Best Practices For Raw Material Supplier Change Notifications: New BioPhorum Guidance
By BioPhorum
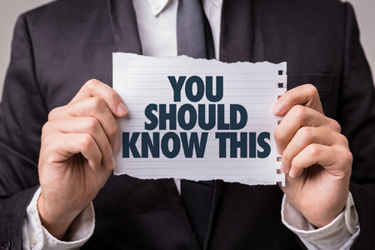
Change notification is an integral and often frustrating component of biopharmaceutical manufacturing. Managing the large volume of supplier change notifications (SCNs) while safeguarding the continuity and compliance of a highly complex and tightly regulated supply chain is a tremendous, resource-intensive task. Often, the information initially provided by suppliers is inadequate to ascertain the scope of the change and its impact on the pharmaceutical product. On the supplier side, meeting a myriad of requests for more information from end users is an equally time-consuming and burdensome undertaking that drains resources and may result in implementation delays.
To address the challenges on both sides of the industry, the BioPhorum Raw Material Variability Workstream has developed a guidance document designed to streamline the process without straying from essential and strict risk mitigation procedures. This article summarizes that guidance document, which categorizes relevant change areas and illuminates the type of changes the biopharmaceutical industry needs to be informed about.
Ensuring Supply Continuity In Biopharma
The COVID-19 pandemic has poignantly illustrated the vital importance of continuity in the supply chain. In the pharmaceutical industry, any disruption in the supply chain has the potential to significantly impact the business in a commercial sense, resulting in lost revenue and, more importantly, to delay the delivery of potentially life-saving medications to patients. As in all things, change is inevitable in the supply of raw materials. Thus, effective management of the inevitable changes to product and process is vital to ensuring a reliable supply. At all points in the inbound supply chain, procedures for the timely notification of downstream users of planned and unplanned changes occurring in the supplier’s raw-material manufacturing process are crucial. Such changes are typically defined as anything that could potentially alter the quality of the raw material or the manufacturer’s product (and therefore patient outcomes), including availability or manufacturability of the material.
Additionally, given necessary regulatory requirements, all changes must also be evaluated for their prospective impact on raw material information included in product licenses. At times, notification to regulatory agencies will be required. In such cases, additional supplier information and more time may be needed to implement a change, for example, to build up safety stock. For all changes, developing and implementing mitigation activities is compulsory. Ensuring supply continuity and minimizing the impact of changes is a complex task that requires shared responsibility among all factions in the supply chain.
BioPhorum’s newly developed guidance document is not intended to replace the timely reporting of quality issues or deviations, which may result in a permanent change, or processes for Corrective and Preventive Action. Instead, it aims to develop a standardized process, to the degree possible, to support change notifications and to streamline the process by homing in on the important information thereby reducing the amount of additional non-value-added work currently experience by many in the industry.
Changes Biopharma Needs To Know About: Key Areas
Any efforts to standardize and streamline change notification processes would be incomplete without an understanding of the types of changes the biopharmaceutical industry needs to be aware of. These can be distilled into eight key areas:
- Manufacturing plant or environmental conditions, including:
- The addition/deletion of production plants or sites
- Changes in animal-free status
- Changes in the manufacture of hormones, cytotoxins, and/or antibiotics on site
- Manufacturing process, equipment, and tooling, including:
- The addition of production lines
- Changes in the manufacturing process
- Changes to cleaning/change-over processes that impact bovine spongiform encephalopathy (BSE)/ transmissible spongiform encephalopathy (TSE) risk
- Installation of new equipment that requires validation
- Changes to allergens used in manufacturing
- Changes to a direct processing material or chemicals
- Materials or supply base, for example:
- Changes to or addition of supplier, sub-tier supplier, outside, or contract manufacturers
- Changes in source of material
- Changes that affect the physical properties of material
- Changes in sub-contractors
- Changes initiated at sub-contractors
- Changes in materials used or in its specification
- Changes in either the class or type of residual solvents or in catalyst use and potential catalyst residues
- Use of a recycled material or changing mixing ratios/times
- Inspections and tests, including:
- Changes to raw-material sampling methods that increase risk of contamination
- Changes to final inspection plans
- Changes in sub-contractors for testing
- Changes in retest period
- Changes to quality tests
- Packaging, storage, and labeling, including:
- Changes in nomenclature/naming
- Changes to material ID codes
- Changes that could affect storage conditions of products or shelf life
- Changes to packaging specifications or quantities
- Changes to transportation methods or conditions
- Changes to physical location of repackaging/warehouse/storage areas
- Changes in packaging quantities or pallet sizes
- Labeling changes
- Changes to packaging containers/materials and their specifications
- Reversal
- Change cancellation
- Naming and nomenclature
- Obsolescence
Table 1 shows the base information required by end users for all proposed supply chain changes. The guidance document also provides detailed information on a host of additional data requirements for specific situations at each stage of manufacture, including changes in the location of the manufacturing plant or transfer of manufacture to another organization as well as changes in the environment within current facilities, such as humidity, temperature, and the presence of potentially harmful materials (e.g., antibiotics, animal-derived materials).
Table 1. Data end users should include for all proposed changes.
Transforming the process of supply change notification begins with understanding the changes biopharmaceutical industry end users need to know about and the specific information required. As other industries have shown, taking this necessary step diminishes the amount of rework required and the time taken to process change requests. Reduction in the variability in demand patterns is another anticipated benefit as end users refrain from building extensive inventories to mitigate against the perceived risks that ensue from proposed changes. Given the nature of biopharmaceutical manufacturing, full alignment and standardization on the information that should be provided for changes is not possible. Nonetheless, adopting more robust alignment on the usual information required can be expected to substantially improve the current state of change notifications in the biopharmaceutical industry.