Are CDMO Partnerships The Answer To Manufacturing Capacity Issues?
By Tom Oakley, Springboard Pro
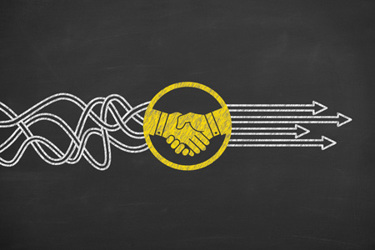
The demand for weight management drugs, such as GLP-1s, has put immense pressure on manufacturing capacity.1 The shortage of available manufacturing capacity threatens to delay product launches and limit access for all injectable medicines as more pharmaceutical companies race to launch new drugs and devices for patients.
The manufacturing strain is exacerbated by the resource-intensive nature of scaling up the fill-finish of primary drug containers, and the manufacture of drug delivery devices, which often require specialized machinery, regulatory compliance, and rigorous quality control. The acquisition of Catalent by Novo Holdings for $16.5B in February 2024 demonstrates the value placed on manufacturing capacity.2
Bridging The Capacity Gap: Global Supply Chain Considerations
As global demand for pharmaceutical products continues to rise, manufacturers face mounting pressure to ensure they have the necessary production capacity to meet market needs. This challenge is compounded by an increasingly complex geopolitical landscape, where trade tensions, supply chain disruptions, and evolving regulatory requirements threaten the stability of global pharmaceutical supply. As a consequence, there is an urgent need for adaptable, scalable production solutions that can accommodate fluctuations in demand while ensuring consistent product availability.
To address this challenge, manufacturers must invest in advanced manufacturing facilities strategically located in key regions such as North America, Europe, and China. These facilities must not only be capable of handling high-volume pharmaceutical and medical device production but also be agile enough to adapt to shifting market conditions. The emphasis on localized manufacturing has never been more critical, as nations introduce tariffs and trade restrictions to protect domestic industries. A robust, regionally distributed supply chain reduces dependence on volatile global logistics networks, enhances supply chain resilience, and supports sustainability initiatives by minimizing transportation-related carbon footprints.
Beyond geographical considerations, manufacturers that commit to excellence at every stage of production — ranging from component sourcing to final assembly — will be better positioned to navigate these evolving challenges. Quality assurance and regulatory compliance are paramount in the pharmaceutical industry, where even minor inconsistencies can lead to costly delays or product recalls.
Partnering With A CDMO Is The Answer
For pharmaceutical executives, securing long-term partnerships with manufacturing firms that emphasize quality, scalability, and speed is essential. These partnerships provide a pathway to rapid expansion while mitigating the risks associated with production bottlenecks, regulatory hurdles, and market fluctuations.
With capacity becoming a key differentiator in the pharmaceutical landscape, companies must shift their strategic focus. Traditionally, pharmaceutical firms have prioritized innovation, striving to develop groundbreaking treatments. While innovation remains crucial, it must now be balanced with pragmatic production capabilities. A promising drug or device can only succeed if it can be manufactured at scale while maintaining quality and affordability. This requires collaboration with manufacturing partners that offer not only capacity, but also expertise in navigating regulatory complexities, ensuring consistent production standards, and delivering user-friendly designs that meet the expectations of both healthcare providers and patients.
Engaging manufacturers early in the design and development process is critical to ensuring a seamless transition from concept to commercialization. Early collaboration facilitates design optimizations, streamlines regulatory approvals, and prevents costly modifications later in the production cycle. Open lines of communication between pharmaceutical companies and manufacturing partners are more vital than ever, particularly as supply chain vulnerabilities and raw material shortages continue to impact the industry. By fostering strong, transparent relationships, companies can proactively address potential challenges and accelerate time-to-market.
The surge in demand for pharmaceutical manufacturing capacity is also driven by the growing prevalence of injectable therapies. This reflects a broader industry shift toward biologically derived treatments, including monoclonal antibodies, RNA-based therapies, and personalized gene editing. While oral medications remain foundational for many treatment regimens, the continued rise of injectables underscores the need for sophisticated manufacturing capabilities that support aseptic processing, complex formulation handling, and precision device integration. Manufacturers must be equipped with state-of-the-art technology and expertise to meet the stringent sterility, stability, and safety requirements associated with these advanced therapies.
In this evolving landscape, contract development and manufacturing organizations (CDMOs) play an essential role in bridging the capacity gap. CDMOs offer end-to-end support, helping pharmaceutical companies navigate the complexities of a constrained capacity environment. By integrating patient-centric device design with agile, scalable, and high-volume manufacturing solutions, CDMOs enable pharmaceutical firms to maintain competitive advantage. Their expertise in regulatory compliance, process optimization, and risk mitigation ensures that products are not only market-ready but also positioned for long-term success in an increasingly demanding industry.
Ultimately, securing sufficient manufacturing capacity is no longer just an operational consideration, it is a strategic imperative. By prioritizing local production capabilities, fostering strong manufacturing partnerships, and investing in scalable solutions, pharmaceutical companies can safeguard their supply chains, enhance market responsiveness, and drive sustained growth in an unpredictable global landscape.
References
- J.P. Morgan doubles GLP-1 market projection to $71B in 2032.
- Novo Holdings to Acquire Catalent | Catalent Pharma Solutions
About The Author
Tom Oakley leads engineering and scientific teams developing new injection devices, pumps, and inhalers at Springboard Pro. He has been the named inventor on dozens of patents throughout his 25 years’ experience in the industry. His most recent work focuses on developing robust device strategies and plans for a wide range of clients from large multinationals to dynamic startups. He was a Reader in engineering at Cambridge University and was the Choate Fellow in Human Physiology and Pathology at Harvard University.