Aggregation 101: Connecting The Dots Between Pharma Serialization And Track-And-Trace
By Jerry Martin
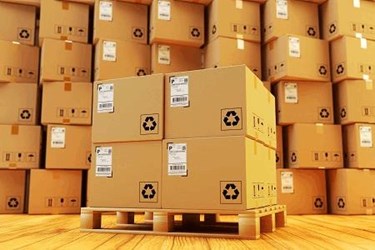
From “serialization” to “coding” to “track-and-trace,” the pharmaceutical industry is rampant with terms that point to the quest for transparency. The latest of these is “aggregation,” a burgeoning method of data collection aimed at simplifying inventory and the supply chain. While still in its infancy, the technique can help to combat counterfeiting, theft, inefficiencies, and confusion as a whole. Yet, with every new process comes challenges, requiring manufacturers considering aggregation to seek best practices for implementation.
Building Parent-Child Associations
The pharmaceutical industry defines aggregation as a process in which identification information about a case of products is collected and built upon at every stage throughout the supply chain. Starting at the packaging stage, each individual product receives its own unique serial number before being placed with other serialized units into a case, which is in turn assigned a group number. Depending on the shipment’s journey, this parent-child coding system can be continued, with numbers assigned to pallets and further identification established.
While relatively straightforward and simple, this information-gathering process builds valuable links between units and full cases of products, documenting the packaging process and quickly informing any subsequent handlers of exactly which units they’ll find in any given case. In this way, aggregation helps to connect the dots between serialization and track-and-trace operations.
Drivers For Transparency
Consumer demand for trustworthy, safe products continues to drive the need for traceability and transparency, and government regulations aren’t far behind. Not currently mandated by law in any country, aggregation is still often regulatory agency-recommended due to its ability to meet policies that are in place, like the U.S. Drug Supply Chain Security Act (DSCSA).1
Furthermore, aggregation is expected to grow in other countries in the coming years, due to the high rate of counterfeiting plaguing the pharmaceutical industry across the globe. The World Health Organization has estimated that 10 percent of medical products in low- and middle-income countries alone are substandard or falsified, pushing manufacturers to seek new methods of protection to avoid patient risk and subsequent commercial and legal repercussions.2 Beyond the concern of counterfeit products, pharmaceutical brands also face threats of theft, due to the high value and specialization of many drugs.
Mitigating Risks With Records
Aggregation can play a role in fighting forgery and theft through its ability to verify authentic products with essentially one glance. Cases using an aggregated system can be identified by their exterior parent numbers, allowing product receivers to scan one code and identify what is in the entire shipment. This provides more tamper evidence, eliminating the need for someone to open up the case or bulk multi-unit container and handle and scan each individual unit. It also means the cases can move through checkpoints in the supply chain and be verified, logged, and pushed on to the next step without fear that someone has manipulated, stolen, or replaced the goods with imitation products before resealing the case. This is critical as a shipment moves along in its path to the consumer, as distributors can know exactly which units their customers will receive and minimize the chances of interference.
Should a pharmaceutical manufacturer face a recall, aggregation can assist the company with zeroing in on the exact units in question and flag them for disposal. This limits product waste, for which costs can be so high that they can quickly exceed the cost of implementing aggregation. While some suppliers rely on serialization for this kind of assessment, serialization on its own does not provide the same benefits as aggregation, as the lines between which products are tainted and which are untouched are less clearly defined. The ability to pinpoint specific batches of product can also be helpful in the case of theft, where a handler can simply identify which logged case number is absent and avoid opening numerous cases to identify which serial numbers are missing — a time-consuming process of elimination.
Boosting Supply Chain Speeds
The parent-code verification of aggregation also provides tremendous opportunities for improved efficiency and organization. The process helps to simplify inventories and cycle counting, streamlining operations, and shortening downtime between each stage of the supply chain. Scanning one number takes guesswork and time out of the logging process, minimizing the number of units that must be hand counted.
Another benefit of aggregation is its ability to facilitate compliance with downstream trading partners that are using serialization. When information is logged properly, wholesalers and third-party logistics providers can make immediate assumptions about individual products from their group numbers and record any movement of those units without opening a single case. This serves as a critical security measure, as individual units can be scanned and tracked while remaining untouched and protected. It also eliminates the need to break down packaging to the smallest level and then repack an entire case, keeping shipments moving with minimal slowdowns.
Challenges Worth Considering
With the regulation of supply chains still a few years off, adopting aggregation may not necessarily be at the top of every manufacturer’s or distributor’s list —although distributors will need to utilize full track-and-trace capabilities by 2024, especially in applications that bundle skids of different drug cases or that break larger cases into smaller sizes. As with any new technology or process, the cost of entry is significant, and the result is a market that is gradually implementing the method. While a 2018 readiness survey conducted by the Healthcare Distribution Alliance (HDA) indicated nearly 70 percent of respondents planned to aggregate data on all SKUs by November 2019, these organizations likely include larger industry players equipped to make the production change.3 In contrast, midsized and smaller pharmaceutical companies, along with distributors throughout the supply chain, may choose to hold off on making adjustments or implementing reading and computer storage/communication systems until the method becomes more commonplace or the investment becomes more feasible.
In addition, when bringing aggregation into the packaging process, pharmaceutical manufacturers can face output challenges if the new technology does not pair well with existing equipment. These systems can run most efficiently when built in line with the rest of the production setup, rather than as an afterthought or add-on. With this being the case, manufacturers and distributors should consider implementing aggregation to their lines in conjunction with other equipment upgrades and updates, ensuring the technologies work well in tandem.
Finally, while aggregation’s data collection technique provides valuable, detailed information to parties along the supply chain, the system is only as reliable as its equipment and operators. The information must be highly accurate and consistent, or it can cause major chaos in the supply chain and invalidate any logged data. Faulty equipment at the case packing stage or during any checkpoint can compromise the entire system. If at any point the serial numbers in a particular case do not match the log, the products are considered unverified and are no longer safe to sell.
Emerging Solutions
As data collection and tracking methods continue to advance, pharmaceutical companies and distributors can utilize new technologies aiming to minimize error, such as automation-assisted packing stations. For example, the practice of adding cameras and label printers to existing case packers is a viable way to log groups of individual serialized units. As the units are packed, the camera can take a photo of the grouping and connect that image to a parent number, which is immediately printed on a label and affixed to the case.
While these photo records can be transferred to a server manually, the most foolproof method of collection is to connect the camera setup to a central software that will automatically relay information hierarchies to a master location. This real-time collection can provide greater assurance over manual data capture — especially when dealing with larger product volumes. In the same vein, modular software that can simultaneously pull aggregated data from separate lines or sites can ensure that all tracking information reaches a central location, regardless of the production and packaging setup.
When it comes to accuracy, logging individual numbers after packing and sealing the case likely provides the most trustworthy information. A scan at this stage would guarantee no products have fallen into or out of the case prior to it being sealed. While the idea of logging serial numbers when they’re no longer visible may sound difficult, this can be achieved through the use of radio-frequency identification (RFID) technology. By using electromagnetic fields to automatically gather information from nearby items, RFID can determine the contents of a case without the use of visual aids. As a case runs through an RFID reader, the technology can sense the individual units — even through multiple layers of packing materials — and pair those tracking numbers with a parent number. Using this method can virtually guarantee coding accuracy, without interfering with the existing packing method.
Still, the implementation of RFID for this application may be far off, as a majority of companies still prefer to use 2D barcodes. Although these barcodes traditionally require direct scanning and will be unseen once packed, new printing techniques are making aggregation clearer and easier. In addition to a label containing a barcode, expiration date, etc., a temporary 2D barcode is inkjet-printed onto the bottom of a bottle in a particular batch. These two codes are linked before the item is bundled with other units, shrink-wrapped, and given a group label. The bottoms of the bottles are visible through the shrink wrap, making identification of units possible even after bundling. When these “innerpacks” are placed in a case, an automated packing system photographs the group numbers and assigns a parent number to the case. As a result, this process creates more chain links between the original serial numbers and the final case number than simply pairing the unit numbers with the case number, providing a deeper level of specification.
References:
- https://www.fda.gov/drugs/drug-supply-chain-integrity/drug-supply-chain-security-act-dscsa
- https://www.who.int/news-room/fact-sheets/detail/substandard-and-falsified-medical-products
- https://www.hda.org/~/media/pdfs/industry-relations/manufacturer-readiness-survey-results-report.ashx
About The Author:
Jerry Martin is an independent consultant to pharmaceutical manufacturers and equipment suppliers for filtration, single-use manufacturing, marketing, business development, and regulatory compliance. He was previously SVP, marketing and global scientific affairs, for Pall Life Sciences, where he served the pharmaceutical, biotech, medical device, and vaccine industries for over 37 years. He is currently chairman emeritus of the Bio-Process Systems Alliance, the single-use manufacturing trade association, and a member of the USP Expert Panel on Plastic Systems Used for Manufacturing Pharmaceutical Products. He holds an M.Sc. in microbiology from the University of Toronto.
Find More Answers At Healthcare Packaging EXPO
As the pharmaceutical industry continues to advance and uncover new supply chain technologies, a holistic software solution may be the answer to meeting a range of track-and-trace requirements across the globe. Until then, manufacturers and distributors can stay on the forefront of industry best practices for aggregation by attending Healthcare Packaging EXPO 2019, which will bring the latest and widest range of equipment solutions and innovations across the supply chain to 5,000 pharmaceutical, biopharma, nutraceutical and medical device professionals.
Featuring 250 exhibitors, Healthcare Packaging EXPO will offer 100,000 net square feet of solutions and attract a predicted 5,000 attendees. Additionally, the co-located PACK EXPO Las Vegas will showcase innovations from more than 2,000 exhibitors spanning over 800,000 net square feet of exhibit space. The two shows will bring together more than 35,000 packaging professionals from around the world to explore state-of-the-art equipment and materials. In addition to the technologies on display, Healthcare Packaging EXPO will offer educational and networking opportunities as well as industry-specific events. Attendees will enjoy full access to the PACK EXPO Las Vegas show floor and all show features.
Registration, which includes access to both PACK EXPO Las Vegas and Healthcare Packaging EXPO, is $30 through Aug. 30 after which the price increases to $100. For more information and to register online, www.hcpelasvegas.com.