Corning A Force For Flow Reactors
By Louis Garguilo, Chief Editor, Outsourced Pharma
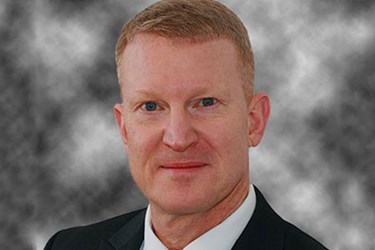
On a morning in Shanghai when the air is anything but, Dr. Yi Jiang of Corning is crystal clear on his view of the biopharmaceutical industry’s transitioning from batch to advanced-flow reactors.
Jiang, global business director for Corning Reactor Technologies, speaks with the assuring cadence of a professor during a business technology seminar. He describes how a company can lead a market disruption with new products, global education, brand leadership, and systems-solution selling. The results lead to increased productivity and profitability, and enhanced worker and environment safety in chemical and biologic manufacturing.
But is Corning the right company to lead a reactor revolution in the biopharma industry?
“Corning Life Sciences is approximately a $1 billion business in revenue versus $10 billion 2014 total company revenue,” says David Morse, chief technology officer and executive vice president, Corning Incorporated. “The biopharma market segment accounts for roughly 50% of Corning Life Sciences sales, and is a growing opportunity for us.”
That $1 billion doesn’t include Corning Advanced-Flow reactors (AFR), a product line residing in its Emerging Innovations Group. The AFR technology originates from Corning’s European Technology Center just outside of Paris, but the significant market action right now is in China and India. That’s where greenfield facilities and plant modernization by the biopharma and fine chemical industries offer the best opportunity to dethrone the long-held leadership of traditional micro, or batch, reactors.
How To Dismantle A Reactor
In February, Corning announced that Medichem S.A. (Spain) demonstrated commercial-scale continuous-flow production for an organometallic-compound API using a Corning Advanced-Flow (G4 silicon carbide) reactor. Medichem switched to flow reactor technology because of concerns current micro reactors would present dramatic yield reduction at every scale-up. The two companies used “a rapid and smooth program-phase approach to develop a process challenged by conventional technology, and enabling profitable commercial manufacturing.”
According to Jiang, some customers keep their adoption of new technologies confidential so as not to tip off the competition. But Medichem, a CMO, has an interest in promoting its capabilities. That most flow technology and continuous manufacturing equipment is adaptable – Corning’s is built on a module design – allows the utilization of flow reactors for myriad CMO client needs, or any biopharma manufacturer’s internal pipeline.
Corning demonstrates capabilities in hands-on testing laboratories around the globe. “We set up a reactor here in China and have run over 100 different chemistries without significant changes other than module settings,” says Jiang. “Once you understand the principle, it’s easy to reconfigure for your next chemistry challenge.”
This is more than a point of promotion; it touches on questions of evolving industry trends. For example, with a de-emphasis on blockbusters and more attention to orphan drugs – and the advent of personalized medicine – is there an increasing future need for continuous flow technology? Jiang says that the sheer volume of API may be reduced for some drugs, but the variety of chemistries is widening, and growing more complicated. As mentioned above, flow-technology is more adaptable than the fixed batch-reactors of today. However, there are other – perhaps competing – technologies being advanced to address product variability and complexity, including single-use technology.
Single-use manufacturing systems are promoted as further reducing potential product contamination risks. They match up well with trending therapeutic focus, most specifically oncology. Perhaps we will see single-use as well as continuous-flow technologies aid ADC (antibody drug conjugate) platforms, and help with product variety, volume variances, increased potency, and the need for better capacity utilization.
Competition Between Technologies, Not Companies
For Corning, it’s batch vs. flow, not us vs. foe.
“It’s not a point of competition,” explains Jiang. “Other companies offer flow products of some kind, but I think today we all agree to join together to expand marketing and educate the industry about the new technology. If you have to call them competitors, okay, but companies appreciate Corning’s brand leading the charge so all players gain access to more customers.”
The real competition is between established and disruptive technologies. And like communications technology and the newest “apps,” Jiang knows it’s the next generation who will lead broad adoption. “The chemical industry in general is conservative,” he says, “and we are dealing with a mind-set change.” To promote that change there must be a focus on education.
“We set up a joint laboratory in Changzhou Chinese University and started familiarizing students. In a few years, we had graduates with master degrees based on training in this technology,” says Jiang. Corning also has a collaboration with the Massachusetts Institute of Technology (MIT) engineering department, where they have several flow reactors. “The first years we accumulated knowledge and grew the student base,” Jiang explains. “From around 2012, you’ll see an increase in scientific publications in this area, particularly generated by professor Jensen [Klavs F. Jensen, Warren K Lewis Professor and Department Head Chemical Engineering Professor Materials Science and Engineering].”
And as this inculcation and brand development takes place within the coming generation, the “elders” in the biopharma industry gain confidence in the technology from the recognition of the established Corning brand.
Perhaps being of that “elder” generation who knows the brand – fiber optics for communications, “Gorilla” and advanced glass for displays of all kinds, advanced industrial-use ceramics – I was still surprised to learn about leadership in biopharmaceutical technology. I shouldn’t have been. Jiang points out, for example, that it’s the company’s historic strength in glass and ceramics providing the materials in its advanced reactors.
Corning has five categories of reactors, and has announced a new product to address photochemistry. AFRs can handle high pressures, and operate at 18 bar and 200 C or -60 C. Further advancements are coming in compatibility with the harshest chemicals, such as HF (hydrogen fluoride).
And seeing is believing for all generations. “The transparence is favorable to all chemists,” says Jiang. (Engineers don’t mind visibility, either.) “This is a chemist-friendly design serving as a technological bridging function. Chemists use glass from the day they enter the labs, then suddenly have to deal with metal batch-reactors to advance a program. Along with everything else, they can’t see inside with their own eyes.”
The Sales Flow
AFR commercial activity started in Europe in 2006. Jiang points particularly to an initial and key (publicized) sale in Austria to Royal DSM. From around 2010, Corning started shifting to their current global sales strategy, particularly for extending into China, India and developing countries.
Corning doesn’t disclose number of installations, but Jiang says, “I can say we are in a very good mood. China holds a strong market leadership position. Other Asia countries like Korea, and of course Japan, are active. We’re also encouraged by the U.S. market as well as by our European customers.”
Corning’s demonstration labs are important to the sales process. Their primary focus is “to show the customer the technology, products and engineering services.” In some cases, potential customers can experiment with their own chemistry in these labs. “We do what we call a QFT – quick feasibility test – which has proven to be a successful promotional program for us,” says Jiang.
He also emphasizes that Corning is a “solutions provider.” The chemistry and engineering services that go along with a sale are vital to many customers. Corning has hundreds of PhD-chemists and chemical engineers available to assist. “We look at it as comprehensive system-level service plus the products,” says Jiang.
What about price? Jiang says Corning has made systematic cost comparisons, particularly in categories such as hydrogenation and nitration. “Our findings show significant advantage both in Capex [capital expenditure] and Opex [operational expenditure].” He says all chemistry is different; in some direct reactor-to-reactor comparisons, an advanced flow reactor might have a higher cost than a batch reactor. “However, if you consider solvent usage reduction, yield improvement, simplification of downstream challenges, avoidance of scale-up costs and pilot plant investment – if you look at the whole investment cycle – we are confident of a significant reduction in cost for both Capex and Opex.”
Batch Reactors As Obsolete?
Will we see flow technology completely replace traditional glass-lined, Hastelloy and other steel reactors? Jiang says he fields this question often; his answer is measured: “Based on accumulated knowledge and experience, it’s safe to say now about forty to fifty percent of chemistry can be realized in this technology.” He offers that the level of benefit varies, and there are some chemistries – including for larger solids, and/or intrinsic slow kinetics – still better left to batch reactors.
There are outside forces moving the biopharma industry – which some say lags behind other chemistry-related industries – to continuous production techniques. These include growing concerns about environmental impacts. For one thing, newer technologies generally reduce the amount of solvents and other chemicals needed to clean and run reactions in traditional batch reactors. Global regulatory authorities for the most part are on record as advocating for continuous-flow production to become mainstream. Says, Jiang: “We’re being looked at by society as a help in moving the industry in environmentally sustainable and green-chemistry directions.”
Finally, there are other large vendors in this field, and like with most technologies, competition will continue to emerge … and grow the market. But right now Corning lends an important brand validation and assurance of commitment, investment-wise as well as technological. This has many groups looking to Corning as a key player in overcoming hurdles to a steeper adoption curve of advanced flow technologies in the biopharmaceutical industry.