Advanced Isolator Tech Boosts Manufacturing Efficiency And Quality
By Gregory Benzel and Michael Jack, Jubilant HollisterStier
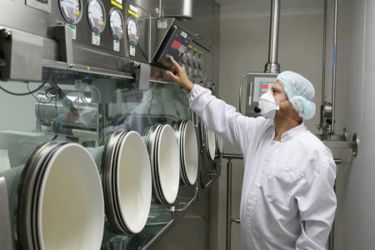
The current expectation among both pharmaceutical executives and regulators is that most, if not all, new line installations utilize isolator technology rather than traditional clean rooms. Jubilant HollisterStier’s (JHS) advanced isolator technology offers a solution that can scale alongside production to fulfill increasing demand without compromising quality or safety.
Constructed as part of a $92M, 50,000-square-foot expansion at JHS’ Spokane, Wash. production facility, production Line 3 delivers on that expectation. Line 3, a high-speed liquid filling line with 100% weight-checking, is supported by state-of-the-art isolator technology with automated H2O2 bio-decontamination, two new lyophilizers capable of frozen shelf loading, three full-service compounding suites, and disposable single-use technologies. The result is not just additional capacity, but also enhanced product quality, yield, and manufacturing speed.
Partnering with JHS provides you with immediate access to cutting-edge sterile manufacturing, supported by advanced isolator technology and full cross-functional involvement by JHS project teams throughout development and production. Meet increased demand for sterile injectables while eliminating the capital investment of expanding or upgrading manufacturing facilities, as well as minimizing timelines and regulatory hurdles.
Get unlimited access to:
Enter your credentials below to log in. Not yet a member of Bioprocess Online? Subscribe today.