may cross over if an unexpected value is the result of a procedural error. It is those deviations and errors – and the subsequent actions that must be taken to address them – that cause an already long development cycle to become even longer. In the event of a public health crisis, time is of the essence, and measures must be taken to reduce the development cycle time while maintaining quality.
The presence of deviations in the pharmaceutical process may seem inevitable, and it has always been an obstacle in not only achieving full compliance but also in meeting demand and keeping per-unit costs down. More recently, here at Tunnell Consulting, we have also seen that in responding to a public health crisis such as COVID-19, the presence of such deviations – without a comprehensive way to document, remediate, and prevent them from occurring in the future – may trigger inefficiencies and make it difficult to respond to the emergency on a timely basis. During the present healthcare crisis, we have seen pharmaceutical manufacturers respond with unparalleled speed and efficiency, and this response may well set the tone for laboratories in the years to come.
COVID has brought to light the question of how vaccine manufacturing sites can, not just in the case of COVID but in all vaccine manufacturing projects now and in the future, manufacture more vaccines, more efficiently, and at a competitive price in the global market.
Regulatory Compliance And Addressing The Root Cause Of Deviations
Whether the deviation is a one-time anomaly, a systemic problem, or the result of a lab technician error, regulatory compliance demands that the deviation be fully documented and, further, that an action plan be put in place to address the deviation and its root causes. Monitoring, documenting, and creating a corrective and preventive action (CAPA) plan is essential. CAPA identifies and implements corrective and preventive actions that address the root cause of the deviation and prevent it from occurring again.
Performance Transformation And A Right-First-Time Model
The CAPA, to be effective, will include transformational – not just procedural – changes. The performance transformation methodology takes a holistic approach to establish a site-wide, right-first-time model to make vaccines accessible as soon as possible, reduce cycle times, improve competitiveness, and roll out greater collaboration and integration across all site functions. Also, by addressing the root causes of the deviations, the manufacturer is able to improve regulatory compliance and ultimately establish a transformational change program that creates a new and more effective culture, establishing new behaviors and risk mitigations going forward.
Performance transformation addresses not just the limitations of processes but also the root cause of deviations and errors through a permanent transformation of processes and human behavior. The “right-first-time” model – integral to the performance transformation methodology – is deeply embedded in the mindset of the pharmaceutical industry and lies at the heart of the drug development process.
Unfortunately, the imperative to get the entire process right the first time out of the gate conflicts with behavioral patterns, turf battles, and a “we’ve always done it this way” mentality and resistance to change. Those in the laboratory may, for example, be comfortable with using legacy devices and taking manual readings, but this naturally lends itself to error. But beyond these operational and technical processes that can be easily improved, the “people” processes may meet with more resistance as the lab manager finds it difficult to get the right people on board. One way to overcome such resistance is through tracking key performance indicators (KPIs) on a more frequent basis on a visual board, showing clearly how those KPIs improve over time as the new operational and technical processes take hold.
A Performance Transformation Case Study With A Vaccine Manufacturer
Looking back at a specific case study pre-pandemic, we can see how the performance transformation methodology applied in the past and may also apply in future responses to other public health emergencies. In this case, a vaccine maker had a backlog of thousands of deviations, was not able to meet demand, and suffered unacceptably high per-unit costs.
Numerous process and people issues were uncovered that were adversely affecting the company’s performance. Some functions were working in silos with little communication outside their small groups, remediation projects were not integrated, and the site had complex people issues due to heavy use of temporary labor. The transformation was accomplished in three waves, which began with creating buy-in and building momentum for a right-first-time mentality, changing deeply rooted behaviors that were negatively impacting performance, and developing internal leaders to sustain the changes.
The first and most important step was to overcome the “we have always done it this way” mentality, which created resistance to transformative projects. By first prioritizing projects, the company was able to uncover hidden capacity to tackle the transformation. Visual boards were used to track KPIs as the new practices took root, and deviations steadily dropped, resulting in winning over team members who had previously been resistant and achieving a critical mass in personnel taking part in the transformation. In addition to visual management, the team deployed focused factory team support (FFST), a multidisciplinary team that would meet, typically during shift changes for that focused factory, to quickly resolve issues identified on the visual boards. The FFST concept supported operations and provided regulatory guidance on the shop floor to and consistently drive improvements. To sustain the transformation long-term, 12 in-house coaches, or in-house leaders, were trained in the right-first-time culture, so that the behavioral benefits would continue for years to come.
The project reinforced quality and compliance while also achieving cost savings greater than 5:1 ROI, reducing cycle time for change control by 55%, and reducing review time for batch records from 33 days to 14 days. The transformation also reduced environmental monitoring (EM) error correction requests by 57% and EM-related deviations by 48% and positioned the company to sustain a right-first-time approach into the future.
The lessons learned from this situation, and the unprecedented speed at which vaccine manufacturers responded to COVID, will be useful in creating a vision for responding to future health crises.
About The Author:
Bob Johnson is group vice president at Tunnell Consulting, a management consulting firm dedicated to solving complex problems for life sciences companies and government agencies. Focused on pharmaceutical, biotech, and medical device organizations, his areas of expertise include operational strategy, lean manufacturing, performance and compliance transformation, organizational effectiveness, change management, sales process improvement, and strategic outsourcing.