Designing Facility Monitoring Systems For Cleanrooms
By Tim Sandle, Ph.D.
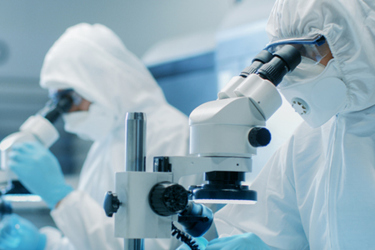
A facility monitoring system (FMS) comprises a series of interconnected devices in a network that feed data back to a central hub. The devices provide data relating to continuous monitoring of aseptic and other controlled environments. The devices are equipped with environmental sensors, and they can be fixed in position or include mobile equipment temporarily connected to the system via a network port or Wi-Fi.1 The overall industrial architecture design includes the devices, their sensors, alarm points, IT hardware and processors, a server, and a data repository, together with software to enable data review.
In a previous article, we looked at the cGMP requirements for an FMS. This established how an FMS aids the facility in meeting regulatory compliance through the monitoring and logging of critical environmental parameters. Here, the focus is on the design elements of an FMS.
What Is An FMS Designed To Do?
The extent of what an FMS monitors will vary between facilities. Typically, an FMS will assess airborne particles, temperature, humidity, and pressure differential. This may extend to other measures such as air velocity, cleanroom air supply, and distinct items of microbiological monitoring equipment like active air samplers.2
Advantages Of An FMS
Key advantages of an FMS are:
- continuous data capture,
- data held on a server,
- the ability to assess alarms in real time (audible or visual), such as when there are sufficient particles present, the counter will indicate that the environment is no longer in compliance, send a signal to the software, and sound an alarm,
- the ability to trend data and to produce reports, permitting the evaluation and analysis of real-time (online) data and (offline) historical data,
- data security, such as password protection,
- data integrity, including the means to review audit trails,
- the ability to synchronize time across all instruments.
- a mechanism to bring all key data together,
- computerized and predictive maintenance planning, and
- early detection of problems and early warning of process deviations.
In addition, those FMS systems can control as well as monitor:
- process parameters, resulting in protection of the process and the product,
- cleanroom air supply and air extraction, and
- energy consumption, resulting in optimization of operational and utility cost.
System Architecture Considerations
An FMS consists of instrumentation that collects and communicates measurements and status information about the cleanroom to a hub, usually in the form of digital and analog inputs. This may lead to alarms sounding or automated programs being executed. Automated control is achieved through control loops, written logics, and start/stop functions. The automated responses are detailed in control recipes based around the desired pressure gradients, temperature and humidity set points, tolerances, and time spans. Delayed time settings need to be set for an alarm where automatic controls/responsive actions are in place (for example, with a pressure differential to account for the momentary opening of a door). Data is held until the user elects to view it through a graphical interface, permitting manual intervention.
FMS Design Considerations
Typical design considerations for an FMS include:
- server with database and client to facilitate FMS information, viewing, controlling, and data storage to a client workstation;
- user interface;
- system interface (between controllers and a server);
- controllers (programmable logic), such as for monitoring and controlling the air handling system;
- room-mounted differential pressure sensors;
- temperature and relative humidity sensors to measure air duct or room temperature and relative humidity; and
- measurement of airborne particulates.
The aspects that require conceptualization and development when designing the FMS include:
- Understand the facility layout, including the pressure differential layout; the air classification layout; the routes of personnel, product, and equipment; air handling unit scope layout; filter cut-out layout for the room (where pressure differential across the filter is controlled); and the utility system, including the chilling unit, hot water unit, steam unit, and so on.
- Define the process parameters to be programmed into the FMS.
- Determine where the instruments are to be positioned, in such a way that they are representative of the cleanroom and/or oriented toward higher risk locations (such as where personnel congregate or where there is open processing).
- Account for activities that might damage instruments, such as avoiding placing a particle counter near a glove changing station since alcohol sprays may occlude or damage the particle counter’s sensitive optics.
- Position instruments so they can be removed without compromising the status of the cleanroom to permit calibration, servicing or “hot swapping” in the event of a breakdown.
- Instrument sensors should be at a distance consistent with any minimal requirements for accuracy and precision (for example, particle counting tubing connecting a probe to the counter would not normally exceed 1 meter in length and have minimal bends).
The design must also assess core data integrity elements, including electronic signature and records; the audit trail at the database level for GMP critical data like log, trend, alarms/events, etc.; the data backup strategy based on the criticality of the data; user administration and access protection; reporting requirements such as the generation of an out of specification report; and disaster recovery.
The design characteristics must be maintained throughout the system’s life cycle. The life cycle is represented by the following four major phases:3
- the concept, and initiation, of a change control;
- project: planning, specification, configuration, coding, verification including instrument and system validation, and release;
- operation, including instrument calibration; and
- retirement.
The installation, calibration, and tuning or routine verification of the instrumentation is critical to the process control and monitoring. The ranges of the control parameters are evaluated during initial system implementation and are modified based on the requirements of the cleanroom or suite of cleanrooms. The configuration specification should be maintained throughout the life cycle of the system, with changes in the recipe agreed through change control and recorded.4
For monitoring and control, the following functions need to be built, configured, and maintained:
- software for monitoring the system,
- scheduler for scheduling the activities for energy management,
- alarm viewing and monitoring tools,
- alarm escalation route with workflow and electronic signature as part of alarm acknowledgement, with alarms configured as:
- basic alarm (for alarms not requiring user interaction)
- simple alarms (for alarms requiring acknowledgment)
- extended alarms (alarms requiring acknowledgement and reset),
- trending tool for data analysis, and
- reporting tool and generation of the report in the required format.
In terms of the operating parameters, in some cases these will be fixed in regulatory guidance documents (like the maximal permitted value of airborne particles); in other cases, they need to be user defined, such as temperature and relative humidity, measures that will depend on the product and the nature of the operations carried out (accounting for the contamination control concern of avoiding excessive perspiration on the part of process operators since this will compromise the integrity of the cleanroom garment).
Realization Of Good Design: The Advantages Of Data Interrelationships
A benefit of the FMS is the opportunity to assess data patterns and interrelationships, a process that feeds into the contamination control assessment.5 For example, this approach enables the determination of a consequential impact (for example, while an increase in temperature may not directly impact the product, the resultant heat profile may give rise to changes in humidity or particulates). The approach also helps with capturing parameter relationships (such as whether a room differential pressure is an accurate reflection of air change rates and, hence, whether the airflow needs to be monitored). Understanding the data generated also enables monitoring the relationship between control parameters and the product, such as how much time can elapse before a deviation from a control parameter, like low pressure, impacts product quality.
References
- Xueliang, M., Huo Ghovanloo, H. (2007) A Wireless Pharmaceutical Compliance Monitoring System Based on Magneto-Inductive Sensors, Sensors Journal, IEEE, 7: 1711-1719
- Sandle, T. (2013) Contamination Control: Cleanrooms and Clean Air Devices, Encyclopedia of Pharmaceutical Science and Technology, Fourth Edition, Taylor and Francis: London, pp634 – 643
- Mourka, A. (2013) Clean Room Monitoring System for Pharmaceutical Companies, Technical University of Denmark: http://www2.imm.dtu.dk/pubdb/edoc/imm6641.pdf
- Arden, N. et al. (2021) Industry 4.0 for Pharmaceutical Manufacturing: Preparing for the Smart Factories of the Future. International Journal of Pharmaceutics, 602: https://doi.org/10.1016/j.ijpharm.2021.120554
- Ashfaq, F. et al. (2020) Towards Data-Driven Approaches in Manufacturing: An Architecture to Collect Sequences of Operations. International Journal of Production Research, 58 (16): 4947–63
About The Author:
Tim Sandle, Ph.D., is a pharmaceutical professional with wide experience in microbiology and quality assurance. He is the author of more than 30 books relating to pharmaceuticals, healthcare, and life sciences, as well as over 170 peer-reviewed papers and some 500 technical articles. Sandle has presented at over 200 events and he currently works at Bio Products Laboratory Ltd. (BPL), and he is a visiting professor at the University of Manchester and University College London, as well as a consultant to the pharmaceutical industry. Visit his microbiology website at https://www.pharmamicroresources.com.