Getting The Most From Your MOTIV® Inline Buffer Formulation System
By Nainesh Shah, Sr. Application Engineer, Asahi Kasei Bioprocess America
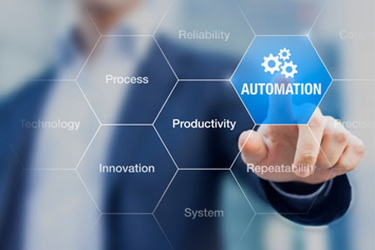
As the biologics and advanced therapy spaces continue to grow, the need for more agile and adaptable processes supporting these modalities has yielded new and improved solutions to support their production. Because most manufacturing processes consistently require buffers and in large quantities, ensuring that their production is as timely and cost-effective as possible can go a long way in optimizing scale-up and commercialization.
Traditional buffer formulation is often a time-consuming and labor-intensive process. From mixing components in large tanks to sampling to performing analytics in order to determine release parameters, these approaches typically require considerable back-and-forth to arrive at the right final product. This time investment, coupled with the space required for tanks, piping, raw materials, and other operational components, as well as the cleaning and validation steps necessary to ensure compliance and quality, can equate to a massive operation, one that can compound significantly as a program scales. An automated, integrated, responsive inline buffer formulation system can help eliminate the need for intermediate storage, reduce facility footprint, and accelerate timelines.
Get unlimited access to:
Enter your credentials below to log in. Not yet a member of Bioprocess Online? Subscribe today.