Calculating Process Control ROI For Improved Costs And Timelines
By Jason Dickens and Mike Ponstingl
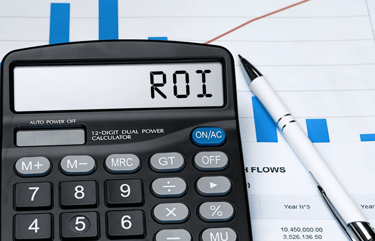
Incorporating process analytical technologies (PAT) into a biopharmaceutical manufacturing paradigm can save companies time, resources, and costs. The degree of savings a biopharma can expect from adopting PAT can vary widely and depends upon several factors, from the scale of a process to the value of a drug product, and understanding how multifaceted variables interact to influence PAT selection can help companies identify technology solutions that maximize both quality and cost efficiency.
The primary goal of PAT is to mitigate the risks associated with gaps in data and process understanding. While its widespread deployment across the space has primarily been the result of a drive toward improved product quality, the financial advantages PAT can offer individual companies have largely been ignored. Calculating the return on investment (ROI) for these technologies is integral to establishing a true understanding of the value of PAT as part of an overarching business strategy.
Benchmarking an existing process, evaluating its pain points, and identifying the PAT that best addresses them is particularly important for biopharmas working with increasingly expensive-to-produce drug substances and product.
Adopting a ‘Risk-Forward’ Approach in a Risk-Averse World
One of the most valuable assets a biopharmaceutical company possesses is time; managing the timelines that attend its manufacturing activities is crucial to ensuring long-term success. Adopting PAT can help companies save time both in straightforward ways – most in-line, on-line, or at-line monitoring technologies take seconds or minutes to yield data and result outputs, compared to the days or weeks typical of traditional offline monitoring methodologies. Indirect savings, such as batch loss prevention via sufficient real-time process controls, are also often realized through PAT approaches.
Batch loss has become increasingly high stakes for the biopharmaceutical space, as new biologics and cell and gene therapies gain greater market acceptance. Determining the root causes of batch loss, as well as their historical frequency in a manufacturing process, can help companies conceptualize the magnitude of cost savings that new monitoring technologies may afford their operations. Multiplying this across equipment and sites as a program scales further expands the benefits of PAT to transform a company’s flexibility and adaptability in response to market demands and pressures.
Despite the numerous advantages PAT may afford a process, many companies can be reluctant to employ these technologies. This is often a function of risk aversion, coupled with the heavy lift that typifies overhauling processes and procedures to accommodate new manufacturing technologies that enable adaptive process control. Yet being “risk forward” in adopting PAT is critical to maximize its utility; often, the required “process stretching” that accompanies a holistic PAT evaluation can help manufacturers pinpoint previously unidentified sources of product loss or impact on product quality attributes.
Achieving Sustainable, Fit-for-Purpose Monitoring
Another important consideration when performing an ROI evaluation for PAT relates to sustainability of supply. Technologies that require a wealth of resources and personnel to install, maintain, and utilize are understandably, more difficult to sustain over a product’s entire life cycle, negatively impacting ROI in turn. To address this, companies must perform road mapping in conjunction with other benchmarking and ROI evaluations to determine whether they can reasonably expect to maintain a PAT in the long term.
This issue can be particularly cumbersome for companies that opt into technologies over-engineered for their purposes – purchasing a technology for one line that costs hundreds of thousands of dollars can represent a large expenditure for a nascent company. Multiply that cost over several lines or manufacturing sites added over multiple years and what was initially a moderate expenditure can become a multimillion-dollar investment. Conducting a fit-for-purpose evaluation as part of determining ROI can help companies identify more cost-effective technologies that can achieve their goals, greatly reducing the upfront costs that can accompany other technology platforms.
One of the biggest benefits of incorporating new PAT into an existing process is the reduced analytical burden and reduced resourcing. Examples of this include balancing single-use technology adoption with supply chain assurance and how these variables impact PAT, as well as how complementary PAT such as those integrated with rapid ID technologies can serve to bolster that supply chain assurance. This is particularly important as manufacturing paradigms scale; more production requires a larger, more diversified supply chain, increasing the potential for manufacturers to receive the wrong materials.
Ultimately, both real-time release and process control PAT give manufacturers the ability to measure the throughput and robustness of their processes, improving scheduling, readiness assessments, and forecasting. With more than 40 years of experience across multiple industries, Custom Sensors and Technology (CST) has established itself as a leading provider of robust, fit-for-purpose PAT and accessories. CST has a wealth of experience in providing establish technologies, as well as designing sensors and monitoring systems tailored to a client’s unique specifications, affording seamless integration with existing systems and software. By approaching each application with the goal of providing PAT that achieves the right level of complexity at the right price, CST offers its customers the latitude to target specific improvements, learn more about their processes, and achieve the optimal PAT strategy for their goals.