Biopharma Cold Chain Logistics 101
By Curtis Gippe, Director of Life Sciences, Adept Packaging
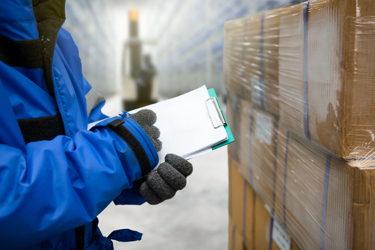
Cold chain logistics can be complex and intricate. Maintaining the integrity of controlled-temperature products requires holistic consistency between design and development, manufacturing and packaging, qualification and validation, cold storage, transportation, and monitoring as the product moves from its point of origin to the end user while facing ever-changing conditions.
To successfully create and maintain a system that controls product temperature throughout its distribution environment, you’ll need to evaluate the impact of each stage on the entire cold chain solution.
Design And Development
Design and development of cold chain solutions generally start early in the product development cycle. Products are tested over a wide range of temperatures – sometimes referred to as temperature excursion studies or target temperature profiles for drug products – to build an understanding of how they degrade. Ranges considered safe may shift multiple times during the product development cycle until the development team narrows in on the optimal temperature range for the product.
An understanding of this process and its outcome is essential for planning each subsequent step in the cold chain, beginning with package development. The package design must be robust enough to protect the product against any temperature excursions it might encounter as it moves through its distribution environment.
Packaging Process Interactions
The many interactions between components, materials, and processes involved in controlled-temperature products are a big reason why developing a cold chain solution is complex. It’s important to understand how those interactions impact the packaging’s performance. For example, packaging processes such as hermetic sealing, heat sealing, and radiation sterilization can increase the core temperature of the product and affect its stability.
Involving packaging engineers early in the design stage provides an opportunity to introduce in-process solutions such as custom dies and tooling, as well as work-in-progress cold package systems to protect the product even before it is packed and shipped through the supply chain.
Qualification And Validation
Packaging also plays an important role in the successful qualification and validation of a cold chain solution, ensuring the product meets regulatory requirements. Having an engineer on your team with regulatory expertise will help maintain a holistic perspective on the cold chain system and avoid potential issues down the line. Regulatory requirements can be complex because they may involve compliance with regulations from multiple regions and additional complications stemming from the use of hazardous materials such as dry ice and liquid nitrogen for cooling.
Design Verification And Validation
Process validation for cold chain packaging, storage, and distribution is required for the regulatory submission of any pharmaceutical, biological, or medical device product. This validation requires expertise in stability testing and thermal packaging qualification, each of which require knowledge of a variety of packaging standards issued by organizations such as ASTM and ISTA. It also requires qualification of freezers, thermal containers, and other cooling equipment.
You’ll need to evaluate the entire distribution environment, including temperature mapping for shipping routes, and the equipment used to keep products within their predetermined temperature range.
Cold Storage
A thorough cold chain solution considers not only the varying conditions found in the distribution environment but also the optimal pre-shipment storage conditions. Maintaining the product’s temperature from the production line to the end user starts with cold storage and, depending on a variety of conditions, products may remain in this initial cold storage stage for a little as a few hours to several days.
Cold storage solutions include some combination of freezers (for temperatures below 0°C), refrigerators (for temperatures from 0°C to 15°C), or environmental chambers that can maintain ambient or room temperatures. Validation of all equipment involved in the storage phase, either as stand-alone equipment or as part of a system, is a crucial piece of a holistic cold chain solution because it represents the last step before a controlled-temperature product is shipped out of the facility.
Transportation
Cold chain transportation systems utilize various temperature control solutions to keep the product within the range determined during the design and development stage. These solutions can involve either passive or active temperature controls, and knowing which is right for your product requires an understanding of the methods that will be used to ship it.
Passive temperature control solutions do not include a continuous cooling mechanism to keep the product within its predetermined temperature range. For this reason, passive solutions are typically used for products that will be shipped quickly, such as overnight shipping for single parcels. Passive control solutions usually include packaging with multiple insulating layers and a starting temperature at the low end of the product’s temperature range. Preconditioning these shipments is of paramount importance to ensure the product maintains its predetermined range throughout its shipping duration.
Active temperature control systems, on the other hand, include a continuous cooling mechanism to maintain a temperature within the product’s predetermined range. These continuous cooling systems involve coolant materials, electrical cooling equipment, or a combination of the two throughout the distribution cycle. These solutions are energy intensive and are typically reserved for larger product loads in specialized shipping containers and temperature-controlled trucks and ships.
Monitoring
For each stage of a cold chain system, monitoring plays an important role in ensuring the entire system is functioning properly and that the product remains within its predetermined range between manufacturing and use at the end of its life cycle. It plays an important role in verifying that the product remained within that range and identifying any points at which the product’s temperature may deviate from its optimal temperatures.
Thorough monitoring and data capture also helps to ensure that problems in the system are identified and resolved before they impact product safety and expose the business to risk. This also helps to identify anomalies and investigate the root cause of potential issues, especially for products exchanged between CMOs and secondary and tertiary logistics providers (2PL/3PL).
Advances in cold chain technology, coupled with increasing trends in direct-to-consumer shipping, mean cold chain solutions play a growing role for many life sciences brands. Designing and maintaining a system that protects a product from manufacture through delivery requires an in-depth understanding of each stage of the cold chain and how those stages depend on each other to ensure product safety throughout the distribution environment. Because this system depends on the integrity of each stage and may involve CMOs and a variety of logistics vendors, it is important to have specialized oversight of the entire process. Understanding the cold chain and each stage of the distribution environment can ensure the entire system functions as designed, and your product arrives safely in the hands of consumers and healthcare providers.
About The Author:
Curtis Gippe is the director of the life science practice at Adept Packaging. He has more than 15 years’ experience in packaging design and development for pharmaceuticals, medical devices, and consumer products.