Driving Efficiency And Ingenuity With An OPC Platform
By Chris Rombach, VP Sales & Marketing, Asahi Kasei Bioprocess America
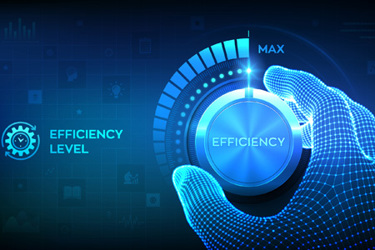
The regulatory approval of several oligonucleotides over the past five years – combined with the recent headlines around rapid COVID-19 vaccine development – has created significant interest in the oligonucleotide (DNA/RNA) segment of the scientific industry. This includes everything from antisense oligonucleotides (ASOs) to lengthy gene transcript mRNA, as well as shRNA (small hairpin RNA), siRNA (small interfering RNA), CRISPR/Cas9 and anti-miR (anti-micro RNA).
The ability to rapidly create, study and formulate these nucleic-acid-based sequences and obtain authorization to provide timely therapeutic benefits to patients is more critical than ever. Robust data analytics from each unit operation – as well as throughout the processing flow continuum – can allow for fewer batch comparisons, thereby decreasing the molecular development timeline, in addition to decreasing the molecule’s cost to market.
To achieve these advances, however, there may need to be changes to currently accepted equipment design and utilization mechanisms for nucleic acid production. Many times, a preferred platform may be utilized for X operation, and yet another might be used for Y operation. This preference can be driven by hardware, software, industry expertise, customer support, lead time/availability and/or design; but, regardless, can create unnecessary imbalances in data output. The ideal arrangement would be to have a unified platform that could communicate with all equipment variations, allowing customers to choose any vendor without sacrificing core or regulatory type expectations for analytics capture and reporting. Such a solution would entail a future-proof, open platform communication (OPC) setup that would allow scalability and the ability to cover many instrument types.
Get unlimited access to:
Enter your credentials below to log in. Not yet a member of Bioprocess Online? Subscribe today.