Big Data And AI In Pharmaceutical Development & Manufacturing — An Inside Look
By Jerry Martin
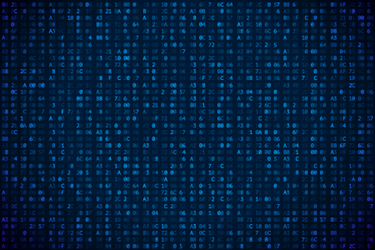
New technologies can lower costs, speed up production, and improve research and development
With the explosion of health-related data in recent years, pharmaceutical companies are looking to Big Data to reduce costs in research and development and manufacturing. The market for artificial intelligence (AI) in drug development, valued at $200 million in 2015, ballooned to $700 million in 2018 and is predicted to value more than $5 billion in 2024, according to a report by Big Data Analytics.1
One of the reasons for this rapid growth is improved capabilities in generating and harnessing data. Many pharmaceutical manufacturing systems already embed data in process development and optimization, connecting to the Internet of Things (IoT) on the factory floor. However, having integrated platforms for smart devices can enhance the accuracy and implementation of data throughout the life cycle — from research to manufacturing to the point of purchase and beyond (including patient monitoring).
AI and Big Data have the potential to lower the cost and time of drug trials, to better determine patient outcomes with established drugs, and to better design new drugs. Computer software and algorithms can provide better analytics before and during the manufacturing processes and stimulate insights to fuel better decisions in the pharmaceutical industry.
Monitoring Manufacturing
Over the last few years, the FDA has encouraged companies toward continuous manufacturing and away from the step-by-step approach of batch processing. By continuously monitoring manufacturing processes and collecting feedback, pharmaceutical companies can monitor factors like temperature and moisture change, therefore reducing variability in the final product and patient outcomes, through a method called process analytical technology (PAT).
Continuously testing drugs through the production process using PAT is more efficient and cost-effective than batch testing, particularly when synthesizing biological proteins at millions of dollars per batch. By better monitoring pharmaceutical manufacturing process operations, we can potentially predict performance and reduce variability in clinical outcomes. Applying AI to performance and feedback response data generated with PAT can be used not only to control manufacturing processes, but also to improve them through automated machine learning.
In the case of biopharmaceutical production, companies can capitalize on Big Data by employing logistics in operations. Manufacturing biopharmaceuticals require the use of living genetically engineered cells. Production teams monitor for more than 200 variables to ensure consistency and purity. Two batches of a particular substance produced using an identical process can exhibit a variable yield of between 50 and 100 percent, creating issues with capacity, product quality and regulation adherence.
A McKinsey report described how a top-five specialty chemicals manufacturer used Big Data to significantly increase vaccine production yield. The company gathered data from its production process in groups of related activities and entered it into a central database. The team then applied statistical analysis to determine interdependencies and sensitivities that had gone unnoticed. The manufacturer then made targeted process changes and was able to increase its vaccine yield by more than 50 percent — saving between $5 million and $10 million per year on production of a single substance.2
Track And Trace
The industry-wide serialization mandate also complements data integration efforts. FDA-required barcodes necessitate the pharmaceutical industry consider data and utilize software for coding product, creating a system wherein packaging operations rely on data for distribution. Serialization mandates that pharmaceutical companies modify their internal operations to be more data compliant, so an outside organization may also read and recognize their data. Data transparency could open pathways to new trends and best practices but presents many challenges due to the proprietary nature of this information.
Additionally, data gathered from serialization can have applications in drug development and patient adherence. Non-adherence poses risks to patient safety and financial burdens to the healthcare system. Lack of adherence is estimated to cause nearly 125,000 deaths and 10 percent of hospitalizations annually and costs the healthcare system between $100 billion and $289 billion per year.3
In response to this challenge, some companies level up their track and trace applications by serializing drugs down to the pill. In 2017, the FDA approved the first drug with a digital ingestion tracking system. Abilify MyCite, a medication for patients with schizophrenia, has an ingestible sensor embedded in the pill to record medication consumption. It works by sending a message from the pill’s sensor to a wearable patch. The patch then transmits information to a mobile application so that patients can track the ingestion of the medication on their smartphone. Patients may allow their caregivers and physician to access the information through a web-based portal.4 This practice could be a huge step towards solving the national medication adherence crisis.
Research And Development
Big Data and AI show promise in reducing the time and cost of pharmaceutical R&D as well. Billions of dollars are invested each year into the discovery and development of new medicines, but it usually takes 10 to 15 years for a medicine or vaccine to evolve from discovery to commercialization. Manufacturers invest a huge amount of capital long before seeing any return, which means they must allocate a high percentage of budget to R&D. Big Data Analytics reports that the fail rate for clinical trials is 92 percent and drug companies spend an average of $2.6 billion developing a single drug.1
When a pharmaceutical company invests in R&D, it screens 5,000 to 10,000 chemical or biological compounds to find one that exhibits potential for treating new or existing conditions, according to the white paper “Five Factors Spur Growth in Pharmaceutical Packaging and Processing Equipment,” produced by PMMI, The Association for Packaging and Processing Technologies.5 There is also risk associated with investing in R&D for a drug if it fails to meet regulatory approval.
Using Big Data to better design clinical trials and predict outcomes makes it commercially feasible to develop drugs for smaller patient populations. Pharmaceutical manufacturers collect data on patient responses to drugs during the clinical trial process. Combining that data with AI will enable them to determine which aspects of a patient subpopulation are associated with responses to drugs.
Looking Ahead
Despite the many benefits of Big Data, incorporating it into manufacturing processes poses some challenges. Companies need to be prepared to handle the volume of data, the speed at which it accumulates, and organizing it best to create a more detailed future.
For manufacturers seeking to improve production with Big Data, the first step is to determine how much useful data the company already has at its disposal. Companies that collect process data for tracking purposes, not as a basis for improving operations, may invest in systems or third-party analysts to organize and then use that existing information to improve operations. Other companies have too little data available to draw statistical conclusions. The challenge then becomes exploring practices to collect more data.
Researchers recognize that it would be valuable for companies to share data and learning with others who can apply it to improve the safety and reliability of all manufacturing. But the competitive nature of the pharmaceutical industry means that all information is propriety, and developing an open source system can be complicated, as companies use different technology platforms. A standardization process would have to be developed. Such a solution may be possible, however, as organizations like the Allotrope Foundation, a worldwide coalition of scientists with a mission to improve data access and integrity, are seeking to revolutionize the way we acquire, share, and gain insights from scientific data.6
Conclusion
While the industry is in the early stages of applying electronic data to manufacturing processes, harnessing new capabilities can lead to a better understanding of drug structure and function that ultimately impact patient outcomes. Big data, AI, and machine learning have the potential to change the way we develop, monitor, manufacture, and apply drugs.
References:
- http://analytics.dkv.global/data/pdf/AI-for-DD-Q2/Available-for-Purchase/Infographic-Summary-Advanced-R&D-and-Drug-Discovery-2018-Q2-Sample.pdf
- https://www.mckinsey.com/business-functions/operations/our-insights/how-big-data-can-improve-manufacturing
- https://www.nacds.org/news/the-cost-of-medication-non-adherence/ https://www.fda.gov/newsevents/newsroom/pressannouncements/ucm584933.htm
- https://pmmi.org/report/2018-pharmaceutical-packaging-processing-white-paper
- https://www.allotrope.org/
About The Author:
Jerry Martin is an independent consultant to pharmaceutical manufacturers and equipment suppliers for filtration, single-use manufacturing, marketing, business development, and regulatory compliance. He was previously SVP, marketing and global scientific affairs, for Pall Life Sciences, where he served the pharmaceutical, biotech, medical device, and vaccine industries for over 37 years. He is currently chairman emeritus of the Bio-Process Systems Alliance, the single-use manufacturing trade association, and a member of the USP Expert Panel on Plastic Systems Used for Manufacturing Pharmaceutical Products. He holds an M.Sc. in microbiology from the University of Toronto.
Healthcare Packaging EXPO (Sept. 23-25; Las Vegas Convention Center), co-located with PACK EXPO Las Vegas 2019, will provide a powerful opportunity for pharmaceutical and medical device manufacturers to converge and address evolving consumer and regulatory demands. Both owned and produced by PMMI, the shows will also offer educational programming and opportunities to cross-pollinate ideas among industries. Register and learn more at https://www.hcpelasvegas.com/