Exploring Sanofi R&D's Batch Monitoring Initiative
By Patricia Seeboldt and Phan Anh Dao — Sanofi, and Brigitte Herren — a-connect
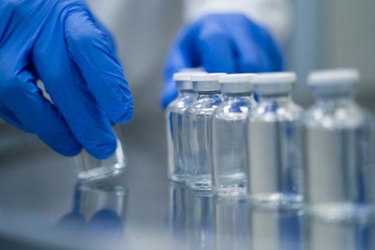
In R&D environments new drug development projects must be typically delivered within ambitious timelines. As such, they are often characterized by agile start-up environments with low operational process maturity. Furthermore, projects operate within highly complex global delivery structures. Lack of process transparency and accountability typically lead to inefficient handover points and volatile delivery timelines. As such, low process maturity directly compromises the demand for high supply predictability in clinical trial programs.
To manage both fast project ramp-up times and delivery predictability, Sanofi sets global lead time targets for its R&D production, testing, and release processes. Its Amsterdam site has successfully implemented an approach that led to a swift and reliable reduction of lead times below target within six months. The approach combines following levers:
- Process transparency and accountability
- Real-time batch data entry and monitoring
- Tight cross-functional and third-party governance
- Continuous improvement
This solution, an approach that is affiliated with and owned by Sanofi, is currently being implemented globally. Understanding human behavior and cooperation is thereby of key importance. A high focus was put on overcoming silo orientation and involving local teams to adapt the approach to fit their needs.
Batch Monitoring and Lead-Time Results at Amsterdam Site - illustrative
Business Context And Challenges
R&D teams operate in highly complex environments. Scientific ingenuity and focus must be matched with delivery excellence to support ambitious clinical trial programs. Many different organizations, functions, talents, and skillsets across the globe need to come together to develop and deliver a new drug program for clinical trials. Thereby, these global teams move in competitive industry environments to deliver best-in-class products to patients first.
Sanofi’s Batch Monitoring Project focused on implementing an approach that would quickly bring about the needed level of predictability in an R&D project’s testing and release processes. These processes are typically characterized by structures and content-specialization that lead to an inward functional or silo focus, as shown in the table below.
In bringing about fast improvements to the end-to-end testing and release lead times, specialists must cooperate cross-functionally. This can create conflicts of interest. Involved specialists are often under considerable time pressure and are incentivized to deliver only their part of the process. The task is thus to create structures and targets that lead to the necessary cross-functional orientation.
Example: The following platform’s testing and release process times illustrate the outcome of a typically silo-oriented project. Lead times fluctuate high above the target and don’t show a downward trend. Single lead times are above one year.
Batch Monitoring Project: Scaling The Approach Globally
Background and target
Sanofi defines batch monitoring as an R&D key capability. Production, testing, and release processes of each of its projects must be transparent, measurable, and manageable across all parties. In particular, this means:
- Batch transparency – Teams know exactly where each of their batches is in the production, testing, and release process and how they perform versus target. Issues and bottlenecks are discussed and tackled in real time.
- Continuous improvement – Teams have a clear understanding of which issues to solve to increase their success rate and drive down lead time. Issue and escalation management is defined and works as part of the cross-functional governance structure.
- Inventory Transparency – Teams know exactly where each of their batches is located. All necessary data to characterize the batch is available and accessible.
- Demand and Supply Alignment – Production schedules align with clinical and non-clinical needs. A supply and demand function is set up to manage the storage, allocation, and shipment processes.
Project Approach And Design Principles
Due to the outlined content focus and specialized structure (silos) of R&D environments, implementing a cross-functional initiative required special attention to human behavior, cooperation, and motivation. Creating transparency, measuring and sharing data across functions, and setting up common goals requires trust in a one-team approach. This team, however, first must be created and members must believe that their time is well invested in this cross-functional effort. Performance incentives as well as management reporting and escalation structures must align to support and guide the effort.
Based on the experience of the Amsterdam site team, three interdependent skills areas must be in place in a central project delivery team to enable the implementation:
Local Co-creation And Ownership
Implementation of the project was conducted with a “bottom-up” approach. A clear focus was put on involving and enabling each local platform team. Teams included members from the following functions: supply chain, manufacturing, quality control, and quality assurance.
General design principles and guidance were defined, but teams could make their own decisions about how they wanted to localize their end-to-end process, measurements, and monitoring. The batch monitoring tool is highly adaptable in terms of inputs but reports lead time results in a standardized layout to management.
Management reports focus on overall lead time and improvement. Reporting is delivered by each team, rather than through a multi-site reporting solution. This empowers each site to define and tell their own improvement story and eliminates a perceived top-down “control and compare” focus.
Key building blocks and design decision of the solution are:
- Pragmatic implementation approach
- The cross-departmental monitoring tool is based on a high-level process view and departmental handover points only. This eliminates lengthy and detailed process modeling efforts in an agile and quickly changing development environment.
- It prevents double entry of data. The batch monitoring tool is linked to more detailed existing departmental trackers.
- The tool uses readily available software solutions and can be implemented by internal resources and quickly set up with low implementation cost.
- Intuitive tracking and forecasting
- The batch monitoring tool works like a dynamic train schedule. Data is entered in real time and any subsequent activities are updated automatically. Intuitive and visual reporting outputs draw attention to specific issues and bottlenecks.
- It provides full transparency so any participant can see all data points across the end-to-end process.
- Cross-functional governance
- Weekly batch monitoring meetings are steered by operations (ideally supply chain or manufacturing) and include representatives from all involved functions. Results and any subsequent actions and improvements are discussed together.
- Tier structure escalates issues from shop floor to top management. Escalation processes are clearly defined to ensure swift decision-making and resolution.
- Management reporting focuses on improvements
- Regular management reporting focuses on continuous improvement initiatives and their impact on reducing overall lead time.
- The cross-functional overall goal setting fosters a one-team approach rather than singling out individual functions.
Implementation Plan
A global kickoff assured the dissemination of knowledge and stakeholder engagement of platform leads. Subsequently, the central implementation team worked with each platform lead (local implementation champion) to define the local cross-functional team and work toward a platform-specific solution. This included defining the high-level process, handover, and data points, customizing the batch monitoring solution, and coaching teams on implementing their cross-functional batch monitoring meetings and continuous improvement process.
Negotiating process steps, dependencies, and lead times across departments is an iterative process. There are different understandings and concerns. Navigating these discussions well sets the tone and is key in team building.
Lessons Learned
The central implementation team encountered a different level of process complexity, process maturity, and behavioral readiness at each platform and site. It carried out respective maturity assessments and tailored their implementation approach by involving the local teams.
Despite structural and process realities, implementing a tried and tested batch monitoring approach is first and foremost a behavioral and change management challenge. There must be a shift from silo orientation to cross-functional and end-to-end thinking as a new way of working. The cross-functional batch monitoring meetings are key. Upholding a tight meeting discipline and a focus on real-time data require the dedication of a local management sponsor/champion who will drive the meetings and assure respective preparation and data consistency. Additionally, the champion needs to foster a one-team approach and drive improvement by encouraging and celebrating small successes. Every small step could have a big impact.
Providing not only content and systems support but also human behavioral and coaching expertise proved invaluable. Our business coach used — among other tools — a behavioral typology model to tailor messaging and conflict resolution strategies. This engaged individual team members and increased the understanding within the implementation team for specific behavioral resistances – see the downloadable appendix for a detailed description of the methodology.
Acknowledgements:
The authors wish to acknowledge Bruno Figueroa, global head of genomic medicine CMC, for his support in this project.
About The Authors:
Patricia Seeboldt, CPIM, is a supply chain director and business advisor with over 20 years of managerial expertise in the pharmaceutical industry. As head of production planning and raw material strategy at Sanofi, she enhances the availability of medicine for patients by optimizing the performance of the end-to-end supply chain, driving operations excellence and leading multidisciplinary teams. For the work covered in this article, she acted as the methodology lead, behavioral change expert, and coach. Connect with her on LinkedIn.
Phan Anh Dao, M.Sc., is a quality director with 15 years of managerial experience in the pharmaceutical industry. As head of quality at Sanofi, Dao ensures the highest quality standards and business integration covering the entire process from manufacturing to testing, to systems quality, to external party quality management. For the work covered in this article, Phan acted as project lead and quality best-practice implementation expert. Connect with Phan on LinkedIn.
Brigitte Herren, MBA/MA, is a consultant with a-connect. She has worked as a transformation director for global corporations for 20 years, including eight years for oncology-related business optimization work. Her engagement for Sanofi comprised post-merger integration, GMP readiness, and KPI and business performance management work. For the work covered in this article, Brigitte was responsible for project management and tool design and Implementation. Connect with her on LinkedIn