An Analysis Of MHRA's Latest Annual GMP Inspection Deficiencies Report
By Barbara Unger, Unger Consulting Inc.
The U.K.’s Medicines and Healthcare products Regulatory Agency (MHRA) has taken a different approach in the publication of the GMP deficiencies for drug product issued during inspections in 2018 and 2019. In 2015 and 2016, the MHRA provided approximately a 100-slide deck each year with tables, figures, and text from deficiencies against the requirements in the chapters and annexes. No data were formally published for 2017. The MHRA published a 6,200-plus line Excel spreadsheet of its 2018 GMP inspection data so that individuals could parse and present the data according to their needs. Last year we published analysis of the data in a two-part set of articles: “An Analysis Of MHRA's Annual GMP Inspection Deficiencies Report” and “The 10 Most-Cited MHRA GMP Inspection Deficiencies By Annex/Chapter.”
The 2019 data were provided in October 2020 in a just under 5,300-line Excel spreadsheet, and this year we again present the data in two articles. The first article begins with a high-level overview of the 2019 data, including trends from the four most recent MHRA reports, from 2015, 2016, 2018, and 2019. It proceeds to identify and evaluate the critical and major deficiencies from 2019, identifying the chapters and annexes associated with 137 critical deficiencies and the chapters and annexes most frequently associated with the 1,999 major deficiencies. Similar to the results in 2018, the most frequently cited chapter and annexes in 2019 are Chapter 1, Quality System, and Annex 1, Manufacture of Sterile Medicinal Products. For critical deficiencies citing Chapter 1 and Annex 1, the specific paragraphs and requirements with which they are associated are identified.
Part 2 will look in more detail at the most frequent citations in each of the top 10 chapters and annexes.
Background
Here is how I parsed the data from the MHRA spreadsheet. Each row in the spreadsheet is treated as a unique deficiency, regardless of whether it is a “deficiency” or a “sub-point” as identified in the Notes and Guidance section of the MHRA publication. I cannot discern which is which in the spreadsheet, so I treat them all equally. The summary data from 2015 and 2016 are taken directly from the MHRA 2016 report. Data were not posted for 2017. Any mistakes in this analysis and reporting of the 2018 and 2019 data are mine, not the MHRA’s.
Overall Data
The MHRA conducted a total of 258 inspections in 2019, a decrease from the 285 inspections conducted in 2018. The number of inspections has decreased since 2016. Insufficient data are available to determine if the inspections outside the U.K. decreased because of the Mutual Recognition Agreement with the FDA. For example, only five inspections were conducted in the U.S. in 2018, and the 2019 inspections outside the U.K. were not identified as to the country.
Table 1 identifies the number of drug GMP inspections, by country, performed by the MHRA in 2015, 2016, 2018, and 2019. As in past years, almost all MHRa inspections were conducted in the U.K. The percentage of inspections conducted in the U.K. in 2019 increased from previous years, and the percentage of overseas inspections decreased over the four years. In 2019, only 12 percent of inspections were conducted outside the U.K. Next year, when we receive the data for 2020, both inspections outside and within the U.K. will likely be far lower based on the travel limitations posed by the COVID-19 pandemic. In 2018, approximately 75 percent of inspections conducted outside the U.K. were performed in India. In 2019, MHRA did not provide a breakdown by country for the 12 percent of inspections that were conducted outside the U.K.
Table 1: MHRA Inspections by Geography
Table 2 shows the top 10 areas of all deficiencies from 2015, 2016, 2018, and 2019. Data from 2015 and 2016 are taken directly from the 2016 report published by the MHRA. Quality Systems leads the list in all four years. Notable features in 2019 include:
- The top six categories remain the same, and in the same order, as they were in 2018.
- All of the chapters and annexes in the top 10 for 2019 were among that same group in 2018.
- Quality System (Chapter 1) deficiencies exceed the number of deficiencies in the combination of the next two areas, Documentation (Chapter 4) and Production (Chapter 5). See the data in Figure 1.
- Computerized Systems (Annex 11) moved up one notch from 10th in 2018 to ninth in 2019 and Outsourced Activities dropped to 10th in 2019.
Table 2: Overall Deficiency Trend Comparison, Top 10
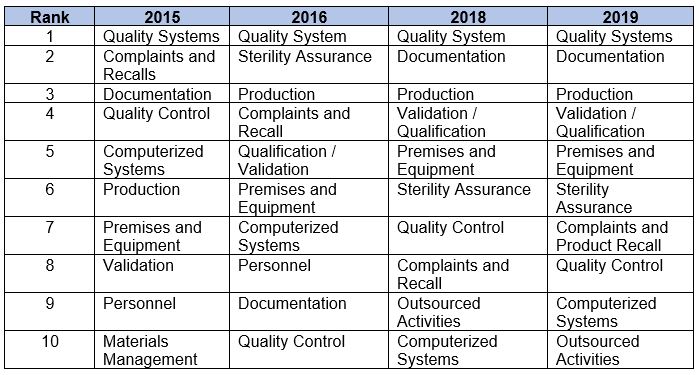
Figure 1 presents the total number of deficiencies identified in 2018 and 2019 for the top 10 combined chapters and annexes. These figures include all deficiency classifications – critical, major, and other. Figures 2 and 3 present the top groups for those, citing chapters and annexes, respectively.
Figure 2 shows that among the chapters, Chapter 1, Quality System, with just over 1,300 citations in 2019, has more than twice the number of deficiency citations as the next nearest chapter. Chapter 4, Documentation, with 700 deficiencies, is closely followed by Chapter 5, Production, with just under 600, and Chapter 3, Premises and Equipment, received almost 425 citations. Chapters 2, 6, 7, and 8 each had between 200 and 250 cited deficiencies. The remaining chapter, Chapter 9, Self-Inspection, had 30 citations.
The top six annexes cited in deficiencies in 2018 and 2019 are shown in Figure 3. Annex 15, Qualification and Validation, and Annex 1, Sterility Assurance, take first and second place among the most frequently cited annexes, respectively. This is followed by Annex 11, Computerized Systems, and Annex 16, Certification by a Qualified Person and Batch Release. All other annexes are associated with double-digit or fewer deficiencies.
Critical And Major Deficiencies
Table 3 provides a tabulation of all 2018 and 2019 deficiencies by their classification. Critical deficiencies constitute the smallest category; additional specific detail on these is provided later. Major deficiencies consistently constitute almost 40 percent of the total, and “other” deficiencies consistently constitute the majority at almost 60 percent of the total.
Most critical and major deficiencies cluster in a few chapters and annexes. Figure 4 shows the number of critical deficiencies identified in 2019 and the chapters or annexes that are referenced. Among the critical deficiencies in 2019, 34 percent are associated with Chapter 1, Quality System, and 23 percent are associated with Annex 1, Sterility Assurance. Annexes 1 and 11 are the only annexes that include citations for critical deficiencies; the remainder cite GMP chapters.
Figure 4 provides the specifics on the 11 most frequently cited chapters and annexes in critical deficiencies in both 2018 and 2019. Chapter 7, Outsourced Activities, and Chapter 8, Complaints and Product Recall, were cited among critical deficiencies in 2019 but were not cited in critical deficiencies in 2018.
Figure 5 shows critical deficiency data for 2019 and presents these by location, a U.K. site or in a site outside the U.K. Interesting this year is that the number of critical deficiencies for Chapter 5, Production, more than doubled from last year, and the vast majority of these deficiencies are cited for locations outside the U.K., when only approximately 12 percent of inspections were conducted outside the U.K. In total, Chapter 1 and Annex 1 top the list for both 2018 and 2019, with Chapter 5 coming in third. Annex 1 critical deficiencies in 2019 are identified exclusively in the U.K. It is worth noting that critical deficiencies citing Chapter 5, Annex 11, and Annex 15 were cited exclusively at sites outside the U.K. in 2019.
Figure 6 shows the critical deficiencies identifying Chapter 1 presented by the paragraph most frequently cited. Sections 1.4 and 1.8, taken together, comprise 77 percent of the critical deficiencies cited Chapter 1. Table 4 provides specific citations and more granularity on these two sections. Section 1.4 identifies the purpose and activities to be ensured by the quality system, and section 1.8 describes the basic requirements of GMP.
Table 4: 2019 Critical Deficiencies Cited in Chapter 1
Critical Deficiencies |
||
Paragraph |
# |
Short Version of Text |
C1.4(i-xvii) |
2 |
Please refer to the link above |
C1.4(vi) |
3 |
Arrangements are made for the manufacture, supply and use of the correct starting and packaging materials, the selection and monitoring of suppliers and for verifying that each delivery is from the approved supply chain; |
C1.4(vii) |
3 |
Processes are in place to assure the management of outsourced activities. |
C1.4(viii) |
4 |
A state of control is established and maintained by developing and using effective monitoring and control systems for process performance and product quality. |
C1.4(ix) |
2 |
The results of product and processes monitoring are taken into account in batch release, in the investigation of deviations, and, with a view to taking preventive action to avoid potential deviations occurring in the future. |
C1.4(x) |
1 |
All necessary controls on intermediate products, and any other in-process controls and validations are carried out; |
C1.4(xi) |
1 |
Continual improvement is facilitated through the implementation of quality improvements appropriate to the current level of process and product knowledge. |
C1.4(xii) |
3 |
Arrangements are in place for the prospective evaluation of planned changes and their approval prior to implementation taking into account regulatory notification and approval where required; |
C1.4(xiii) |
1 |
After implementation of any change, an evaluation is undertaken to confirm the quality objectives were achieved and that there was no unintended deleterious impact on product quality; |
C1.4(xiv) |
6 |
An appropriate level of root cause analysis should be applied during the investigation of deviations, suspected product defects and other problems. This can be determined using Quality Risk Management principles… Appropriate corrective actions and/or preventative actions (CAPAs) should be identified and taken in response to investigations. The effectiveness of such actions should be monitored and assessed, in line with Quality Risk Management principles. |
C1.8(i) |
2 |
All manufacturing processes are clearly defined, systematically reviewed in the light of experience and shown to be capable of consistently manufacturing medicinal products of the required quality and complying with their specifications. |
C1.8(iii) |
1 |
All necessary facilities for GMP are provided, including… |
C1.8(iv) |
1 |
Instructions and procedures are written in an instructional form in clear and unambiguous language, specifically applicable to the facilities provided; |
C1.8(vi) |
1 |
Records are made, manually and/or by recording instruments, during manufacture which demonstrate that all the steps required by the defined procedures and instructions were in fact taken and that the quantity and quality of the product was as expected. |
C1.8(vii) |
4 |
Any significant deviations are fully recorded, investigated with the objective of determining the root cause, and appropriate corrective and preventive action implemented; |
C1.8(xi) |
2 |
Complaints about products are examined, the causes of quality defects investigated, and appropriate measures taken in respect of the defective products and to prevent reoccurrence. |
Figure 7 presents the critical deficiencies citing Annex 1. These do not cluster as closely as the deficiencies in Chapter 1 but are rather spread over the entire annex. Most of the requirements are cited in only a single critical deficiency. Only six paragraphs are cited more than once, and the abbreviated text for these are provided in Table 5.
Table 5: 2019 Critical Deficiencies Cited in Annex 1
Critical Deficiencies |
||
Paragraph |
# |
Short Version of Text |
A1.18 |
4 |
Where aseptic operations are performed, monitoring should be frequent, using methods such as settle plates, volumetric air, and surface sampling (e.g., swabs and contact plates) … |
A1.20 |
3 |
Appropriate alert and action limits should be set for the results of particulate and microbiological monitoring. If these limits are exceeded, operating procedures should prescribe corrective action. |
A1.8 |
2 |
Clean rooms and clean air devices should be routinely monitored in operation and the monitoring locations based on a formal risk analysis study and the results obtained during the classification of rooms and/or clean air devices. |
A1.9 |
2 |
For Grade A zones, particle monitoring should be undertaken for the full duration of critical processing, including equipment assembly, except where justified by contaminants in the process that would damage the particle counter or present a hazard, … Monitoring during simulated operations should also be performed. The Grade A zone should be monitored at such a frequency and with suitable sample … |
A1.54 |
2 |
It should be demonstrated that air-flow patterns do not present a contamination risk, e.g. care should be taken to ensure that air flows do not distribute particles from a particle generating person, operation or machine to a zone of higher product risk. |
A1.64 |
2 |
Precautions to minimize contamination should be taken during all processing stages including the stages before sterilisation. |
Figure 8 shows 11 annexes and chapters associated with a subset of the major deficiencies and the number of times they were cited during inspections both in the U.K. and outside the U.K. (ROW). In addition to these 11 chapters and annexes shown in Figure 8, major deficiencies were also identified in Chapter 2, Chapter 7, Chapter 9, Annex 2, Annex 3, Annex 6, Annex 8, Annex 9, Annex 12, Annex 17, and Annex 19. More GMP chapters and annexes were cited in major deficiencies than were cited in critical deficiencies. Among the major deficiencies, 31 percent are associated with Chapter 1, 29 percent are associated with Annex 1, 10 percent are associated with Annex 15, and 9 percent are associated with Chapter 4. Shortcomings in quality systems clearly lead the list of both critical and major deficiencies, demonstrating the agency’s focus on the importance of a sound quality system to GMP compliance. Annex 1 ranks a very close second, emphasizing the prioritization of the manufacture of sterile products during inspections.
Conclusions
We conclude Part 1 after presenting an overall view of MHRA GMP inspection deficiencies from 2019, including trends from previous years. We have looked at differences year over year, and in 2019 we show the differences between inspections conducted in the U.K. and those conducted outside the U.K. Overall conclusions include:
- In 2019, the MHRA continued to conduct fewer inspections year over year. The percentage of inspections conducted in the U.K. increased slightly, and those outside the U.K. decreased by almost half since 2015. It will be useful to monitor whether the MRA with the FDA results in a decrease in the number of inspections of sites that they may both inspect. Because the MHRA only conducted five inspections in the U.S., it will be difficult to determine if the MRA with the FDA results in a decrease in inspections in the U.S.
- It is no surprise that Quality Systems, Chapter 1, continues to be first among the areas cited in inspection deficiencies, regardless of classification. It has remained in the number one position for all four years covered in this article.
- Critical deficiencies constitute just under 3 percent of the total deficiencies identified in 2019, and these are associated primarily with Chapter 1 and Annex 1. Approximately 37 percent of critical deficiencies cite requirements in Chapter 1, and approximately 22 percent cite requirements in Annex 1. It is noteworthy that among the inspections conducted outside the U.K., critical deficiencies make up 5 percent of the deficiencies identified.
- Among the major deficiencies that constitute approximately 40 percent of the total deficiencies, Chapter 1 again leads the group with just over 600 deficiencies. The next two include Annex 1 with almost 600 deficiencies and Annex 15 with approximately 200. Clearly, Quality Systems is the clear leader as it is for critical deficiencies.
- Computerised Systems, Annex 11, remains in the top 10 for both critical and major deficiencies, reinforcing the importance of this area to data integrity and the regulator’s focus on the control and management of electronic data. This year the critical deficiencies citing Annex 11 were identified at sites outside of the U.K.
Hopefully, the MHRA will continue to publish data in the Excel format in the future and expand to include its GCP and GDP inspection findings. It would also be useful for the MHRA to publish the actual text of critical deficiencies from the various areas in future years as it did in the past. But in the absence of that, the publication of these data is valuable and appreciated by the industry.
About The Author:
Barbara Unger formed Unger Consulting, Inc. to provide GMP auditing and regulatory intelligence services to the pharmaceutical industry, including general GMP auditing and auditing and remediation in the area of data management and data integrity. Her auditing experience includes leadership of the Amgen corporate GMP audit group for APIs and quality systems. She also developed, implemented, and maintained the GMP regulatory intelligence program for eight years at Amgen. This included surveillance, analysis, and communication of GMP related legislation, regulations, guidance, and industry compliance enforcement trends. Unger was the first chairperson of the Rx-360 Monitoring and Reporting work group that summarized and published relevant GMP and supply chain related laws, regulations, and guidance. She is currently the co-lead of the Rx-360 Data Integrity Working Group. You can contact her at bwunger123@gmail.com